Stay updated on news, articles and information for the rail industry
September 2016
Rail News: Mechanical
Railroads continue to implement new technologies and processes aimed at reducing fuel usage
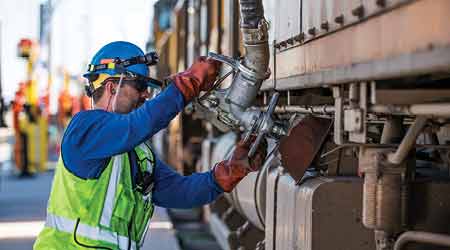
By Deborah R. Huso
With four times the fuel efficiency of trucks, railroads are “the most environmentally sound way to move freight over land,” as the Association of American Railroads (AAR) notes in the first sentence of an April 2016 white paper titled “The Environmental Benefits of Moving Freight By Rail.” Nevertheless, fuel remains one of the largest line-item expenses railroads have.
“Fuel has always been one of the biggest costs of operating trains,” says Matt Feldman, BNSF Railway Co.’s general director of fuel efficiency. “Anything we can do to reduce fuel consumption helps the bottom line.”
Accordingly, North American railroads continue to implement new technologies and processes aimed at reducing diesel usage — and their efforts continue to make a difference. U.S. freight railroads moved a ton of freight 235 miles on a gallon of fuel in 1980. By 2015, that gallon enabled them to haul that ton of freight an average of 473 miles, according to the AAR. To reduce diesel usage, railroads have:
• acquired new and more fuel-efficient locomotives;
• installed of idling-reduction technologies, such as automatic engine stop- start systems (AESS) and consist managers that automatically reduce power on unneeded locomotives; and
• developed advanced computer software systems that can perform many functions from calculating the most efficient train speed over a given route to monitoring locomotive performance to ensure maximum efficiency.
But there’s a lot more going on out there to curb diesel usage. What follows is a sampling culled from interviews, email conversations and information posted on railroad websites.
CSX: Employees key to fuel efficiency
“Getting fast and accurate information” is central to reducing fuel consumption at CSX, as are improvements in data collection and analysis to drive “fact-based refinements” in processes, says Kaitlyn Barrett, manager of corporate social responsibility.
Technology: CSX has been installing GE Transportation’s Trip Optimizer on locomotives, Barrett adds. The software calculates a locomotive’s ideal speed based on a variety of factors, including trip length, track curvature and grade, and train tonnage, to minimize braking as well as increase fuel efficiency. Currently, the railroad is testing and installing the next iteration of Trip Optimizer — SmartHPT (horsepower per ton) — which can idle select locomotives within a train to maintain track speed for additional fuel savings.
Processes: “Employees are the biggest contributors to improving fuel efficiency,” Barrett says. To that end, CSX has launched several employee education initiatives and training programs to ensure crews understand new technologies and process changes, and “how daily operations impact fuel expenses,” she adds. One example: Crews are instructed to shut off idling locomotives that aren’t slated to be in service for awhile.
Impacts: Technology enhancements and process changes have helped CSX improve fuel efficiency by more than 100 percent since 1980. In first-half 2016, CSX “saved more than 10 million gallons through fuel efficiency measures,” Barrett adds.
Union Pacific: A technology-driven team effort
Fuel accounts for about 15 percent of Union Pacific Railroad’s annual operating expenses. To continually reduce that cost, UP seeks ideas from a fuel conservation and emissions team that meets regularly.
Technology: Since 2000, UP has retired 3,000 older, less efficient locomotives and replaced them with a fleet of more than 4,300 locomotives meeting U.S. Environmental Protection Agency guidelines for Tier 0, 1, 2, 3 and 4 standards for fuel efficiency and reduced emissions, according to the railroad’s 2015 “Building America Report.” About 80 percent of the railroad’s 8,500 locomotives use AESS technology.
Meanwhile, 700 UP locomotives are equipped with New York Air Brake Corp.’s (NYAB) Locomotive Engineer Assist/Display and Event Recorder (LEADER®); 600 feature GE’s Trip Optimizer; and 300 feature EMD’s Smart Consist, which advises the engineer on the horsepower and tractive effort required for a haul and offers recommendations on throttle notch combinations for the best fuel efficiency. UP also is investigating liquefied natural gas as a potential alternative to diesel.
Processes: UP has also changed its operating practices to encourage employees to manage train speeds to better maximize miles per gallon. In addition, the railroad has integrated its network and interchange operations with other railroads to minimize delays, which can lead to unnecessary engine idling.
Impacts: In 2000, UP could move a ton of freight 375 miles on a gallon of fuel. By 2010, that had increased to 495 miles. In 2015, the number stood at 456 due in part to a different commodity mix that required more horsepower and fuel to haul.
BNSF: New power, new processes
Technology: Since 2005, BNSF has purchased 3,000 new locomotives, including 236 Tier 4 units the past two years. The new units are up to 14 percent more fuel efficient, BNSF’s Feldman says. Although he doesn’t think the Tier 4s are more fuel efficient than Tier 2 and 3 locomotives, they do reduce nitrous oxide and particulate matter emissions.
And over the course of the past 15 years, the Class I also has been installing AESS technology on locomotives; now, 95 percent of BNSF’s fleet is equipped with the systems, Feldman says.
The Class I also has purchased more than 3,100 energy management systems for locomotives, including GE’s Trip Optimizer. Installed on 7,000 locomotives in North America, the software builds an optimal operating plan based on data collected about a train’s characteristics and helps railroads save fuel as a result, according to GE. BNSF also uses more than 1,500 top-of-rail friction modification units to reduce friction and increase fuel efficiency.
Processes: If a train features more locomotives than it needs — say it has crossed the Sierra Nevada and is now cruising across the Great Plains — BNSF engineers turn off unnecessary locomotives to achieve the lowest horsepower per ton necessary to provide sufficient service, Feldman says. To achieve maximum fuel efficiency based on route characteristics, the railroad also limits how high a horsepower the engineer can kick the throttle into in an effort to achieve maximum fuel efficiency based on the characteristics of the route.
“Almost the entire railroad is set up to analyze engineers’ fuel conservation habits,” says Aaron Ratledge, BNSF’s general director of operating practices.
Engineers who achieve high rates of fuel efficiency receive gasoline reward cards as an incentive.
Impacts: Between 2005 and 2015, BNSF’s fuel efficiency has improved 12 percent as measured in gross ton miles per gallon, Feldman says. That figure increases to 18 percent when calculated as revenue ton miles per gallon, he adds.
Norfolk Southern: LEADER plays leading role
Technology: About 80 percent of Norfolk Southern Railway’s more than 4,300 locomotives feature NYAB’s LEADER, says Neville Wilson, NS assistant vice president of mechanical. A locomotive computer system designed to improve fuel efficiency and boost safe handling for long-haul trains, LEADER provides locomotive engineers with real-time information about a train’s operating conditions. NS first began testing LEADER in 2003. Currently, less than 10 percent of the Class I’s locomotives use GE’s Trip Optimizer. The railroad also employs AESS technology on 85 percent of its locomotives, about 50 of which are Tier 4 compliant.
Processes: While NS does not have the employee fuel conservation incentives BNSF offers, the railroad does monitor engineers’ diesel usage — and includes it as one of the factors evaluated for an incentive program directed at overall expense reduction in operations.
Impacts: Year over year for the last four to five years, NS has seen a 1 percent improvement in fuel efficiency due to implementation of new diesel-saving technologies, Wilson says. In second-quarter 2016, the railroad’s operating expenses were down 11 percent compared with the total from same 2015 period due in large part to fuel cost reductions, according to the Q2 report.
OmniTRAX: Technology to burn
Technology: OmniTRAX Inc. has installed 35 auxiliary power units on locomotives on its “cold” railroads, where temperatures are below freezing for a good chunk of the winter, to allow engines to be turned off when not in use yet not risk freezing, says Sergio Sabatini, chief operating officer. Doing so has saved more than 322,000 gallons of fuel since units were installed, he adds. OmniTRAX — which owns 20 short lines that operate in 12 states and three Canadian provinces — also has installed AESS technology on its entire fleet.
In addition, a few OmniTRAX railroads are using a GPS-enabled device supplied by Wi-Tronix LLC to connect all sensors on a locomotive — such as those that monitor speed and fuel level — via the internet. The devices can indicate the best time to fuel locomotives, Sabatini says.
Processes: OmniTRAX has changed its locomotive mix to better reflect the horsepower per ton needed to move a particular type of freight, Sabatini says. The company also has changed its maintenance programs for load testing on locomotives to twice a year instead of once. The reason: to ensure the units are pulling the maximum amount of tonnage.
OmniTRAX also conducts tri-annual locomotive inspections. Meanwhile, employees who demonstrate commitment to the efficiency and fuel-saving causes receive letters of recognition and gift card rewards.
Impacts: In 2015, OmniTRAX owned 90 locomotives and leased 31. Between June 1 and June 30, 2015, the railroad burned more than 2.3 million gallons of fuel. In the same 2016 period, with 64 owned locomotives and 37 leased, OmniTRAX burned just under 1.7 million gallons of diesel.
Conrail: A ‘proactive organizational mindset’
Technology: Since 2005, Conrail has been using GPS technology to drill down into the deep pool of data that it generates and improve asset utilization; reduce fuel consumption; and monitor crew performance and efficiency. The aim: to use the data to make informed decisions that ultimately help the railroad create more service delivery capacity.
Processes: All Conrail locomotives are monitored for mobility and energy usage, and responsibility for measured results are assigned to service delivery jobs and craft employees, says President and Chief Operating Officer Ron Batory. Locomotive shutdown compliance exceeds 95 percent when climatic conditions allow. “The proactive organizational mindset within Conrail toward fuel conservation has resulted in an overall locomotive hourly burn rate of near idle consumption on an annualized basis,” Batory notes.
Impacts: Conrail has saved $41 million in cost and 16 million gallons of diesel over the past 10 years through employee awareness and behavior accounting alone, Batory says.
Amtrak: Real fuel-reduction realized
The national passenger railroad is in the process of “conducting competitive solicitations to reduce costs” while also focusing on promotion of locomotive shutdown, use of ground power and improved inventory management to reduce the amount of diesel purchased, says D.J. Stadtler, Amtrak’s executive vice president and chief operations officer. Fuel is the railroad’s second-largest expense, he adds.
Technology: Amtrak has installed a “train communications data system” on all of its locomotives to monitor performance as well as operating and mechanical conditions, according to Amtrak officials.
The railroad also installed CWI Inc.’s rail yard data management systems at many of its fuel facilities to provide fuel inventory management, and real-time remote monitoring of metered input and output to locomotives.
Processes: The railroad’s System General Foreman’s Office oversees a fuel management team that works with environmental, operating, and mechanical team members to promote conservation efforts.
Impacts: “To date, Amtrak has reduced revenue train fuel by over 3 million gallons this fiscal year alone,” Stadtler says. That also equates to a 30,630 metric-ton reduction in greenhouse gas emissions.
Deborah R. Huso is a Barboursville, Va., freelance writer. Email comments or questions to prograil@tradepress.com.