Stay updated on news, articles and information for the rail industry
January 2025
Rail News: MOW
Product update: Trackwork 2025
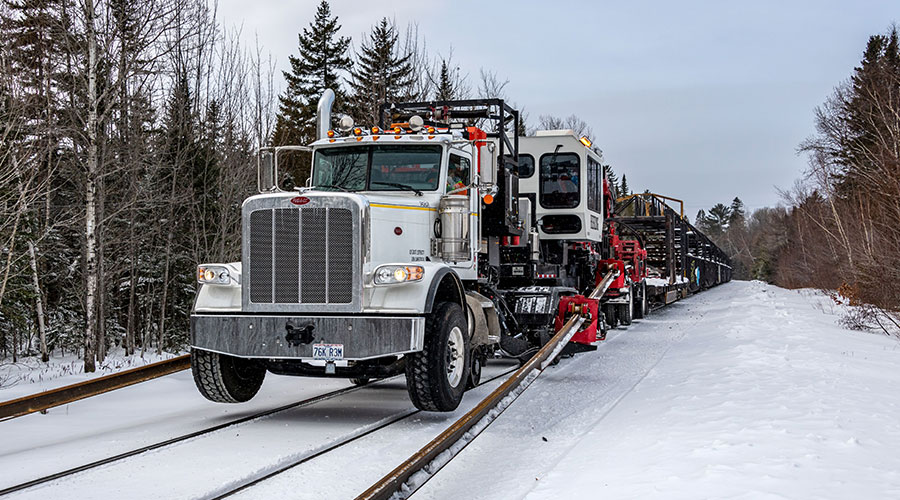
Compiled by Bridget Dean
Herzog
Herzog's Rail-Unloading Machine (RUM) is the rail industry's only road-to-rail continuous-welded rail (CWR) distribution system, company officials said in an email. The RUM aims to redefine rail logistics by combining flexibility, precision and safety in one versatile machine.
The RUM's design enables the machine to travel to multiple job sites under its own power — innovation that provides a crucial solution for projects requiring flexible rail distribution, Herzog officials said.
The RUM features hands-free, precision rail placement, and uses advanced automation to unload and position rails with high accuracy. That capability eliminates the need for manual handling, ensuring that rail is aligned and placed correctly in less time, Herzog officials said. The RUM can unload a 50-pocket rail train in about four hours.
Its compatibility with all Herzog rail trains, as well as most Class I rail trains, further enhances thew machine's usability, making it adaptable for a wide range of rail distribution operations, Herzog officials said.
Safety and efficiency are at the heart of the RUM's design. By reducing the need for manual labor and physical rail contact, the system minimizes workplace risks and enhances operational efficiency, Herzog officials said. Fewer crew members are required and the streamlined unloading process ensures faster project completion while maintaining the highest safety standards, they said.
L.B. Foster Co.
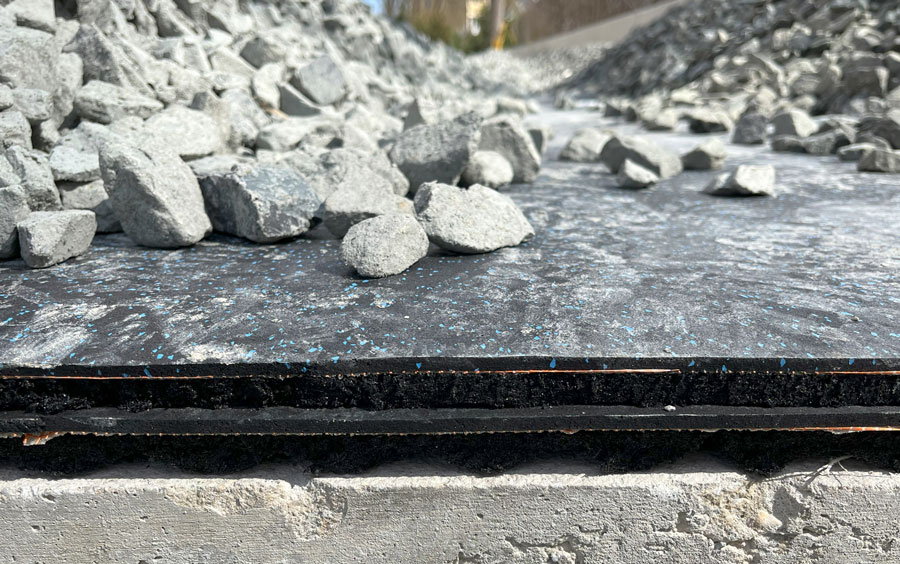
In 2022, L.B. Foster Co. partnered with Pliteq as their North American distributor of GenieMat® RAIL products. The products include the GenieMat® RAIL BST Ballast Mat, GenieMat® RAIL RTP Under Tie Pads and GenieMat® RAIL FST Floating Slab Track Mats.
Since that time, L.B. Foster has successfully supplied Pliteq solutions across the region with notable projects at the Maryland Transit Administration, Metrolinx, Northern Indiana Commuter Transportation District, Tren Maya, Amtrak, Metro-North Railroad, CSX and Vermont Agency of Transportation, company officials said.
The GenieMat RAIL solutions are designed to provide vibration mitigation, significantly reducing ground-borne vibrations and enhancing comfort for nearby communities, they said. By optimizing track stiffness and minimizing ballast degradation, the products can extend the life of rail components and reduce maintenance costs.
In addition, Pliteq's manufacturing practices prioritize sustainability, ensuring the solutions are environmentally responsible from production to application, L.B. Foster officials said.
L.B. Foster remains focused on the development of next-generation track fastener products and systems based on customer demand through internal research and development and external partnerships, they said.
Loram
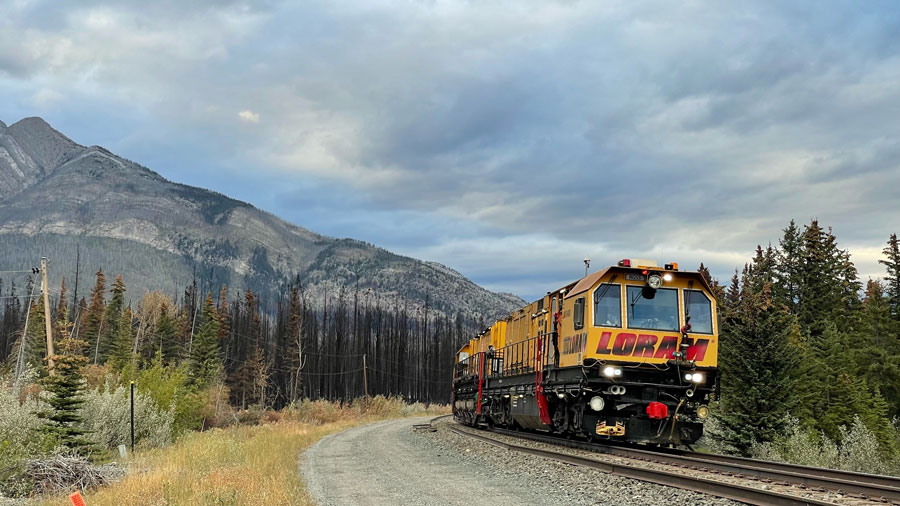
Virtual Rail (VR) software and digital twin approach is part of Loram's strategy to work more closely with its railroad partners to ensure maintenance decisions are part of the overall asset management regime.?The ideal goal is an intelligent program of maintenance perfectly tuned and planned to predict rail degradation and continuously improve the lifecycle of rails, Loram officials said.
VR helps quantify why to grind (life extensions and cost benefits), where to grind (frequency and schedule) and how to grind (rail profile and metal removal needed), they said. Ultimately, digital twins provide location-specific grinding strategies to maximize track life. The users compare how each alternative grinding strategy will impact their track life extension, return on investment and capital plans before they implement the changes in the field, Loram officials said.
The company offers both rail grinding and milling solutions for railroads. Loram's rail grinders incorporate high power, flexible grinding modules and patented control systems to deliver industry-leading speed and proven productivity, company officials said. Loram's rail grinding product portfolio offers machine configurations from four to 120 stones, providing an ideal rail grinding solution, they said.
Through a partnership with Linsinger, Loram's newest solution - the LM1 rail miller - can be used for reprofiling rail when a heavy correction tool is needed. It can restore the lateral and longitudinal profile of the rail while removing all surface defects, and can remove up to 1 millimeter in a single working pass, Loram officials said. That helps extend the surface life of the rail, significantly reducing costs and a carbon footprint, and improving safety, they added.
For spot treatment during tight working windows, Loram's rail milling solution is designed to serve as a cost-effective and environmentally friendly way to extend the life of rail, grade crossings and switches. Because milling is a rotary cutting process, only milling chips are produced and very few sparks and dust are generated by the polishing process, which makes this an ideal option for areas that are highly sensitive to dust and fire, Loram officials said.
Plasser American
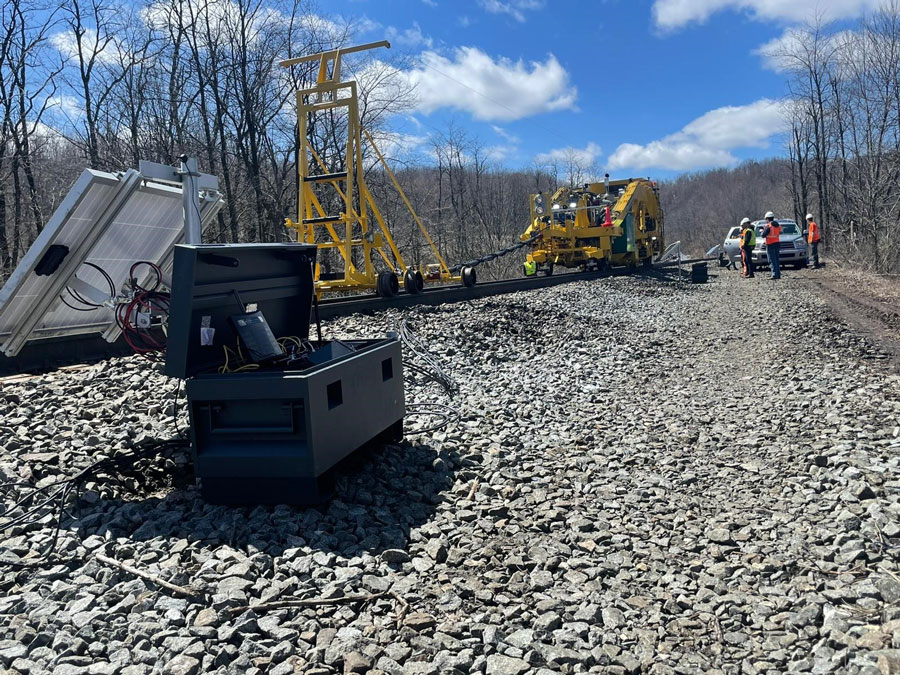
The quality of tamping actions depends on several parameters, such as squeezing time, lifting height and the number of insertions. Those factors significantly influence ballast stability, impacting the durability and safety of tracks, Plasser American officials said. Yet, traditional tamping practices often rely on operator experience, leaving room for variability in results, they said.
A study conducted by Penn State University and Plasser sheds light on the variables. Using “Smart Tamper” technology and “SmartRocks,” the study analyzed tamping action under various conditions on a Class I mainline. The SmartRocks within the ballast bed were equipped with sensors that recorded ballast particle motion and contact stresses to generate real-time data.
The test results demonstrated that tamping parameters such as squeezing time and the number of insertions significantly affect ballast stability, Plasser officials said. For example, a one second squeezing time produced larger acceleration and bulk residual stress in the ballast compared to a 0.6-second squeezing time.
In addition, increasing the number of insertions from one to two eliminated the effect of squeeze time, Plasser officials said. The squeezing process ensures that ballast stones settle properly below a tie, forming a compact and stable foundation. An insufficient squeezing process leads to instability, a failure to maintain the track geometry in the desired position and a higher demand for tamping, Plasser officials said.
To address the challenge of operator variability, Plasser offers TampingControl, which aids operators with real-time feedback and recommendations based on site-specific conditions during the tamping process, company officials said. Meanwhile, Plasser’s TampingAssistant is designed to automate the selection of appropriate settings to help minimize errors and enhance efficiency.
The two tools can improve track stability, extend maintenance cycles and reduce costs, setting new standards for reliability and precision in track maintenance, Plasser officials said.
RailWorks Corp.
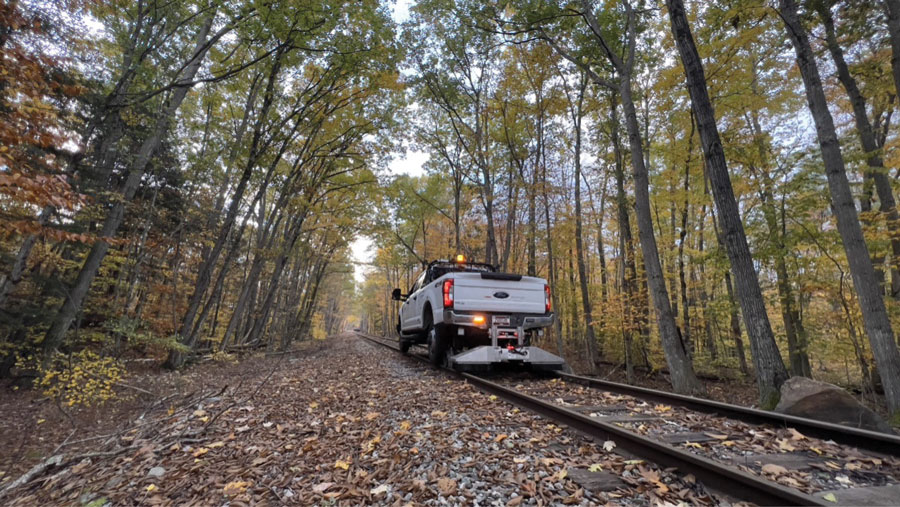
RailWorks Maintenance of Way's latest addition to its track geometry fleet includes an all-in-one Portable Laser Profiler System designed for measuring track geometry and rail profile on any hitched/mounted hi-rail vehicle.
The system's assembly includes a wireless connection and requires no permanent changes or installation on a hi-rail vehicle. RailWorks' footprint and large equipment fleet across the United States and Canada enable the company to quickly respond to customers' needs, RailWorks officials said.
The company provides a Portable Laser Profiler System that can be quickly deployed on any vehicle platform to provide real-time track geometry results. The system provides users the flexibility to inspect track in limited track windows and in short notice while providing pinpoint GPS and accurate data on track conditions, RailWorks officials said.
Customized inspection service and the ability to provide immediate feedback on track conditions - using current track geometry hi-rail fleet or operating a Portable Laser Profile System - enables RailWorks to respond to all market demands, they said.
RailWorks focuses on providing best-in-class service and reporting software to demonstrate the value of utilizing technology that leads to actionable decisions on railroad and track construction operations, company officials said. RailWorks aims to provide leading technology and software to support customers' needs and to present the best results in a data-driven industry.
voestalpine Railway Systems Nortrak
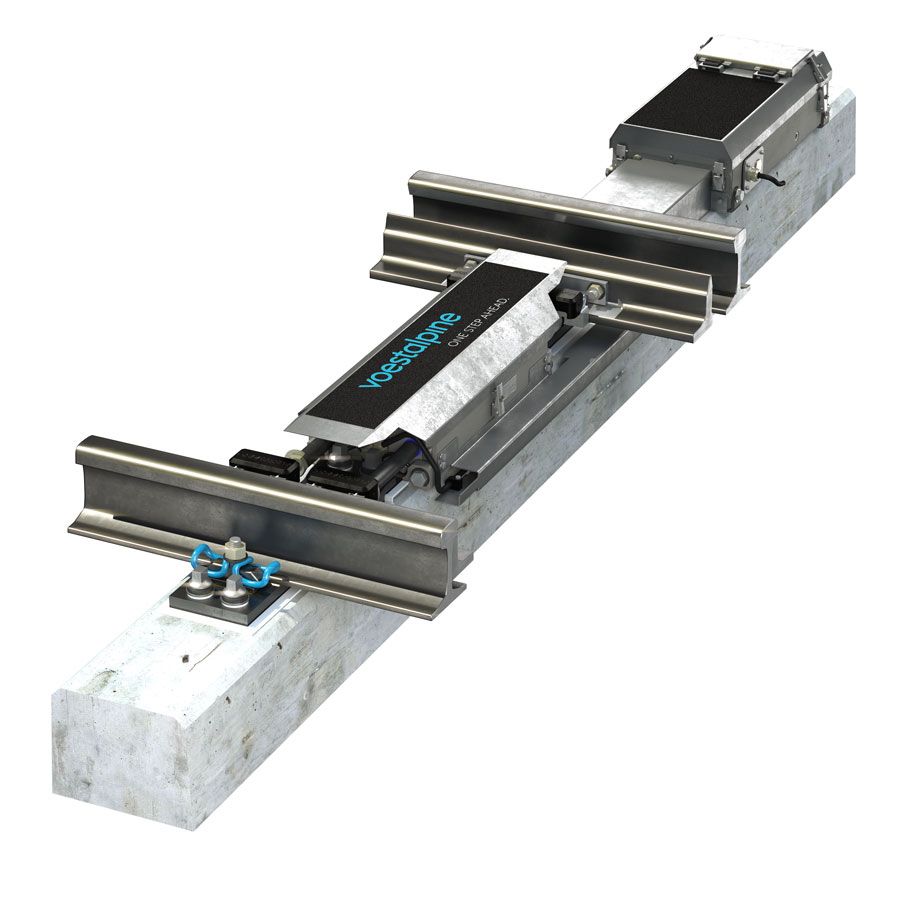
Offering solutions that enhance reliability, safety and efficiency while minimizing lifecycle costs is paramount to voestalpine Railway Systems Nortrak.
The company recently introduced the Universal Hollow Steel Tie (HST) and enhanced UNISTAR-HR switch machine with the zentrak Object Controller Point.
The Universal HST's flexibility in turnout systems streamlines inventory management and simplifies maintenance, Nortrak officials said. A permanent electrically isolated shim plate is attached to the shell of the formed steel tie, and adaptable switch plates are bolted directly onto it.
Transitioning from one switch size or hand to another is as simple as unbolting the existing plate and replacing it with the required configuration, meaning a single hollow switch tie can accommodate all turnout sizes, hands and machine positions, Nortrak officials said.
The Universal HST eliminates the need for maintainers to handle insulation during conversions, which helps enhance safety and improve signal reliability.
Meanwhile, the UNISTAR-HR - which already is a benchmark for reliability and low lifecycle costs — offers a versatile and user-friendly solution for switch operation, Nortrak officials said. As a complement, the zentrak Object Controller Point is now available, embedded within the watertight housing of the switch machine. The design allows retrofitting to any type of switch machine, including pneumatic and electric-operated systems, Nortrak officials said.
The zentrak intelligent diagnostics platform provides real-time information on the condition of switch machines and turnouts, enabling timely interventions and preventive maintenance, they said. Those features reduce downtime, improve safety, and deliver unmatched reliability and cost efficiency, Nortrak officials said.
Email comments or questions to bridget.dean@tradepress.com.
Keywords
Browse articles on Trackwork Herzog L.B. Foster Loram Plasser American RailWorks voestalpine Railway Systems NortrakContact Progressive Railroading editorial staff.