Stay updated on news, articles and information for the rail industry
July 2022
Rail News: Mechanical
Suppliers offer an array of technologies to help railroads cut diesel consumption, reduce emissions
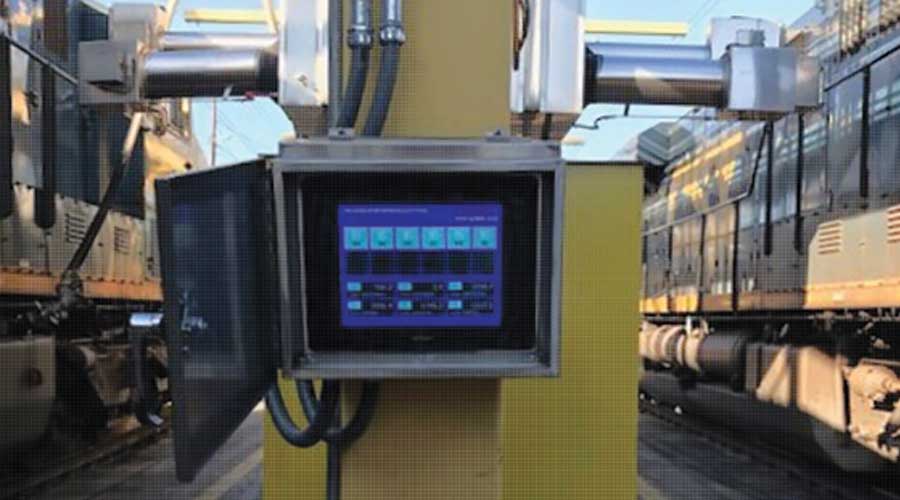
Compiled by Michael Popke
CWI Railroad System Specialists
Over the years, CWI Railroad System Specialists’ RYDM Rail Yard Data Management has morphed from tracking fuel usage into a customizable, modular-based system providing metering, data accuracy and real-time data management functions. It serves a variety of rail yard tasks — including truck loading and unloading, as well as locomotive nozzle fueling — with an emphasis on accurate measurement, data integrity and safety, company officials said in an email.
The reporting capabilities are cutomizable; instant email notifications are available for warnings or advisories for high tank levels, specific fuel/sand/lube/waste quantities, leak detection and system faults. Other fetures include maximum locomotive/truck filling shutoffs and fuel security/ theft prevention.
CWI also has installed fuel tracking systems on locomotive service trucks. Equipped with a 12-volt RYDM system, the trucks use all standard RYDM equipment. The data gathered synced and accessed via a dedicated RYDM website dashboard. Authorized users have access through cell phones, laptops, desktops and/or local displays, and data from all fueling sites is consolidated and updated in real time.
Hotstart Thermal Management
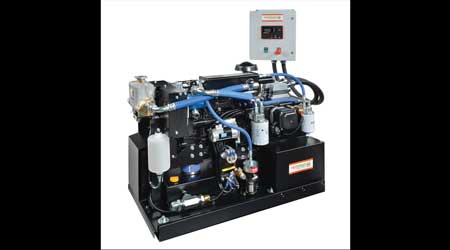
One way railroads can offset fuel cost increases is to invest in idle reduction systems designed to eliminate the need for locomotive idling in cold weather.
Hotstart APUs and shore power electric engine heaters operate when a locomotive is parked, either in the yard or remotely, and help keep the prime mover and oil heated in cold weather, company officials said. Depending on the solution, battery charging, cab heat and Automatic Engine Shutdown/Startup interfacing are available.
The APU operates on the locomotive’s diesel source, using 0.5 gallons per hour compared with four or five gallons per hour by the locomotive, company officials said. Shore power systems connect to power in the yard, eliminating the need to use diesel for idling. Keeping a locomotive heated with a Hotstart system also eliminates wet stacking and emissions, company officials said.
New York Air Brake LLC
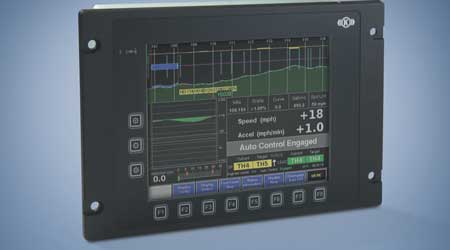
New York Air Brake LLC (NYAB) offers LEADER®, an onboard train-control system that reduces energy consumption and CO2 emissions by 6% to 17%, according to NYAB officials.
The system’s foundation is an onboard computer with a database containing the track profile of a given trip (hills, curves, speed limits and distance) and the makeup of the consist (train length, weight, car types, car position, locomotive power and power distribution). Using GPS to pinpoint the location and exact speed of the train, LEADER software performs hundreds of simulations per second that predict train performance miles ahead. It evaluates multiple train operating strategies and selects the strategy that’s the best match for fuel economy, rail-car life and on-time schedule performance, company officials said.
Introduced as LEADER DriverAssist™, the initial system displayed ideal throttle and dynamic brake settings to the locomotive engineer. Today, LEADER AutoPilot™ provides precise automatic operation of throttle, dynamic brake, independent brake and air brakes for increased fuel economy, extended rail-car life and on-time schedule performance.
LEADER is PTC-compliant and responsive to enroute signal changes, changing weather conditions and locomotive performance. Deployed on more than 5,000 locomotives worldwide, LEADER was the first onboard energy management system for heavy-haul freight trains, the first onboard train-control system to demonstrate the ability to start and stop a freight train under the sole control of a computer and the first autonomous heavy-haul train-control system (driverless train) in revenue service, NYAB officials said.
Power Drives Inc.
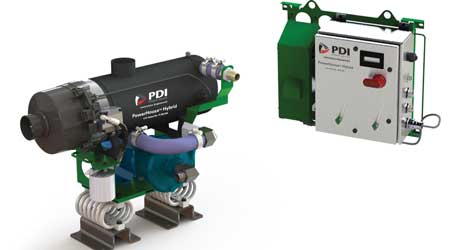
The newest model in the PowerHouse™ lineup, the PowerHouse™ Hybrid from Power Drives Inc. eliminates the engine as an APU — powering itself directly from the locomotive battery bank.
The Hybrid can run off the locomotive batteries for up to seven days without starting the engine; when plugged into an external 120-volt power source, the Hybrid charges the locomotive batteries.
“Customer savings have surpassed the investment in as few as three months,” company officials said, adding that typical usage savings is more than 10,000 gallons of fuel in one season.
Additionally, the PowerHouse system heats the engine oil and circulates heated coolant through the locomotive engine block and cooling system to maintain a fluid temperature above 100 F — even in the coldest of temperatures — via a diesel-fired heating unit, company officials said.
Progress Rail
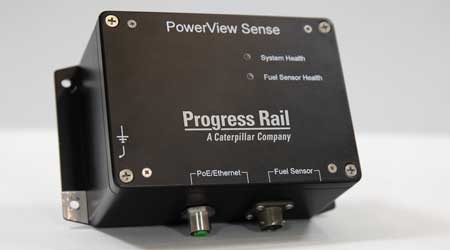
Progress Rail offers Talos™ Energy Management, train automation software designed to automatically (and more efficiently) control the throttle and dynamic brake.
“Customer deployments are experiencing up to a 15% reduction in fuel consumption, lower in-train forces and more consistent train operation,” company officials said.
Talos also enables locomotive engineers to focus more on “the overall situational awareness of the train’s surroundings,” which increases train safety, company officials said.
Additionally, Progress Rail now offers NitroMP Movement Planner and Pacing NitroMP through the company’s acquisition of decision-support software company Nitryx. NitroMP uses machine learning and optimization tools to improve railroad network operations.
Connecting the movement plan to Talos train automation can further improve network efficiency and fluidity: During a “meet and pass” situation, Movement Planner can optimize the train’s speed (and fuel consumption by Talos Automation train), thereby avoiding a delay caused by one train waiting for the other. The potential result: up to a 20% additional decrease in fuel consumption, company officials said.
Meanwhile, the PowerView Sense unit connects to any open Power over Ethernet port on the PowerView network and enables ultrasonic fuel sensor readings while comparing X, Y and Z acceleration data to create accurate tank volume measurements.
Railhead Corp.
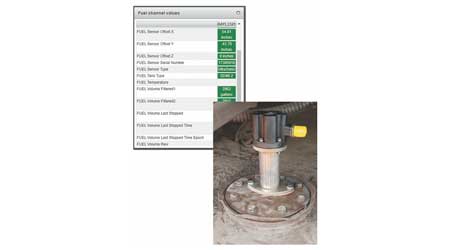
Railhead Corp.’s modular system utilizes an ultrasonic sensor installed through the top of the fuel tank. The sensor is Power over Ethernet-powered, making it easy to install or retrofit, and it does not require mounting a 4-foot capacitive pole like other fuel sensors, company officials said.
Users can detect fuel events, evaluate history, calculate consumption, detect rapid-fuel loss, monitor real-time fuel levels, and detect low fuel and other fuel-related anomalies. Fuel data can be accessed through a full back-office software application along with other train data or viewed with video captures using Railhead’s standard RSM software.
The company’s fuel monitoring system uses accelerometers and custom algorithms to compensate for pitch and roll of the locomotive, resulting in increased accuracy in fuel readings, Railhead officials said.
Wabtec Corp.
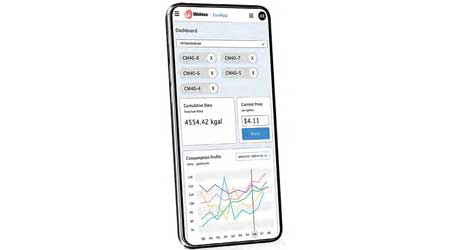
Wabtec Corp.’s new Fuel App is designed to provide operators full visibility into fuel consumption, enabling them to optimize operations in real time through an intuitive interface on any mobile device or web browser. The application connects data from multiple systems and sensors to provide an up-to-date view of fuel consumption, and can connect to energy management systems, event recorders, train sensors, fuel gauges, locomotive control systems and external systems, such as fuel depot records, company officials said.
The application also analyzes fuel usage based on throttle, price, spend by locomotive class, crew, trip and geo zones. Leveraging machine-learning technology, the Wabtec Fuel App can detect potential fuel leaks or unnecessary and excessive idling.
Railroads can achieve a 3% to 5% annual cost savings with the app, company officials said. And the machine-learning capabilities help make the app “smarter” as it collects more data over time, they added.
Wi-Tronix LLC
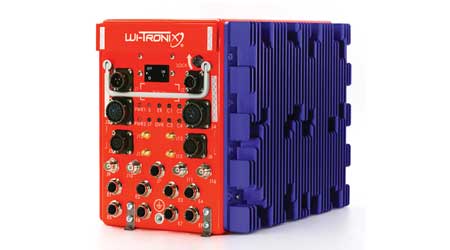
Wi-Tronix LLC provides railroads with multiple fuel management outcomes. The company delivers monitoring for multiple forms of fuel usage and consumption, including diesel, electric and liquified natural gas power.
The options enable users to determine how energy solutions are performing and receive alerts quickly, compare efficiencies across multiple energy solutions in a fleet, measure effectiveness of energy solutions and easily identify root causes of problems, company officials said.
Wi-Tronix’s Violet Edge fuel management solution is designed to provide real-time, accurate, reliable data and diagnostics on such parameters as locomotive idling time and fuel tank levels. Violet Edge also ensures trains are refueled per trip plan and detects any fuel leakages.
Wi-Tronix receives refuel data from third-party vendors at fixed fueling locations, integrates that data with the company’s ultrasonic sensors installed in the locomotive, and then alerts the railroad if the locomotive doesn’t receive the right quantity of fuel at the right time or location. To further improve fuel data integrity, the company uses artificial intelligence to differentiate a true refuel from erratic fuel spikes showing up as false refuels.
To simplify fuel accounting for Class Is, Wi-Tronix provides a one-click solution for tracking fuel in locomotives at change-of-authority locations. The company also provides standardized emissions solutions for compliance reports, summarized by vehicle type, geography and fleet.
ZTR
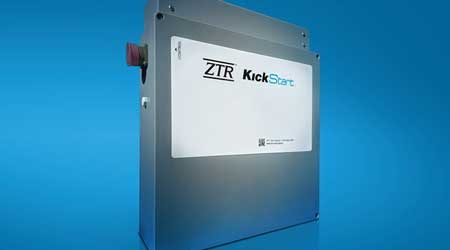
ZTR offers intelligent starting technology alongside proven Automatic Engine Shutdown/Startup (AESS) systems and fuel measurement solutions designed to provide fuel savings, advanced diagnostic information and emissions reductions.
SmartStart® IIe is an AESS system that helps reduce and manage locomotive idling and delivers significant fuel savings. SmartStart IIe also reduces emissions and exhaust smoke and can be applied to “just about any diesel locomotive — from relay logic to microprocessor — regardless of manufacturer, model, age or usage,” company officials said.
A compact system, SmartStart IIe is designed to mount easily and is annually certified by the U.S. Environmental Protection Agency. The AESS can also provide emissions reports and verification of emissions reduction and continues to record actual savings (millions of gallons/liters of fuel) while it’s working, usually paying for itself in less than 12 months, company officials said.
The ZTR KickStart™ starting solution can provide further fuel and emission reductions. Using supercapacitor technology, KickStart offloads the batteries during the engine crank cycle. Over time, the reduced battery usage in the crank leads to reduced AESS engine idle time waiting for the batteries to charge and extends shutdown time due to less battery-initiated restarts, offering further environmental benefits, company officials said.
InteLevel® is designed to provide accurate locomotive fuel level information in harsh railway conditions. The fuel-level measurement technology uses solid-state electronics and a patented technology that operates by sending wave-guided pulses along a tank-mounted, stainless-steel waveguide, and is unaffected by foam, rust, scale or other commonly found tank conditions.
Michael Popke is a Madison, Wisconsin-based freelance writer. Email comments or questions to prograil@tradepress.com.