Stay updated on news, articles and information for the rail industry
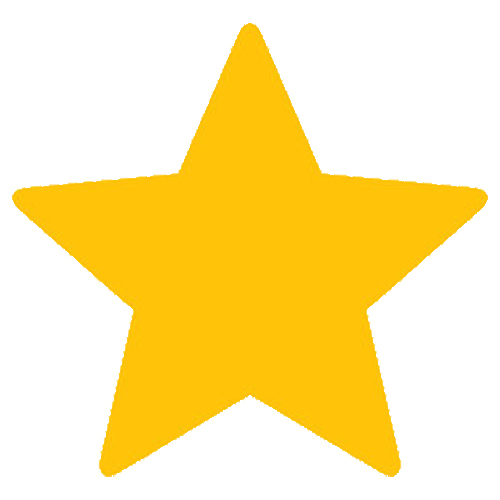
August 2022
Rail News: C&S
Product update: Wheel detection
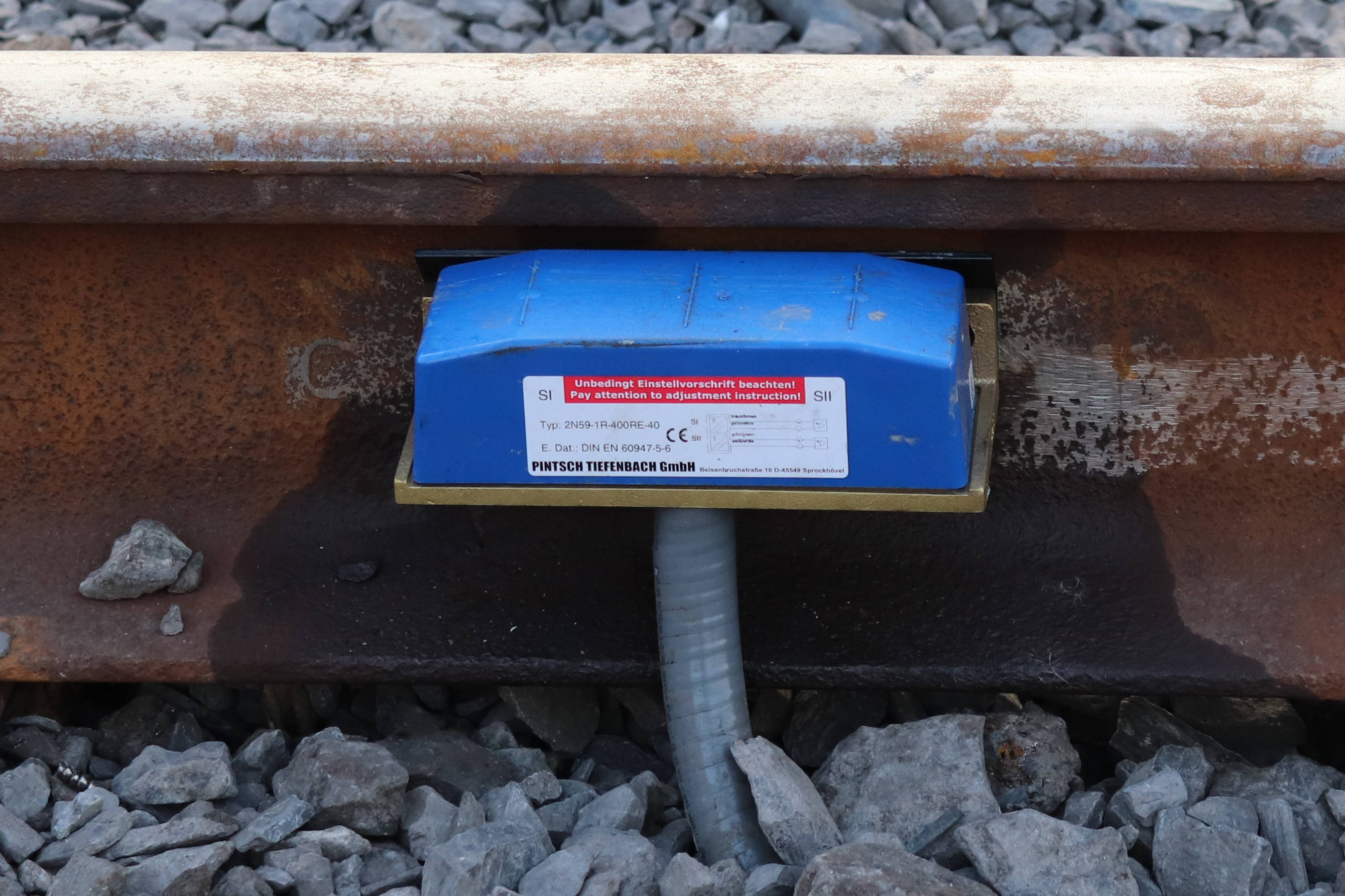
Compiled by Grace Renderman, Associate Editor
Pintsch North America Inc.
While wheel sensors may seem to be simple devices, a deeper look into the requirements and solutions needed for reliable wheel sensor performance reveals a complex engineering problem due to the need to function in all weather conditions, Pintsch North America Inc. officials said in an email.
Wheel sensor performance must remain consistent across all temperatures and humidity levels, from arctic conditions to extreme desert heat. Sensors must work when they are covered in snow, ice, dirt, grease and contaminants. Some wheel sensors even work when temporarily immersed underwater due to minor flooding, company officials said.
Pintsch North America manufactures wheel sensors used for rail-yard control applications, grade crossings and interlocking systems. Any type of virtual track circuit can be designed and built around wheel sensors, company officials said. Applications include overlays atop existing track circuits, traffic light pre-emption retrofits, switch protection and automated industrial loading and unloading processes, gate control devices and blue signal systems and derails in rail-car and locomotive shops.
With no direct electrical connection to the track, wheel sensors are immune to a variety of shunting sensitivity issues. They also offer significant isolation from lightning ingress, affording a higher level of reliability than traditional track circuits, company officials said. The company provides full-service engineering and manufacturing to design custom solutions built for the Pintsch Virtual Track Circuit.
L.B. Foster Co.
L.B. Foster Co. provides wayside technology to monitor safety and increase network velocity on the digital railway. L.B. Foster subsidiary Salient Systems Inc. recently launched the Mk-IV system, a next-generation wheel impact load detector (WILD), that continually monitors wheel health to ensure safe and productive train operations. The new system features technology designed to improve strain-gauge accuracy. Salient Systems invented the industry’s first WILD in 1984, L.B. Foster officials said.
“Mk-IV now incorporates many years of customer-driven advancements in technologies and features that make the new system easier to maintain, while also offering detailed remote site health reporting,” said Michael O’Connell, L.B. Foster’s technology sales, product and business development manager for the Americas.
The Mk-IV is mounted directly to the rail, which allows for more data collection points compared to a traditional WILD, company officials said. The system measures impact force caused by damaged wheels and provides callouts on a per-train basis, as well as periodic reports through its web-based wheel data management system portal.
Available as an add-on to the Mk-IV or as a standalone wayside installation, the company’s weigh-in-motion system reduces derailment conditions and infrastructure damage by detecting overloaded or imbalanced vehicles at track speeds, company officials said. It also provides accurate vehicle weights and alerts on overload as well as side-to-side and end-to-end imbalance conditions.
TransmetriQ
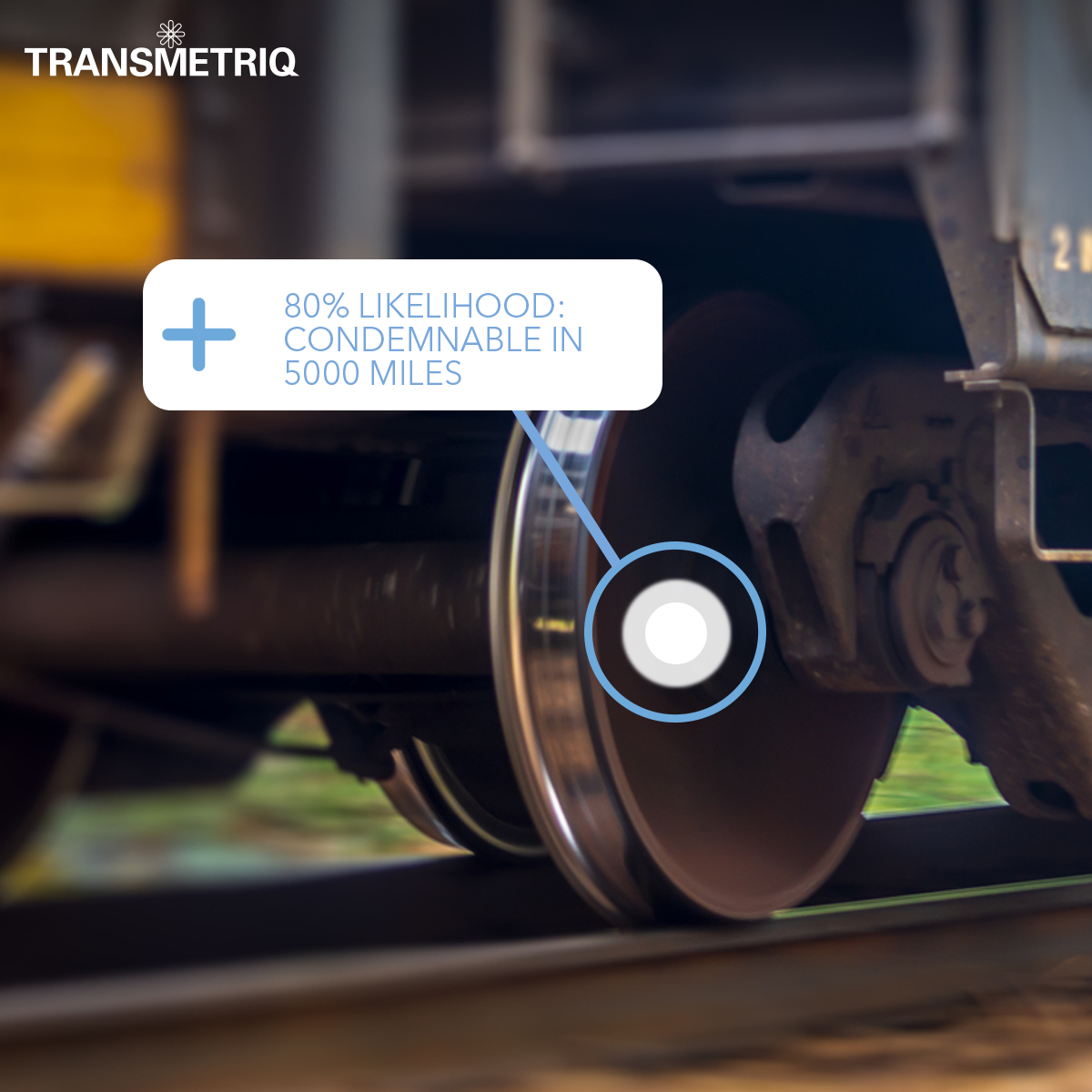
TransmetriQ is using artificial intelligence and machine learning techniques to improve component health tracking, including wheelset intelligence. Using data from the Railinc Corp. Component Tracking program and utilizing insights from millions of wheelset lifecycles, the company’s AI models predict the probability that a wheelset will reach condemnable status within a certain mileage window.
With this predictability, car owners can route cars to a preferred shop for repairs and optimize decisions when a car is already at the shop. Knowing when a wheelset is likely to need replacement allows owners to choose repair timing — which increases equipment availability and allows proactive management of maintenance spending, company officials said. Shops also can leverage predictive analyses to identify repair opportunities.
The ability to monitor contracted equipment and identify at-risk rail cars enables equipment owners and lessors to keep equipment in productive service. It also creates more efficient use of existing fleets (rather than adding equipment to maximize availability), reduces the risk of incurring foreign repairs and optimizes maintenance investments, company officials said.
Frauscher Sensor Technology USA Inc.
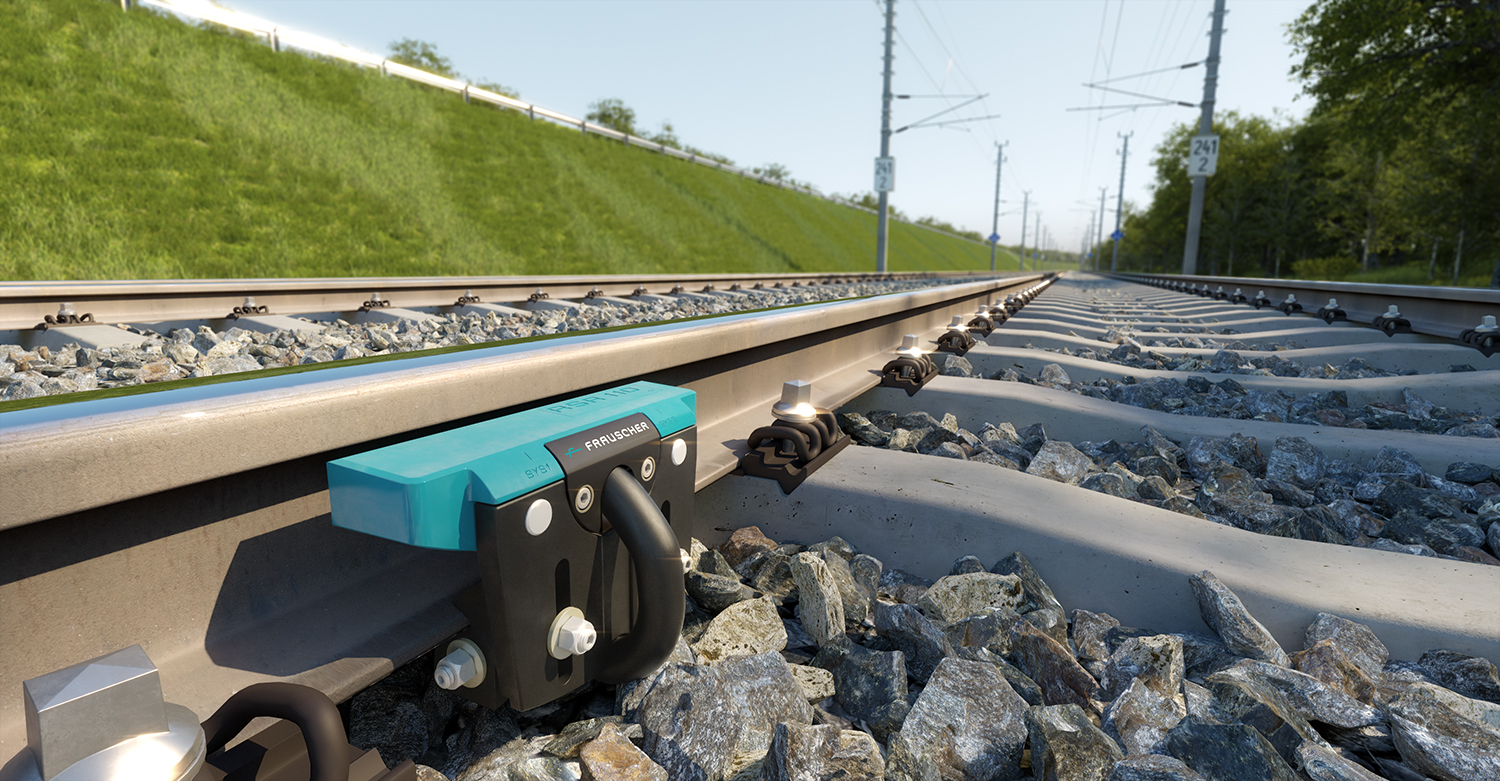
The RSR110 wheel sensor offers an alternative to conventional detection methods, Frauscher Sensor Technology USA Inc. officials said. Application examples include triggering trackside monitoring equipment like automatic equipment identification readers, hot-box detectors and vision monitoring systems; tracking trains in yards; calculating rolling resistance and speed in hump yards; and detecting accurate car position for freight-car loading and unloading.
RSR110 wheel sensors are inductive, contactless, IP68-rated and water- and dustproof. Sensor reliability is unaffected by snow, ice, vegetation or temperatures between -40 F and 185 F. Frauscher wheel sensors also function properly independently of rail shunting, so the RSR110 remains reliable even when track and ballast conditions have deteriorated, company officials said.
The sensors can be installed without drilling the rail and they can be calibrated from an off-track location, either directly from the wayside evaluator module or remotely. The sensor requires minimal maintenance, limited to infrequent visual inspections, meaning maintenance activities can be completely avoided during cold or rainy seasons, company officials said.
Siemens Mobility
The Clearguard Axle Counter series supplies track section status and diagnostic information, permitting safe and efficient signaling operations for train speeds up to 250 mph, Siemens Mobility officials said. It includes an axle-counting tool that can be implemented on multiple systems and applications with a compact design.
The technology offers a redundant product architecture and dual ethernet network for high availability. Combined with the company’s digital solutions, the system also features advanced diagnostic reporting, such as maintenance alarms and live asset health status.
Live monitoring and remote diagnostics are available through an internet connection. Status information and stored log files can be called up in the form of graphics and data lists, and LED indicators on the module allow for simple diagnostic testing on site, company officials said.
The Clearguard series operates on double-sided technology – which supports more complex circuitry – without electronics on the sensor, making it less sensitive to environmental changes and providing high reliability and strength for mainline, mass-transit and industrial rail applications, company officials said. The sensors are installed onto the track by either drilling or clamping to the rail.
voestalpine Signaling USA Inc.
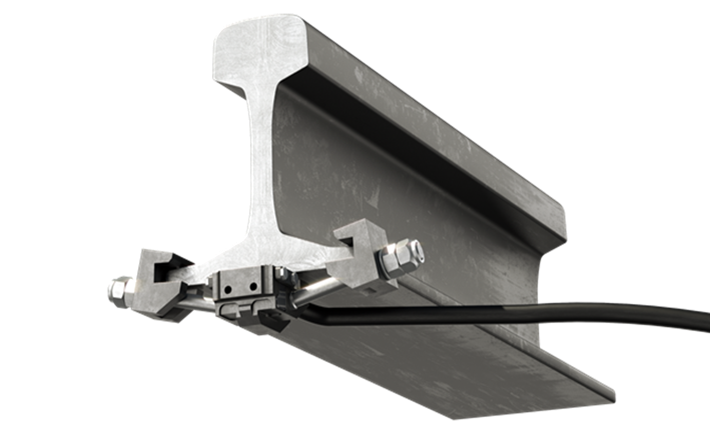
voestalpine Signaling USA Inc.’s wheel defect detection and weigh-in-motion systems measure every wheel of the train fleet on a continuous basis, checking for deviating force levels during normal train operation, voestalpine officials said. The systems also function as a dynamic rail scale to measure vehicle weight and load distribution on each passage so that an imbalance or overload can be recognized in time. Assistance for optimal payload usage is also available.
Force exerted on the rail is captured by optical sensors clamped under the rail, with rail deformation measured at a high scanning rate. Every wheel is identified during a train’s passage, and data reports on weights and defects are generated accordingly. Alarms are also displayed in real time, and defective wheels are identified together with their exact positions under the vehicle.
The systems’ software differentiates various types of wheel defects, like wheel flats, out-of-roundness and polygonization. The “small, lightweight, energy-efficient design of the module allows for easy co-location with other diagnostic functions in a cost-effective way,” company officials said. The sensor’s fiber-optic technology in design provides electromagnetic compatibility with any rail system.
Email question or comments to grace.renderman@tradepress.com.