Stay updated on news, articles and information for the rail industry
June 2024
Rail News: MOW
Suppliers tailor hi-rail maintenance equipment to customers' needs
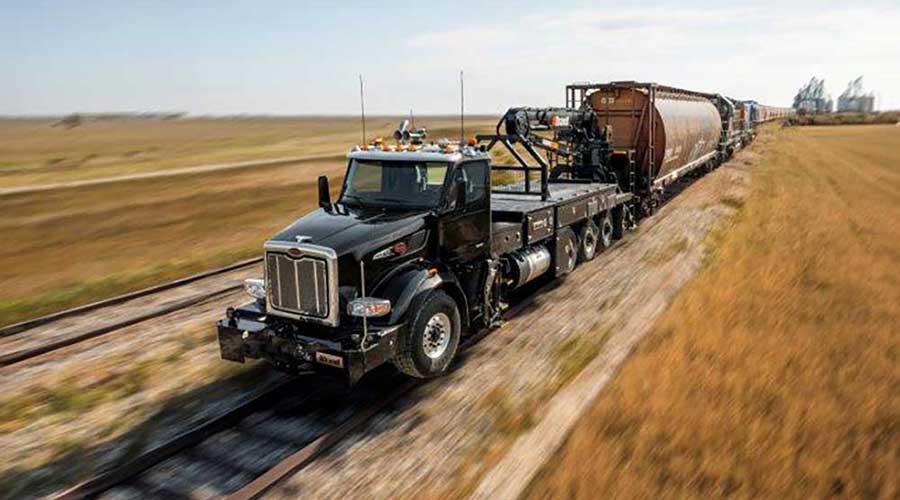
Compiled by Julie Sneider
Brandt
The Brandt R4 Power Unit rail-car hauler has been a mainstay in the industry for many years. Brandt recently unveiled its new R5 unit, which enables operators to perform maintenance-of-way, revenue service, emergency response and other work efficiently and safely, company officials said in an email.
The R5 is purpose-built to keep customers productive and efficient. It’s capable of producing up to 605 horsepower, 2,050 foot-pounds and 50,000 pounds of tractive effort. The R5’s off-road transmission and tridem drive axles deliver highway speeds up to 65 mph, on-rail speeds up to 30 mph and reverse speed up to 25 mph.
The R5’s multiple features ensure a secure working environment. Those features include a new Peterbilt chassis that delivers better visibility day and night, with fewer blind spots as well as backlit controls and infrared cameras. Hydraulic systems have integral counterbalance in cylinders, and the crane swing motor has a static brake and hydraulic lock, which protects from unwanted motion in case the hose ruptures.
DMF
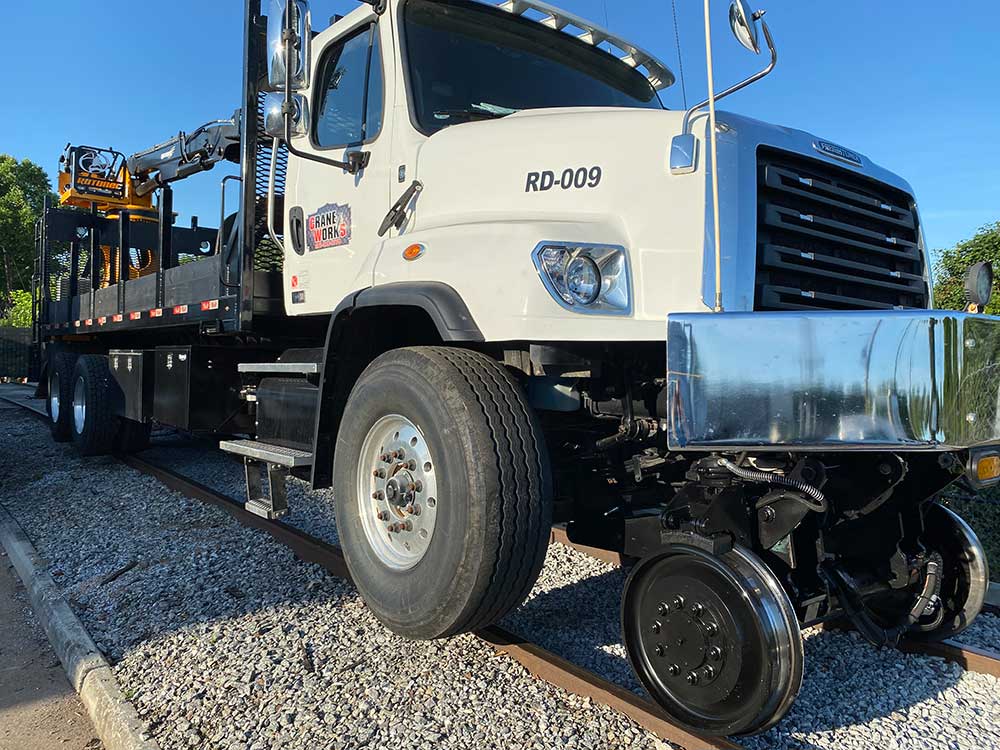
Whether picking up ties from the captain’s chair of a material handler or maintaining the catenary on a light-rail system from the raised platform on the back of a truck, it is vital to have a dependable rail gear system that provides safe and smooth operation, DMF officials said.
The DMF RW-2300HS is a front-mounted hydrostatic creep drive system designed to operate independently of the vehicle’s transmission. With a 33,000-pound gross axle weight rating, the front hydrostatic system can be mounted forward of the front tandems and, in special applications, behind the cab. Full wireless control operates the Neotec motorized front axle, without having to integrate into the vehicle. The system will operate up to 7 mph in creep mode and disengage up to 25 mph in freewheel mode using the vehicle propulsion.
The system is rated for 88,000 pounds at a 2% incline and up to 200,000 pounds on level track. Additionally, the system allows the user to operate the vehicle equipment without having to disengage the PTO to advance the truck down the track, which saves time and money, DMF officials said. Since the RW-2300HS is independent of the transmission, the vehicle can be moved off track if issues arise — unlike some split-shaft systems.
The full system includes the Neotec axle, DMF integration package and DMF RW-1630 or RW-1650 rear axle assembly with auto mechanical locks.
Herzog
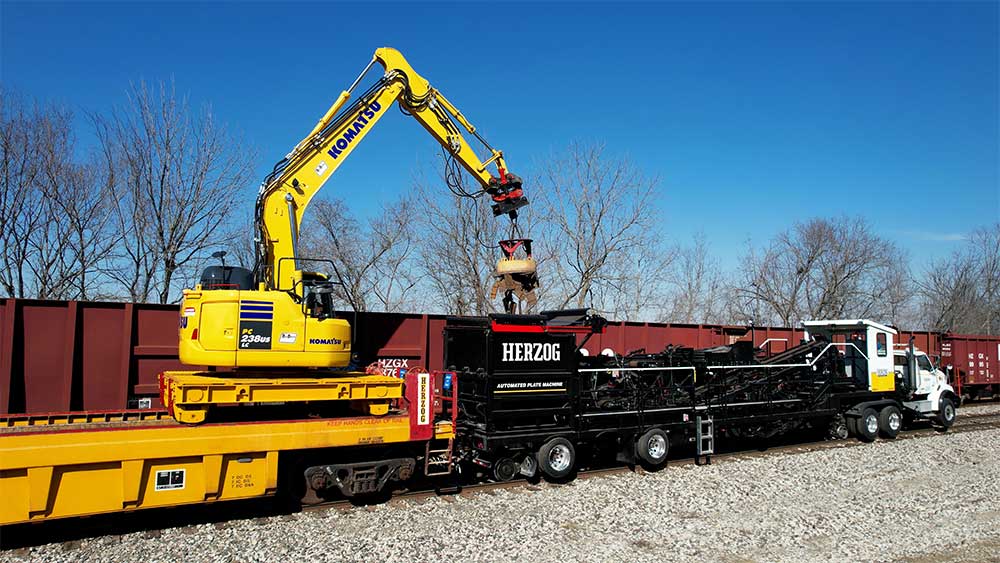
Herzog’s latest innovation is the Automated Plate Machine (APM). Engineered to streamline the tie plate distribution process, the APM reduces safety risks associated with manual handling of other track material, Herzog officials said.
It offers customers the ability to automate the sorting and distribution of both 14¾- and 16-inch tie plates along the field or gauge side of the rail, providing versatility to meet project specific requirements. With no ground personnel required on the right of way, the APM’s patented sorting system helps railroads meet production benchmarks while eliminating laborious tie plate placement activities, company officials said.
“The APM stands as a primary example of Herzog ingenuity, providing our partners with the ability to eliminate the manual process associated with tie plate distribution, optimizing track time without compromising safety, efficiency or quality,” said Herzog Director of Marketing Taylor MacDonald.
Operating at a consistent, calibrated speed, the APM can distribute 1,600 plates per hour. The APM’s road-to-rail versatility ensures rapid deployment to the next job site, optimizing production schedules, Herzog officials said. Its compatibility with a range of on-track equipment — including Herzog’s Multi-Purpose Machine — ensures ease when transferring tie plates into the APM’s material hopper, they said.
Loram
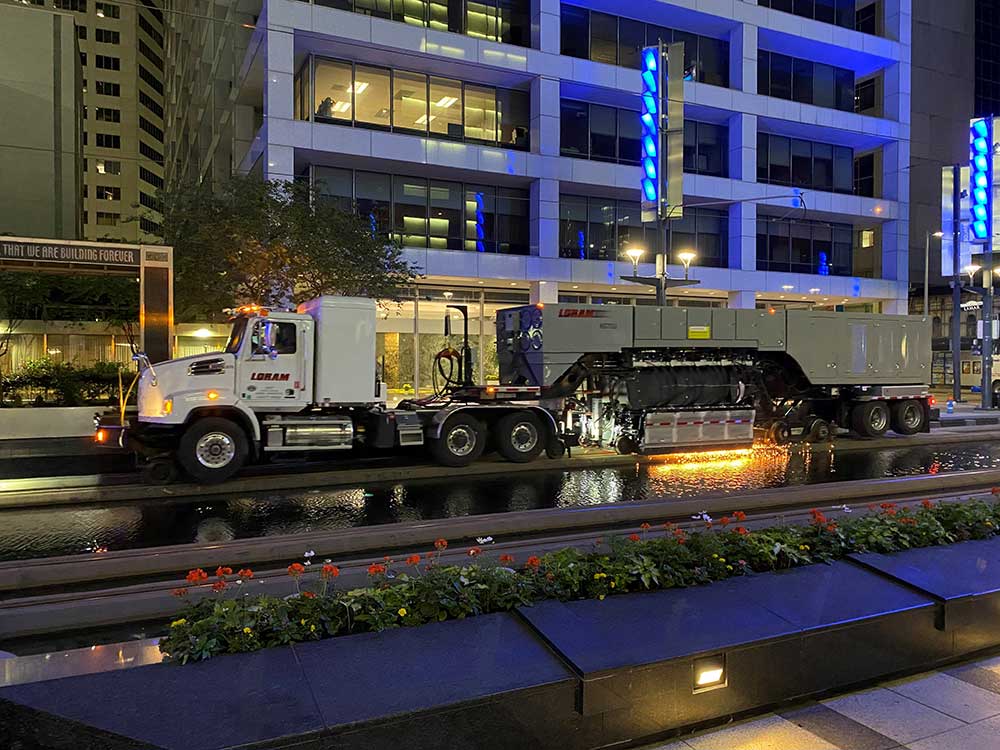
Data collected from track geometry measurement vehicles (TGMVs) offer an objective assessment of track roughness. By comparing track geometry data over time, one can quantify track performance and deterioration rates, Loram officials said.
Key factors contributing to track geometry maintenance include ballast and drainage conditions. Analyzing the vertical profile geometry channel over successive inspections enables evaluation of track ballast and drainage conditions, Loram officials said.
The company has developed “heat plot” that represents geometry roughness using a color scale, with cooler colors indicating smoother geometry and hotter colors indicating rougher geometry. This visualization aids in studying time, distance and roughness in a 2D view.
Loram provides ground-penetrating radar (GPR) and lidar measuring services, along with data analysis for condition assessment. The company’s proprietary analysis tool known as “Rail Doctor” integrates GPR/lidar data with TGMV data, offering insights into the root causes of track performance issues, according to Loram. GPR data continuously measures track substructure conditions, including ballast fouling, subsurface moisture and layer thickness and configuration.
Integrating information from track geometry, GPR, lidar and right-of-way scanning provides a comprehensive view of line health. The Rail Doctor output guides railways in understanding maintenance needs, planning activities and budgeting. Loram’s analysis recommends areas for tamper application, ballast maintenance, drainage improvements and other necessary actions for a healthier track.
In the new generation of substructure maintenance management approach, Loram will offer a suite of advanced technologies for rail infrastructure management, including remote controlled autonomous data collection, remote QC and QA, enhanced positioning, tools tailored for large-scale data collection projects, and AI-based GPR data analytics integrated into Rail Doctor, company officials said.
In terms of Loram’s rail grinding offerings, the Loram RGT Quick-Deploy Rail Grinder is a hi-rail equipped, DOT-certified fifth wheel rail grinder capable of traveling on virtually any North American roadway without the need for special permits, company officials said. It features a fully flexible rail grinding buggy with eight-stones, each powered by a 30-horsepower grinding motor, delivering the most finishing power and capabilities of any truck-mounted solution.
Additionally, Loram-developed 6- and 10-inch diameter grinding stones are optimized for performance and longevity, achieving rail finishes from heavy metal removal to super smooth mirror finishes —or any combination of both — in fewer passes, company officials said. Designed to optimize short service windows, the RGT can deploy or be recovered in as few as five minutes at a rail access point near a service destination.
The RGT can be used to grind switches, grade crossings, transit tracks, open rail or areas of general service or exception remediation. The machine’s crew consists of two people, but there is cabin seating for three people.
Omaha Track Equipment
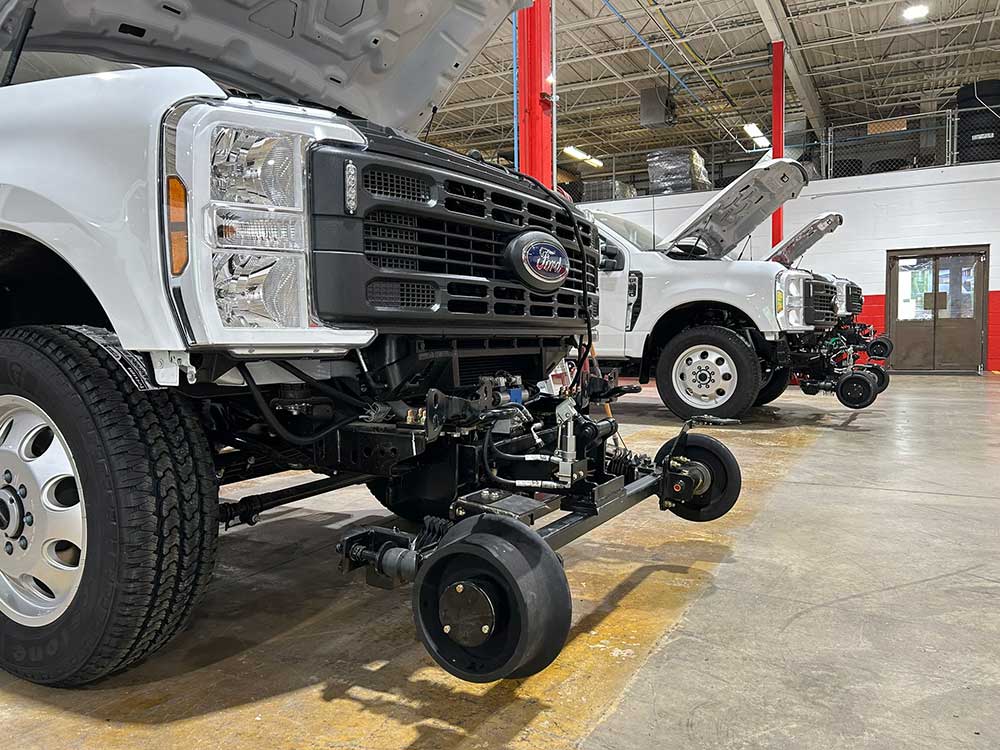
Omaha Track Equipment specializes in manufacturing and repairing hi-rail maintenance equipment. The company’s expertise covers a range of hi-rail equipment, including UTVs, pickups, grapple loaders and heavy machinery essential for maintaining railway infrastructure.
Innovation is key to Omaha Track’s operations, company officials said. Omaha Track continuously develops new ideas and specialized equipment to meet the unique requirements of hi-rail maintenance, they added.
Additionally, the company offers customization services, upfitting new chassis to customer specifications for various hi-rail applications. Omaha Track manufactures several types of hi-rail carts, expanding its product offerings to meet diverse sector demands.
The current market for hi-rail maintenance equipment is driven by the industry’s need for updated and reliable machinery, particularly amid challenges posed by the COVID-19 pandemic, Omaha Track officials said. As existing hi-rail equipment ages, the demand for extensive repairs and modernization grows, emphasizing the importance of repair and customization, they said.
Additionally, the nationwide focus on improving railway infrastructure has amplified the demand for hi-rail equipment, as efficient maintenance is crucial for ensuring the safety and reliability of railway operations.
RailWorks Corp.
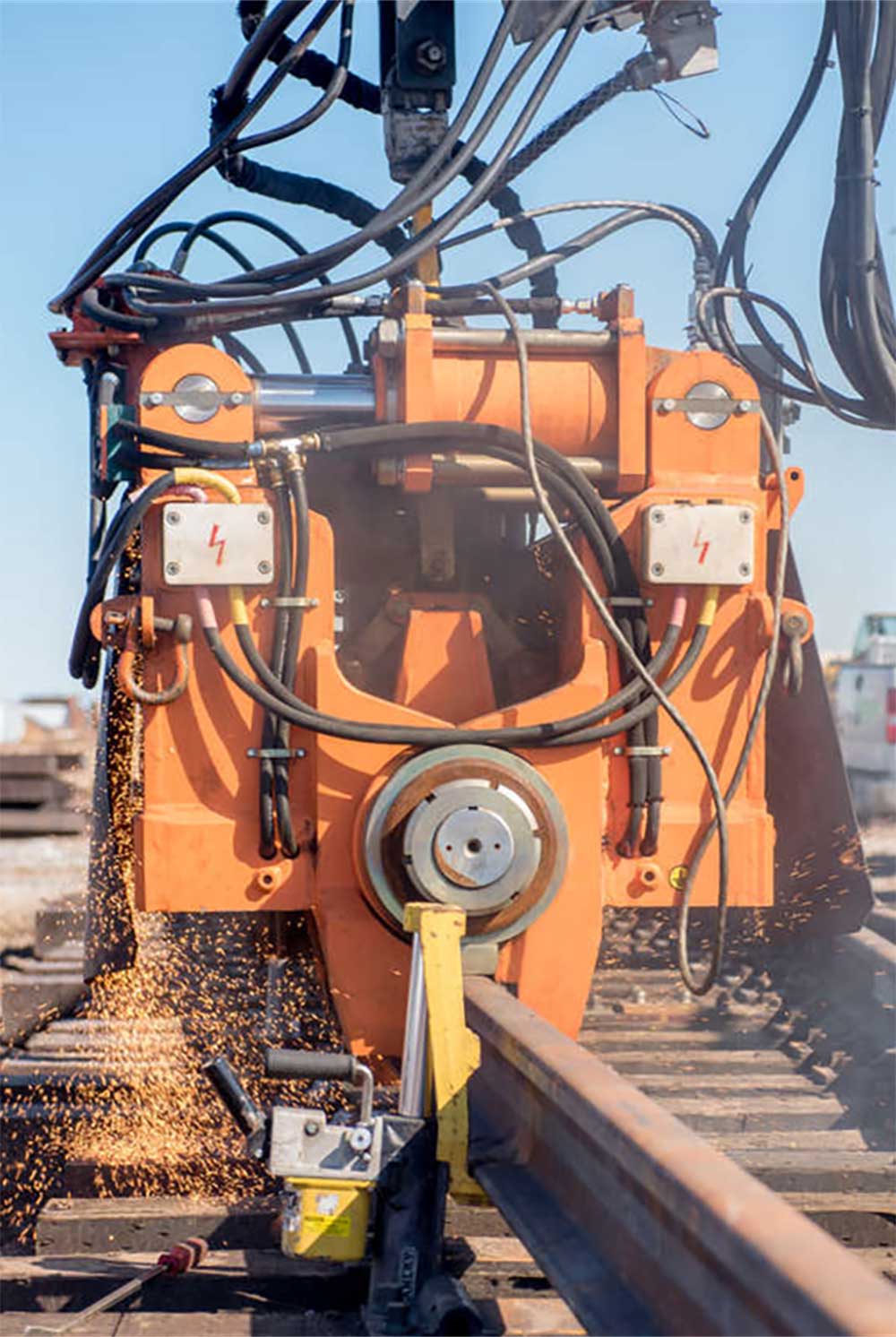
RailWorks has an expanding fleet of narrow head flash-butt trucks equipped with a 70-ton weld head to add to the existing fleet of standard mobile welders. The head requires only 8 inches of clearance to perform a weld, RailWorks officials said. Its unique design enables the company to safely make close clearance welds around the frog and switch points, which are usually accomplished with thermite welds.
The trucks are equipped with a 25-foot HIAB crane that maximizes the reach and enables crews to weld both adjacent to and on track with less moves. The units operate with a standard Chemetron control system and remote monitoring, which enables the observation of real-time weld data.
When utilizing the right conditions, production rates are extremely high, which is lowering the capital expenditures for special trackwork, company officials said.
Email comments or questions to julie.sneider@tradepress.com.