Stay updated on news, articles and information for the rail industry
September 2016
Rail News: MOW
Track inspection system developers strive to drive more automation to bolster detection, data-collection capabilities
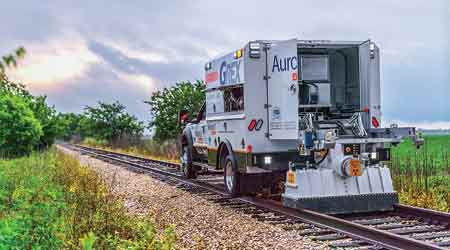
By Michael Popke
Over the past several years, track inspection technologies have evolved significantly, helping railroads boost safety and improve operational efficiency. Yet, railroads covet more ways to accurately detect rail flaws or identify faulty track components to avoid service interruptions. In addition, their heightened concerns about spike and fastener integrity, or earlier-than-expected decay in wood ties, has increased their demand for contract track testing services.
Enter inspection system developers’ ongoing efforts to enhance the equipment they sell or contract out, especially in the areas of track imaging systems and software that can collect, store and display information in real time.
“Railroads are collecting more and more data across their networks,” said Gerry Coyne, general manager of Holland LP’s Railway Measurement Systems and Services Division, which provides various track measurement systems and services. “The more traditional track geometry and rail-profile data is being augmented with video, machine vision and other wayside data that increasingly is being used to monitor the condition of individual components or aspects of track.”
System suppliers and service providers also are trying to develop inspection equipment that can either reduce the number of personnel required for operation or run autonomously.
So how are they faring with railroads’ more-and-better equipment charge? Progressive Railroading corresponded via email with eight of them to find out.
A geometry problem solved
At ENSCO Rail, there are some new-or-improved offerings in its equipment arsenal. Last year, the company introduced a RailScan Lite-Track Geometry Measurement System (RSL-TGMS), which is designed to measure full track geometry from a standard-size hi-rail vehicle. The company reduced the system’s size and weight by employing the latest digital technology, said Matthew Dick, ENSCO Rail’s deputy division manager for product business operations.
RSL-TGMS can be operated by a single laptop using ENSCO Rail’s GeoEdit 8 software, which has been updated to a simpler and more intuitive user interface to boost usability and efficiency, company officials said.
In addition, ENSCO Rail earlier this year began offering a new server software system called the Automated Maintenance Advisor (AMA). The system is designed to automatically review and process track inspection data to provide recommended maintenance tasks such as tamping, undercutting, grinding and rail replacement. AMA can operate on its own without a team of maintenance planners, “thus increasing efficiency,” ENSCO Rail officials said.
The company also continues to market an Autonomous Track Geometry Measurement System (ATGMS) that offers reduced operational costs and increased surveys compared with traditional manned track geometry measurement systems, they said. ENSCO Rail has installed ATGMS — which was released in 2013 — on revenue locomotives, and freight and passenger cars. The system is picking up steam this year and ENSCO Rail has five ATGMS deliveries slated in 2016, company officials said.
Product suite for Protran
There also are new track inspection options available from Harsco Rail’s Protran Technology, as well as one that will be introduced soon. To address the growing need for accurate and low-cost geometry measurements, Protran Technology has developed the Callisto suite of track geometry systems.
The suite offers geometry solutions for several rail applications, including:
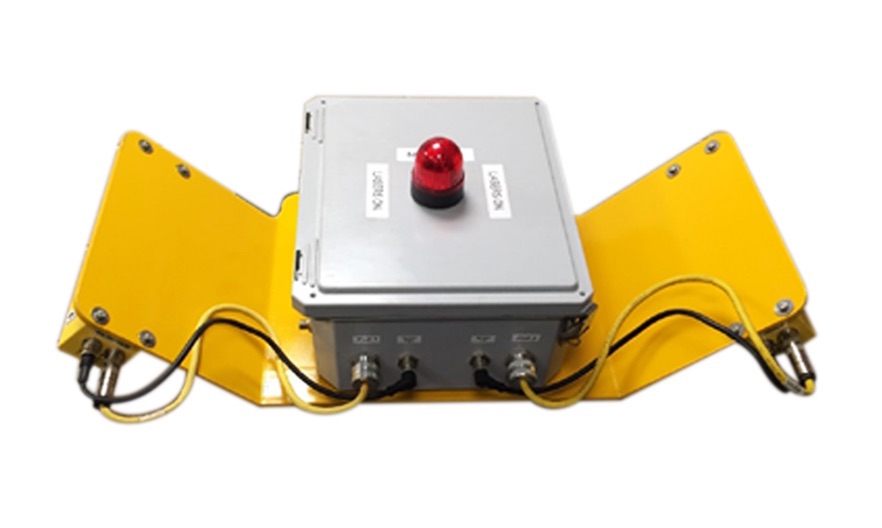
Photo: Harsco/Protran Technology
• Callisto-ProTamp, a system launched last month at the American Railway Engineering and Maintenance-of-Way Association’s annual meeting that can provide high-speed recordings integrated with Harsco’s Mark IV and 6700 series tampers to help boost productivity and improve tamped track quality;
• Callisto-HyRail, a system to be launched in late 2016 that’s designed to offer a precise and more economic solution for track geometry data collection onboard hi-rail vehicles, and will feature Federal Railroad Administration-exception processing and sequential inspection overlays; and
• Callisto-Absolute, a system now available that can serve as a mechanism for railroads requiring a precise track location to integrate survey instruments to a tamper for automated operation.
Callisto’s track geometry measurement systems incorporate an inertial measurement unit, a laser/camera-based gauge reference system and GPS capabilities within a rugged, compact package to accurately locate and measure track geometry, said Joseph Palese, Harsco Rail’s senior director of engineering and technology.
Herzog Services Inc. and Herzog Services of Canada Ltd. (collectively known as Herzog Services) — which provide track inspection services to North American Class Is, regionals, short lines and transit-rail agencies — also are offering new options along with some tried-and-true equipment.
Last year, the company introduced the Series 4000, a versatile rail inspection vehicle based on the Polaris Brutus all-wheel-drive utility task vehicle. Although small in stature, the vehicle offers all the detection capabilities of a full-sized inspection vehicle, including under-shell transverse and vertical split head detection, Herzog Services officials said. The Series 4000 is used in areas that tend to be difficult for larger vehicles to access, such as yards, crossovers, mainline skips and some places on transit-rail systems with tight curvatures, said Herzog Services President Troy Elbert.
The vehicle’s success led to the introduction of another Polaris product: the Hippo. Sporting a portable power pack, non-pneumatic tires and hi-rail system, the four-wheel-drive Hippo is designed for yard maintenance in areas where it’s difficult for a larger service truck to maneuver, Herzog Services officials said. The installed power pack features a hydraulic circuit, compressed air, generator and welder that can be used to perform many railroad maintenance and repair tasks, they said.
Testing vehicles put to the test
Enhanced track inspection vehicles are paramount for Holland, as well. The company entered the track measurement realm nearly two decades ago with its TrackSTAR® Gage Restraint Measurement System (GRMS) testing vehicles, which provide gauge restraint, track geometry and rail-profile measurements from a heavy-duty, hi-rail platform. Holland collects and manages measurement data for Class Is, regionals, short lines, and transit- and commuter-rail systems.
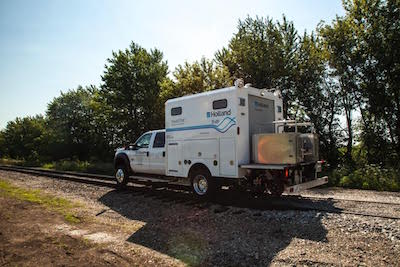
Photo: Holland LP
The GRMS vehicles are in high demand following incidents in which track gauge strength issues appear to have played a role in derailments, Holland officials said.
The company’s patented load-axle technology is engineered to provide full GRMS testing from a hi-rail platform and target at-risk areas, whether based on tonnage, track and component condition, or hazardous materials transportation, they said. The company now offers the mid-weight 850 Series platforms that feature a smaller version of its load-axle technology.
Most recently, Holland has focused its development efforts on the Vista Track Geometry Measurement System, which was introduced in 2012. The system can deliver track geometry measurements that are very low power, with fully integrated and embedded components that can reduce system complexity, maintenance, deployment and calibration efforts, Holland officials said.
Due to its streamlined packaging, fully embedded components, and minimal calibration and maintenance requirements, the Vista system is well suited for various deployments, including unattended operation on a revenue-service vehicle or on a track inspector’s hi-rail unit, they said.
For Plasser American Corp., a track measurement car recently delivered to MTR Corp. in Hong Kong holds promise. The non-self-propelled car features state-of-the-art measuring and video systems.
The vehicle also sports a non-contact inertial navigational track geometry measuring system with no minimum speed requirement; a rail-profile measuring system; overhead wire geometry capabilities to measure wire wear and detect poles; an overhead wire pantograph with voltage and an acceleration measuring system; and an overhead line video system.
All parameters are measured simultaneously, and can be analyzed and displayed in any combination in real time onboard the car. Plasser can provide office software for detailed reviews and further in-depth analyses.
A towed multifunctional measuring car (TMMC) is an ideal platform for subway and transit systems, said Plasser American Sales Manager Ron Olds. It can be towed in consist with revenue trains, other track maintenance machines or dedicated locomotives. If towed as an end car, some additional options are available, including driver’s view and thermal imaging video capabilities, and clearance measurements.
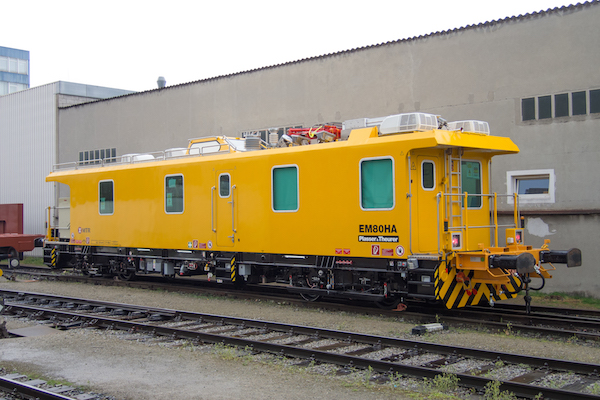
Photo: Plasser American Corp.
A TMMC could additionally feature systems to obtain the following measurements: corrugation, axle box and car body acceleration, flange way, third rail (including temperature), ultrasonic rail flaw and track component video, Plasser officials said.
At Loram Maintenance of Way Inc., the R&D focus has been fixated on offering track inspection vehicles that combine precise rail-profile measurements with severity levels of rolling contact fatigue to help best calculate which fatigued metal to remove. A series of algorithms determines the optimal grindstone placement to reach a desired profile while avoiding wasted metal removal, thus further extending rail life, Loram officials said.
“This technology has been used to create grind plans for more than 75,000 pass miles of rail ground every year in North America alone,” they said.
Rolling contact fatigue in focus
Combining the system with Loram’s Predictive Preventive Maintenance model can help optimize the timing of a grind and further minimize the growth of rolling contact fatigue.
“There is interest in developing technology to measure the magnitude of rolling contact fatigue in order to improve accuracy and consistency,” company officials said.
To that end, Loram is pursuing crack depth measurements through both a non-contact system and a visual evaluation system.
“These technologies can help [railroads] learn more about the way rolling contact fatigue grows through analysis of this data, including the types of exceptions that can be identified to improve the prediction models,” Loram officials said.
Georgetown Rail Equipment Co. (GREX) is trying to help railroads learn more about tie conditions. The company’s Aurora Xi® system has been in production service for the past year and is providing railroads more valuable information about those conditions, GREX officials said.
Aurora Xi combines a traditional 3-D track-profile inspection system with the internal tie condition using X-ray backscatter technology to provide a more complete evaluation of tie integrity.
Each tie is graded based on surface characteristics — including plate cutting and splitting — the same way a tie inspector would perform the grading, GREX officials said. Each tie also is graded based on internal characteristics, such as voids, deep splits and loss of wood density.
Trying to make a top grade
By integrating the two systems, an overall grade can be assigned to each tie to provide railroads the information needed to drive maintenance and capital programs. All data is collected from a hi-rail platform using a single operator and is processed using machine-vision algorithms to provide a wealth of track information.
The data collected by the Aurora Xi system includes asset inventory, measurements, maintenance conditions and defective tie counts.
A data viewer enables users to toggle between the 3-D surface and internal X-ray views to see images of each tie to help understand different degradation and failure modes, GREX officials said.
Geismar-Modern Track Machinery Inc. (MTM) aims to provide railroads a litany of track measurements, too. The company has developed a line of electronic track inspection instruments based on its analog RCAT-A1 track gauge, which has been considered an industry standard for years, Geismar-MTM officials said.
The Garnet digital track gauge measures gauge, cross-level, twist, flangeway clearance and temperature, and offers optional data-logging capabilities. The associated software enables users to overlay the same area of track to compare previous readings, monitor track status and verify that trackwork has been completed.
“So now, you could go out and take all of the measurements and come back to the office and save the data into a PC or laptop for recording and analyzation,” said Geismar-MTM General Sales Manager Alan Reynolds.
The company also offers Amber, a lightweight, electronic and hand-pushed inspection trolley designed to measure track gauge and cross level, and calculate twist. The trolley simultaneously records all information via a Bluetooth connection to a data-logging device.
A segment of track that usually took several hours to inspect or required the use of a geometry car now can be analyzed and measured in a short time, said Reynolds.
In addition, Geismar-MTM now offers a line and level measurement system that was introduced in late 2015 to replace the string line used to check curves. The MINI OPAL, which operates with lasers, can effectively read a curve’s profile, as well as provide vertical readings in bridge approaches and runoffs, said Reynolds.
Geismar-MTM also is developing an instrument designed to more effectively read and record rail-seat abrasion.
Michael Popke is a Madison, Wis.-based freelance writer. Email comments or questions to prograil@tradepress.com.