Stay updated on news, articles and information for the rail industry
March 2016
Rail News: Mechanical
Internet of Things: AAR’s Railinc crunches Big Data to help railroads stay on top of equipment repairs
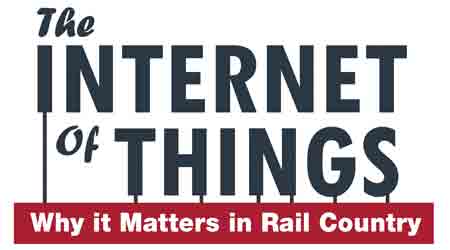
By Daniel Niepow, Associate Editor
In January 2012, Railinc Corp. rolled out a tracking program to collect data about rail-car components. The program provides railroads, car owners and repair shops with a more comprehensive view of their components’ performance so they can tackle safety issues before they arise, says Jerry Vaughn, director of asset services for Railinc, a wholly owned subsidiary of the Association of American Railroads (AAR).
The program, which uses Railinc’s Umler® component tracking registry to comb through massive amounts of data, allows the industry to "understand the depth and scope of defects identified by other processes," such as the wayside detector network, Vaughn says.
For example, the detector network might identify a safety issue with a certain type of wheel. Car owners then can use the registry to search for all rail cars associated with other wheels manufactured at the same time. If they find that these wheels have the same issue, they can send the cars off for repair before problems emerge, Vaughn says.
A partial screenshot of Railincs's Umler® component registry provides data on an axle.
As part of the tracking program, barcodes are placed on components during the manufacturing process. The barcodes allow car owners to pinpoint a component’s location.
The system originally tracked wheelsets, but was expanded in 2013 to include side frames, bolsters and couplers. Railinc later added slack adjusters and the emergency and service portion of the brake valve.
Rail industry participants on the AAR's committees determined that wheelsets had the largest impact on safety and costs, so they were added first.
"The No. 1 reason for adding a component to the tracking system is safety," adds Vaughn.
Each month, Railinc adds 25,000 to 40,000 new wheelsets to the registry, on top of a base of 6 million, Vaughn estimates.
Railinc created the database for the registry in a way that easily facilitated the addition of new kinds of components over time, says Railinc Director of Corporate Communications Patrick O'Neil.
"It's not starting from scratch; it's just like adding another page to the book," he says.
There are plans to add even more components to the registry.
"There is a long list," says Vaughn, reiterating that priority goes to components that have the greatest impacts on safety and costs.
The component tracking program is just one element of the AAR's broader "Asset Health Strategic Initiative," which was highlighted in the organization’s first "state of the industry" report issued in late January.
To help foster better decision-making about maintenance, the initiative aggregates data from wayside detectors that belong to multiple railroads. Previously, railroads could only use information gathered from wayside detectors in their own service territory.
"Where we come in is … putting that data in an actionable level," says O'Neil.
[Editor's note: This story has been changed since its initial posting.]