Stay updated on news, articles and information for the rail industry
October 2019
Rail News: CSX Transportation
Class I focus: Operational and efficiency gains can create a virtuous cycle for CSX
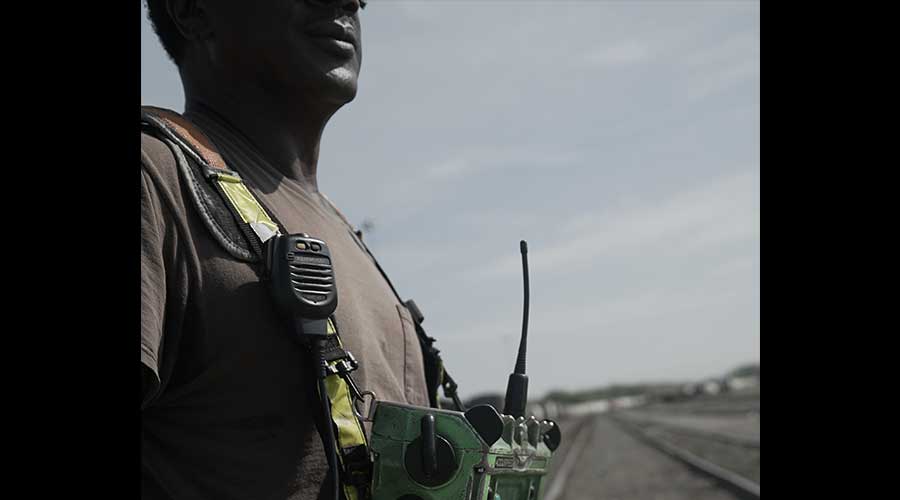
By Jeff Stagl, Managing Editor
Transformation. Re-engineering. Changeover. Those are some of the words that describe what CSX is attempting to do to significantly alter the way the organization operates and conducts business.
Becoming a streamlined, nimble and efficient organization will enable the Class I to respond faster to today’s transportation supply chain needs and offer a more superior service product, CSX leaders say. An effort that began two years ago to change the business model and remold the railroad — primarily because the Class I had been underperforming both operationally and financially — is gaining momentum, they say.
Two of the biggest drivers behind that undertaking are the implementation of precision scheduled railroading (PSR) and adoption of numerous technologies. Providing such potential benefits as service reliability, operating efficiencies and reduced network complexity, PSR has shifted CSX’s operational focus from moving trains to moving individual rail cars. The operating strategy is designed to minimize rail-car dwell time and classification events, reduce locomotive requirements, balance train movements and improve asset utilization.
The company is analyzing every aspect of how the organization is run, essentially trying to re-engineer every business process, said CSX President and Chief Executive Officer James Foote Sept. 11 at Morgan Stanley’s annual conference in Laguna Beach, California.
“It’s simple engineering, taking out every inefficient step that you can along the way,” he said. “It drives out all the unnecessary costs associated with all that unnecessary work you used to do, but it streamlines and improves the quality of our product.”
To keep the efficiencies coming, the railroad’s braintrust continues seeking ways to balance the network, consolidate and lengthen trains, eliminate train stops and car dwells, use less rolling stock and rationalize terminals. For example, the Valleyfield intermodal terminal in Quebec, Canada — now considered expendable because of traffic flows — will close this month.
They’re also trying to show a willingness to make unconventional decisions that can help drive change. In August, CSX named Adam Longson as its first-ever vice president of energy to manage an energy portfolio that’s been consolidated to include export and domestic coal, liquefied petroleum gas and crude oil. That followed the May appointment of Farrukh Bezar — who founded transportation and logistics advisory firm Lynwood Partners — as the railroad’s first chief strategy officer.
More recently, CSX sold an unwanted line to a competing Class I — which doesn’t happen often — as part of an initiative to generate value from non-core assets. CN in late August acquired CSX’s 220-mile line between Valleyfield, Quebec, and Woodard, New York.
Such moves are vital to more clearly understand the entire supply chain and global trends, and to become more responsive to changing transportation needs, said Foote.
“The days of us going to the customer and saying, ‘Hey, what have you got for me today?’ are done. We’ll just continue to lose market share,” he said. “So we need to be proactive in going to the customer and explaining to them that we have some options and some solutions for them … [to] save money by using rail transportation or by working with us on a logistical standpoint.”
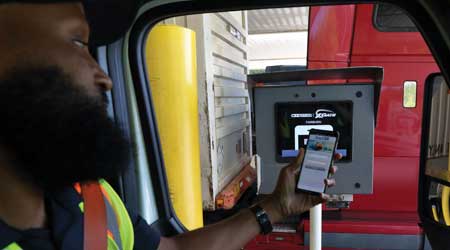
CSX needs to be a consistent performer, too, to attract and retain customers. If a shipment is promised in 3.5 days, it needs to arrive in 3.5 days every time, said Foote.
Recent performance metrics show CSX’s average transit time has been reduced by about two days and reliability has significantly improved. The railroad is logging better trip plan compliance and velocity measures of late — which are up by double-digit percentages year over year — and less terminal dwell time, while operating much fewer locomotives and cars.
From Q1 2017 through Q2 2019, the number of active locomotives and cars on line fell more than 30 percent and 20 percent, respectively. Currently, active locomotives total about 2,500 and cars on line, about 117,000.
Operational and efficiency gains can create a “virtuous cycle” for CSX, one that begets a more attractive transportation product and more business at a lower operating cost, said Foote. The cycle starts with building service, reliability and confidence in the customer base to build more business.
As customers recognize that operational performance is much better, market share can be regained in business segments the railroad lost over several decades due to inconsistent service, said Foote.
“As we focus on improving throughput and improving the way the railroad runs, we drive up these metrics that show performance. [That] then improves efficiency and drives assets out of the network, improving the cost structure, [and] at the same time improving the quality of the service, which then goes back around and you start over again,” he said. “And you do it over and over and over again. You just simply keep grinding it out.”
Managing mountains of data
Another key continuous-improvement component of the cycle? Technological adoptions. The company needs to keep leveraging the latest technologies, such as artificial intelligence, to help drive efficiencies, enhance safety and improve the customer experience, CSX leaders believe.
“We want to take advantage of new technological developments … that can help us see into the future and make better business decisions,” Foote said May 30 at Sanford C. Bernstein & Co. LLC’s annual conference in New York City.
It’s all about figuring out what to do with mountains of data and adopting advanced tools to make better business decisions, he said.
“We’re data freaks. If you can’t measure it, you can’t fix it. And so we are constantly trying to figure out different ways of capturing data,” Foote said.
Information gathered today doesn’t necessarily provide insight as to what might happen tomorrow, so CSX also needs to better exploit data to be more predictive, he said.
The Class I strives to continuously develop its own tools as well as tap existing and emerging technologies to help meet strategic objectives and reinforce the operating plan, says CSX SVP and Chief Information Officer Kathleen Brandt.
“We want to be the best in the industry, and technology helps us do that,” she says.
In-house development generates key benefits, says Jamie Boychuck, who was named executive vice president of operations on Oct. 2.
“We can develop technologies on our own that no one has, or that make the customer experience better,” he says.
The push for self-developed tools has been supported by a growing technology team, says Brandt. Since 2017, CSX has hired 300 individuals who are charged with helping develop various technologies.
An app for terminal entry in a snap
One of the team’s successes is XGate, a mobile application for intermodal terminals. Developed about 18 months ago, XGate is designed to prompt more efficient truck-traffic flow at terminals by expediting in- and out-gate processes and terminal tasks. Truckers can use the app to submit paperless information prior to arriving at a gate, obtain container drop-off and pickup locations, and receive an electronic gate receipt.
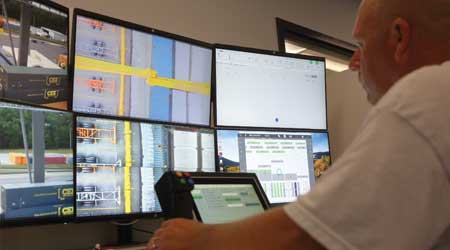
XGate saves time — truckers can enter a terminal in about 30 seconds instead of in minutes by scanning a barcode on their mobile device. About 14,000 drivers have used the app over the past 90 days and more than 27,000 drivers have
“We are seeing a high adoption rate among truckers,” says Brandt. “They realize it saves them time, and is intuitive and easy to use.”
CSX also has developed a gate reservation system that’s been rolled out at all 31 intermodal terminals over the past year. Truckers use the system — first deployed in June 2018 — to book appointments to return empty containers or drop off loaded ones. The system enables CSX to match the number of containers entering terminals to the number of slots on an outbound train and available storage space.
“Truckers can get guaranteed slots on a train, and then can tell their customer when a container will get there,” says Boychuck. “We know how many containers will be brought in every day. It helps clean up congestion.”
There’s another form of automation that CSX has been employing at several intermodal terminals for the past two years: unmanned cranes. Supplied by Austrian manufacturer Kuenz Cranes, the equipment is remotely controlled and guided by a worker in an office using GPS coordinates.
CSX currently employs the cranes at its intermodal terminals in Winter Haven, Florida, and Atlanta (Fairburn). The railroad is considering whether to use them at other terminals, says Boychuck.
Other recent technological advances include new yard intelligence and network intelligence tools. An advanced software solution designed to optimize yard operations and maximize asset efficiency, the yard intelligence tool helps improve the visibility of current yard status, including inbound trains and outbound schedules.
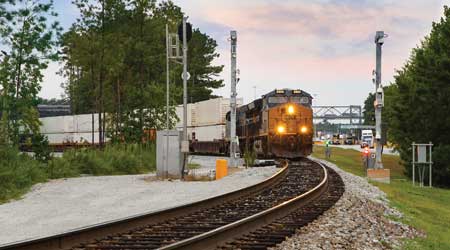
It can algorithmically optimize switch priority, class track assignments and train build processes. The tool improves trip plan performance, which leads to better service for customers, says Brandt.
Of algorithms and analyses
Meanwhile, the network intelligence tool is a key component of providing efficient service via the operating plan, she says. Designed to analyze both historical traffic patterns and forecasted demand, the tool features a set of sophisticated algorithms that help schedule trains more optimally.
Network intelligence also plays a role in minimizing fuel consumption and maximizing the utilization of locomotives and crews.
The railroad also is tapping technology to improve fuel efficiency. For example, CSX uses Trip Optimizer, which Boychuck says is like cruise control for locomotives. The technology was developed by Wabtec Corp. subsidiary GE Transportation.
The tool is designed to optimize fuel consumption based on a train’s makeup and route, and calculate an optimum speed profile based on such factors as train length and weight, and track profile. Trip Optimizer then automatically controls throttle and dynamic braking.
CSX also is working with Siemens to develop a meet/pass planner tool, which might be available in the fourth quarter. The tool is designed to better determine where trains should meet or stop, says Boychuck.
“It will help improve fuel efficiency and network fluidity,” he says. “It’s another way to leverage data.”
In the meantime, CSX is employing distributed power on all types of trains in part to help reduce fuel usage. Distributed power involves placing one or several locomotives within the length of a train that are remotely controlled from the lead locomotive.
By reducing draft forces along a train and lowering the lateral force between wheels and rail on curves because of distributed power, fuel consumption is cut.
“Two years ago, we didn’t use distributed power at all. Now, we use it on 100 trains per day,” says Boychuck.
Gathering intel
Yet another tool soon will be used by CSX to generate efficiencies of another kind. To launch in first-quarter 2020, a crew intelligence tool is under development by the technology team that will employ algorithms on historical information and other worker data to provide better insights on assigning crews, says Boychuck.
“It can take hours usually to match up crews. With the tool, we will know a crew member’s availability in the next 12 to 24 hours, and when they are rested,” he says. “We can plan crews well in advance.”
Adds Brandt: “It gives us more time to react and an opportunity to adjust, if needed.”
Overall, the adoption of many technologies will provide CSX additional operational efficiencies, with trains running closer together and more capacity freed up, CEO Foote said.
“Just like every time we run the trains a mile or an hour faster, we create capacity,” he said. “We are never done with creating efficiency in the organization.”
To notch further gains, CSX needs to speed decision-making to the level of other progressive companies, such as Uber or Google, Foote believes.
“We need to work every single day at deal speed just like our competitors do. And when we do that, when business is up and down, we should be able to respond and be much more effective in the way we do things,” he said.
All in all, the key to being a well-run company is to become an efficiently run one, Foote maintains.
“We need to always focus on making sure that we maintain our leadership position as the most efficient because it makes you a good-run company,” he said. “It makes you have a very good product for your customer.”
Email questions or comments to jeff.stagl@tradepress.com.