Stay updated on news, articles and information for the rail industry
October 2021
Rail News: MOW
2021 crosstie update: Concrete, steel and composite ties providers talk products, trends
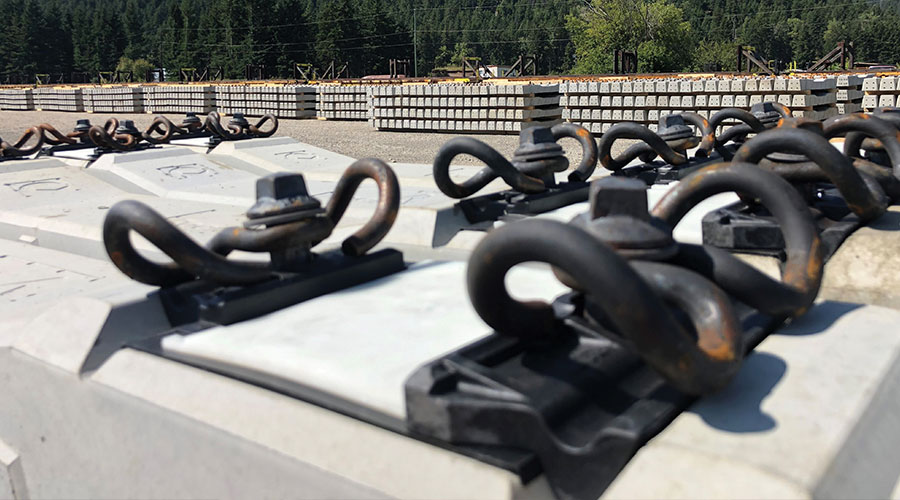
Vossloh Tie Technologies
For about 18 months, Vossloh Tie Technologies (VTT)/Rocla Concrete Tie Inc. has been producing and supplying ties from a new Canadian plant, offering heavy-haul, transit and industrial concrete ties to the Canadian market. The facility can produce more than 250,000 concrete ties per year and offers “significant logistics advantages,” company officials said in an email.
“Whether it’s major flooding in the south or wildfires sweeping across California and British Columbia, our customers have come to rely on installing concrete ties through their most demanding and environmentally challenging area,” they said. “We have seen a significant reduction in track outage time when concrete ties have been installed in areas that are prone to flooding and wildfires.”
Concrete ties also have been “the least volatile of all crosstie types” when it comes to price changes, they added.
The company continues to develop products designed to protect and prolong the lifecycle of concrete tie track infrastructure, including concrete ties fixed with Under Tie Pads (UTPs), a process common throughout the world. The demand for UTPs is increasing, company officials said.
CXT Inc./L.B. Foster Co.
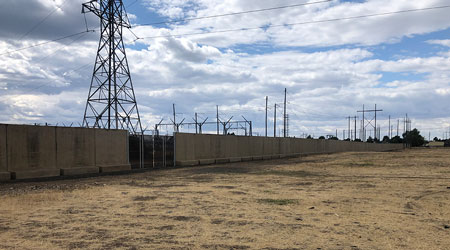
Officials at CXT Inc./L.B. Foster Co. are encouraged by several current and ongoing concrete-tie developments, particularly in the transit market segment, but also in the freight-rail and energy industries.
“Current market conditions remain favorable for concrete ties vs. wood ties, although port disruptions and resulting shipping delays for some raw materials have squeezed our production schedules,” Engineering Manager Vince Petersen said in an email. “We’re also continuing to see wood-tie jobs convert to concrete ties because of ease of installation, labor savings and improved overall track quality.”
Current projects include phases of the Sound Transit East Link in the state of Washington, connecting Bellevue, Redmond and Federal Way to Seattle. Additionally, customers are contacting CXT regarding crane rail projects.
“We’ve seen strong demand from mining operations for stacker/reclaimer ties and from forestry product suppliers for gantry crane ties,” Petersen said. “The combined product offerings from CXT® ties and L.B. Foster rail streamlines procurement for our customers for these types of projects.”
CXT/L.B. Foster also has expanded its concrete offerings to include alternative products; a recent project required precast security walls for a local utility provider. The company is reaching out to new and existing customers to market the standalone security enclosure wall system, which includes an anti-graffiti coating.
voestalpine Railway Systems Nortrak
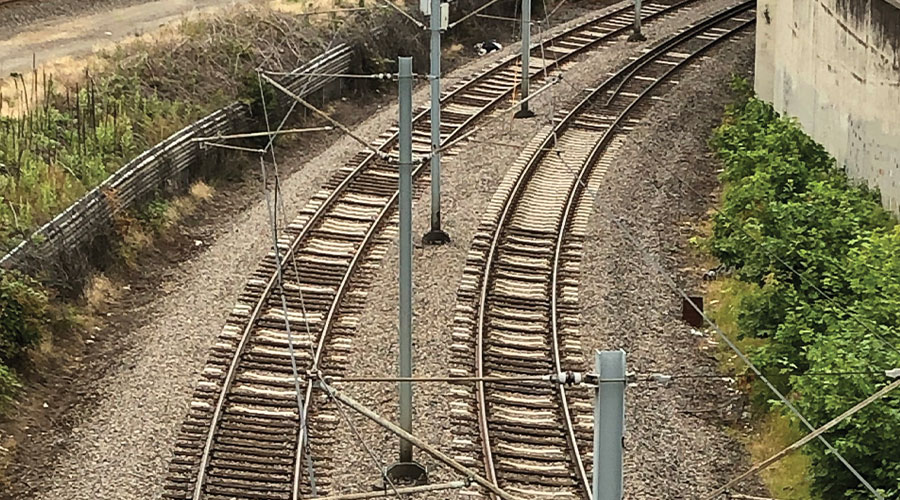
To complement the company’s special trackwork offerings, voestalpine Railway Systems Nortrak created an integrated Fixation Systems Team focused on developing, testing and manufacturing a portfolio of crosstie and fastening solutions for freight and passenger customers. Nortrak customers include Union Pacific Railroad, Bay Area Rapid Transit, LA Metro, Sound Transit, Amtrak, MTA Long Island Rail Road and Florida’s Brightline.
“We focus on producing only the highest-quality concrete ties using our custom-built longline production system and are committed to designing products that solve our customers’ unique challenges,” said Dave Peterson, Fixation Systems plant manager, in an email.
Such products include a shallow-depth turnout tie currently being deployed for locations where fixed infrastructure limits ballast depth; and the Keyway Concrete Tie, designed to be randomly interspersed with wood ties during typical maintenance intervals. The Keyway tie has the same footprint and track stiffness profile of wood ties, but with “superior gauge holding ability and longer service life, all in a package that is environmentally friendly and fully recyclable,” Peterson said.
Keyway ties are installed in Class I, commuter rail and transit operating environments using standard maintenance-of-way equipment. Both 5 1/2- and 6-inch base rail sections are now available, as well as designs for fixed guardrail, adjustable guard rail and adjustable stiffness profiles for transitions into bridges, tunnels or grade crossings.
TieTek Global
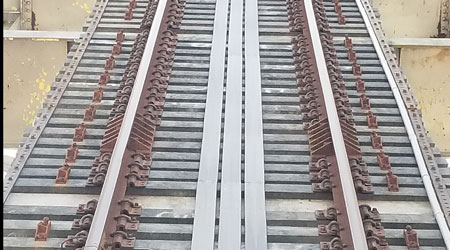
Earlier this year, LT Resources Inc. acquired American TieTek’s assets, including TieTek® technology. The company’s been rechristened TieTek Global (TTG).
TTG’s offerings include engineered polymer composite TieTek crossties, switch ties, bridge ties and custom products. TieTek’s patented formulation features premium recycled materials to produce composite products that demonstrate strong performance and extended service life in high-decay areas and severe environments such as tunnels, bridges, bridge approaches and grade crossings, TTG officials said in an email. TieTek ties also are “resistant to insects, fungi, moisture, harsh environmental conditions and rail-seat abrasion,” they said.
The TieTek tie is the only AREMA-standard engineered polymer composite tie to perform without failure between 2000 and 2015 at Transportation Technology Center Inc.’s FAST high-tonnage loop track, accumulating over 2 billion gross tons, company officials said. The ties were installed six years ago and continue to perform well, they said.
The ties can be interspersed with treated wood ties or installed in new construction to reduce and eventually eliminate on-going tie replacement costs. Installing TieTek composite crossties, switch ties and bridge ties — which are manufactured using 80% recycled materials and are recyclable if mechanically damaged — can help companies address sustainability goals, company officials said.
NARSTCO
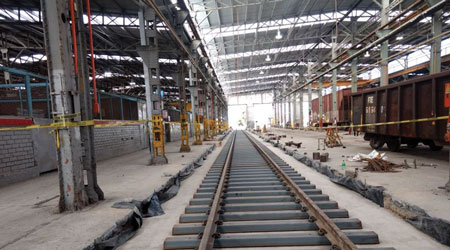
Steel ties and turnout sets are “gaining popularity with end users” seeking upfront cost savings, life cycle savings and “green” benefits, NARSTCO Director of Sales and Marketing Matt Violin said in an email. Steel ties and turnout sets require less ballast and are easier to install, require less maintenance and fewer tie changeouts, and are made from recycled material and are recyclable after use, he said.
NARSTCO’s steel ties are suited for a range of rail applications, including ports, industrial facilities and siding/passing tracks.
Company officials also are noting more demand for steel ties in concrete-embedded track applications at warehouses, heavy tonnage industrial crossings, loading/unloading pads and rail-car shops, Violin said.
The company’s ties feature open (not spaded) ends and inspection holes, so concrete can be pumped and vibrated throughout the underside of the tie while holding the rail at the specified gauge.
Evertrak LLC
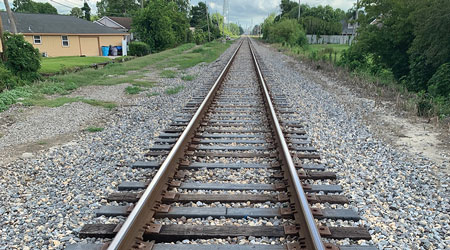
Evertrak LLC manufactures the Evertrak 7000 glass fiber-reinforced composite (GFRC) crosstie. With 40,000 Evertrak 7000 ties installed as of mid-2021 — and more than 99.9% reliability in track, according to the company — Evertrak is relocating and expanding its operations in St. Louis. The state-of-the-art facility will enable Evertrak to quadruple production by the end of 2021 while providing rail service for outbound logistics.
The facility will manufacture Evertrak 7000 GFRC ties in 8-foot, 6-inch and 10-foot lengths for mainline installation, as well as a limited number of ties for low-speed track.
“The new production facility marks the completion of the pilot phase of our Evertrak 7000 mainline crosstie,” President Matt Moore said in an email.
The company plans to make investments to scale production, reduce outbound shipping costs with rail service and “underwrite innovations in capital leasing for lower capital costs on installation,” Moore said.
Michael Popke is a Madison, Wisconsin-based freelance writer. Email comments or questions to prograil@tradepress.com.