Stay updated on news, articles and information for the rail industry
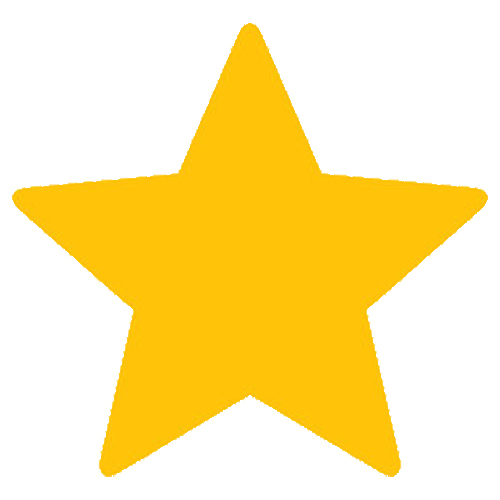
January 2007
Rail News: Mechanical
No breather in 2007 for tank-car builders
By Robert J. Derocher
When tank car builders turned their calendar pages this month, they might have been tempted to skip past 2007 and leap right into 2008. That’s how far the backlog goes for many of them.
“Our market is very, very, very hot,” says Bruce Winslow, spokesman for Union Tank Car Co. “Production is spoken for well into 2008.”
Other North American tank-car builders have similar tales to tell. A strong economy, buoyed by an unprecedented surge in production of the alternative fuel ethanol, will keep builders busy throughout ‘07 — and, likely, beyond.
Meanwhile, builders are keeping a watchful eye on Washington, D.C., where government agencies and Congress are becoming increasingly interested in hazardous-material transport (see page 9). They also want the industry to make haz-mat tank cars safer and more secure. Segments of the haz-mat industry itself are working to design a “next generation” tank car.
Just how — and how soon — the rekindled regulatory interest and redesign initiatives will impact the tank-car market remains to be seen. For now, builders will continue cranking out tank cars for customers eager to get those cars out on the rails earning revenue in what remains a very hot market.
“[The market] is sizzling,” says Toby Kolstad, president and co-founder of Rail Theory Forecasts, a rail industry consulting firm. “Ethanol shippers are lining up for cars from lessors. Builders have backlogs through 2008, even at production rates for 2007 and 2008 that are almost two times the historical maximum.”
The Ethanol Effect
Tank-car deliveries in 2006 were expected to be around 14,500, nearly 30 percent more than the 11,500 delivered in 2005, Kolstad says.
As for 2007, Kolstad expects a similarly sized jump to 18,500 tank cars. In December, the tank-car backlog stood at 34,000, more than double the 14,000-car backlog a year earlier, according to Rail Theory Forecasts statistics. The driver of the increases continues to be ethanol.
“There are a lot of new cars filling into that service,” says Jim Earl, executive vice president and chief operating officer of rail-car lessor GATX Corp., adding that about half of the 5,000 new tank cars that went into service in 2006 were devoted to ethanol service.
Tank cars make up about 65 percent of GATX’s 110,000-car fleet. The cars primarily service the chemical, food and agriculture industries. Utilization was running at 99 percent for most of 2006, Earl says — essentially, non-stop.
GATX has purchase agreements that run through 2007 with two of the largest tank-car producers, Union Tank Car Co. and Trinity Industries Inc. Another multi-year purchase contract will begin in 2008 with another major builder, American Railcar Industries (ARI).
At Union Tank Car, ethanol and bio-diesel fuels represent “an absolute growth industry,” says Winslow. And because ethanol is fairly light — a 263,000-pound ethanol tanker holds about 30,000 gallons — ethanol cars also can carry other chemicals of similar weight.
Execs at GATX and Union Tank Car are optimistic about ethanol’s prospects for continued growth, and they say it won’t come at the expense of other business. The petrochemical industry remains Union Tank Car’s top customer base, Winslow says. Adds GATX’s Earl: “We try to maintain a balance. We’re not going to short those long-term customers just to try and serve a start-up ethanol supplier.”
More capacity to build
For good reason. Even without ethanol, 2006 was a busy year for the three largest tank-car builders.
Through the year’s first three quarters, Trinity reported $100.7 million in operating profit compared with $58.1 million for the same period a year earlier. Those numbers include results from Trinity’s other businesses: barge and power equipment building, rail-car leasing and other freight-car manufacturing.
Even so, Trinity President Tim Wallace told investors during a November 2006 conference call that production capacity at some facilities would be switched over to ethanol car building during the next few quarters to meet market demand. The conversion will help Trinity meet increasing tank-car demand, Wallace said.
Similarly, Union Tank Car in June 2006 opened its third production facility, a plant capable of producing 70 cars a week with 850 employees at full capacity. The Alexandria, La., plant — the company’s largest — already was running at half of its capacity just a few months after opening, Winslow says. “We’re pedal to the metal at all of our facilities,” he adds.
Officials at ARI also are looking forward to a more productive ‘07. In April 2006, a tornado damaged the builder’s Marmaduke, Ark., plant. The storm destroyed the facility’s inbound material processing area and a nearly completed building that would have received inbound materials and stored inventory. It also wrecked material handling, plate steel blasting and sheet rolling equipment. By August, the plant had reopened and was running at full capacity.
The “Big Three” builders aren’t the only ones riding the production wave. Specialty tank-car builder Texana Tank Car and Manufacturing is booked into 2008, says Executive Vice President Terry Brooks. The company builds about 100 cars a year, mostly stainless steel and compartmentalized units. “We can’t compete with the big boys — they pretty much have the ethanol cars,” Brooks says. “We grow annually, but we grow at a small pace.”
The company’s tank-car repair business also has been strong, he adds.
Building partnerships, too
As builders cope with increasing demand, they’ll also need to consider other issues. Chief among them are safety and security concerns, and how cars will be constructed in the future.
The Federal Railroad Administration is working with the Transportation Security Administration and the Pipelines and Hazardous Materials Safety Administration to develop “next generation” tank cars that are less likely to be damaged during an accident or terrorist attack.
Three fatal derailments that led to the release of Toxic Inhalation Hazards have been a cause for concern for the industry, as well as for Congress, which has held hearings on ways to improve transport of such hazardous materials.
Additionally, the Association of American Railroads’ (AAR) Tank Car Committee is analyzing potential solutions to make the cars stronger.
“A new AAR standard will mean thicker heads and shells, which will make the tank cars more resistant to attack,” says Robert Fronczak, AAR assistant vice president of environment and hazardous materials. “[The Railway Supply Institute], [American Chemistry Council], the Chlorine Institute, and AAR are cooperating on a project to evaluate armor technology that might be applicable to tank cars. The next generation tank car committee is considering some of this technology for inclusion in their design, but it is not clear whether it will be feasible.”
As many as 7,000 tank cars built before 1989 might need to be replaced if railroads pull them off the lines, Rail Theory Forecast’s Kolstad says.
Entire fleets to be replaced
At the same time, another next generation tank car panel, led by Dow Chemical Corp., Union Tank Car and Union Pacific Railroad, also is addressing safety and security.
A coalition of chemical manufacturers already has committed to replacing their entire North American chlorine tank fleets by 2017 with safer, more secure cars. In addition to Dow Chemical, the group includes Occidental Chemical Corp., US Magnesium L.L.C. and Bayer MaterialScience.
“We simply do not know the number of cars that will be replaced or the financial impact, but we can assure that it will be significant,” says Gerald Wasserman, global supply chain director, chlor-vinyl business for Dow Chemical and a spokesman for the coalition.
Ultimately, cooperation among all stakeholders will be key. “We’re excited about the possibilities of bringing in new technologies — we’re looking at everything,” says Bill Schoonover, the FRA’s staff director of hazardous materials. “We’re taking a global view of the tank car and rail hazardous material safety. I see us moving ahead very quickly and working with the industry. We’re really partnering with the experts.”
Tank-car builders expect to be engaged in that dialogue — if and when they have a chance to look up from their still-humming production lines.
Robert J. Derocher is a Loudonville, N.Y.-based free-lance writer.