Stay updated on news, articles and information for the rail industry
March 2025
Rail News: MOW
Product update: Rail grinding 2025
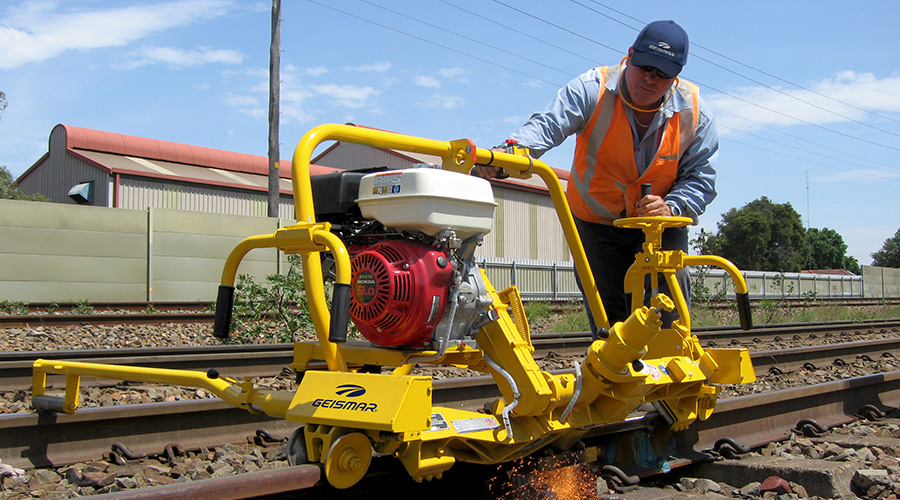
Compiled by Bridget Dean, Associate Editor
Geismar
Rail grinding is one of the most important and delicate operations in railway maintenance work. It requires expertise, know-how and good tools, Geismar officials said in an email. The company — which has operated in the rail maintenance market for over 100 years — offers a range of machines designed to perform efficient, precise and safe grinding work.
The Geismar MP23 is one of the most powerful and ergonomic rail grinders on the market, company officials said. The grinding stone’s electric lowering system ensures precise control of the grinding depth, while its powerful 6.3-kW engine enables the grinder to handle the most ambitious rail maintenance tasks. Its grinding stone head pivots 90 degrees to either side of the rail without the need to turn the machine around or carry loads while grinding — a big advantage for productivity and for the safety of operators, Geismar officials said.
For grinding work carried out in tunnels or urban areas, Geismar also offers a battery-powered electric rail grinder: the Barracuda. This machine allows the main rail grinding operations to be carried out without emitting polluting gases, Geismar officials said. It also offers reduced vibrations and noise levels.
The Barracuda is designed for precise grinding after rail welding, or other applications requiring reprofiling. It is relatively light and easy to use with an exceptional grinding quality, company officials said.
The Barracuda is designed as a versatile machine that can be used on multiple rail types, including flat-bottom, grooved and bridge crane rails.
Loram
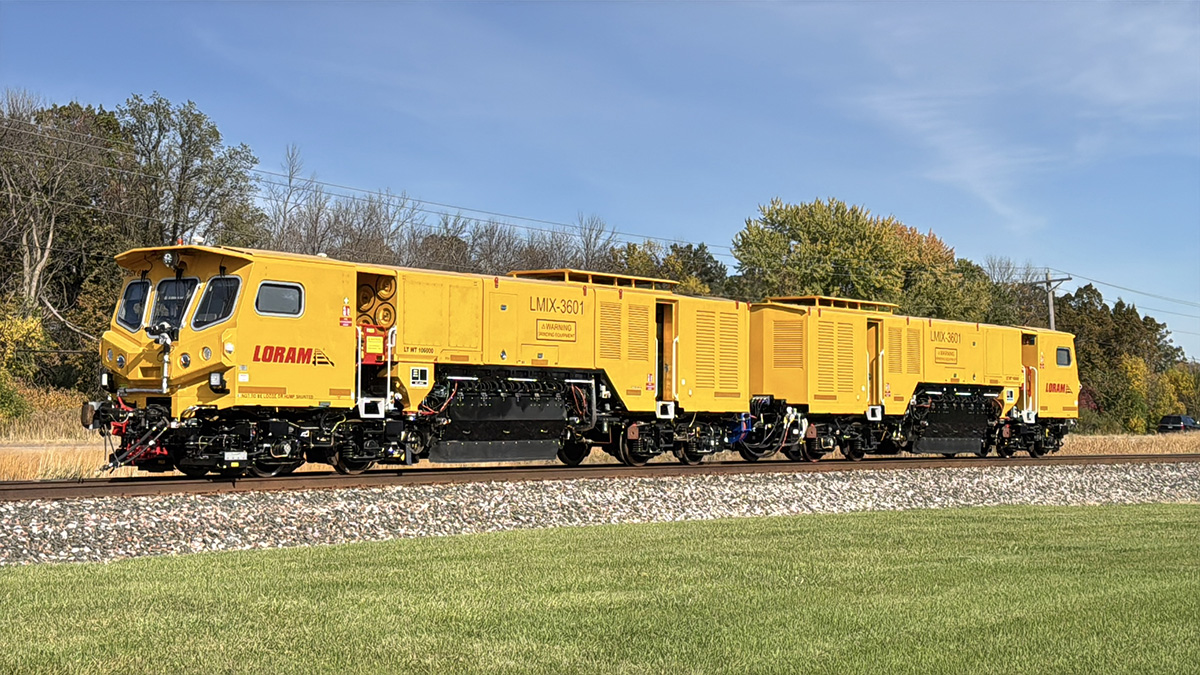
Rail grinding and milling play crucial roles in maintaining rail infrastructure, enhancing overall rail safety and minimizing service disruptions. Grinding is vital for eliminating surface defects, which, if left untreated, can lead to noise and ride quality issues. Maintaining reliable service and public satisfaction makes timely rail grinding not just necessary, but essential, Loram officials believe.
Through its specialized services and equipment, Loram significantly contributes to the reliability and longevity of railway systems around the globe, company officials said.
A standout innovation in the company’s lineup is the RGX, a new rail grinder model designed specifically for the metro industry, Loram officials said. This machine features advanced engine technology and a compact design, providing a lighter axle load. Despite its smaller dimensions, the RGX retains significant power and productivity, Loram officials said.
Designed to meet various global network requirements, the RGX can navigate tight curve radii and adhere to stringent clearance diagrams. Its light axle loads enable the grinder to be both nimble and versatile, easily addressing diverse grinding conditions, Loram officials said. The machine features a unique design element so it can operate without workers needing to disembark for set up or pack away, significantly reducing risk and enhancing workplace safety, they said.
The RGX also can be outfitted with measuring equipment, such as systems for analyzing transverse and longitudinal rail profiles. This capability ensures that all pre- and post-treatment outputs are documented, verifying that the grinding works meet the required specifications, Loram officials said, adding that doing so facilitates the prompt reopening of a network for safe train operation.
Orgo-Thermit Inc.
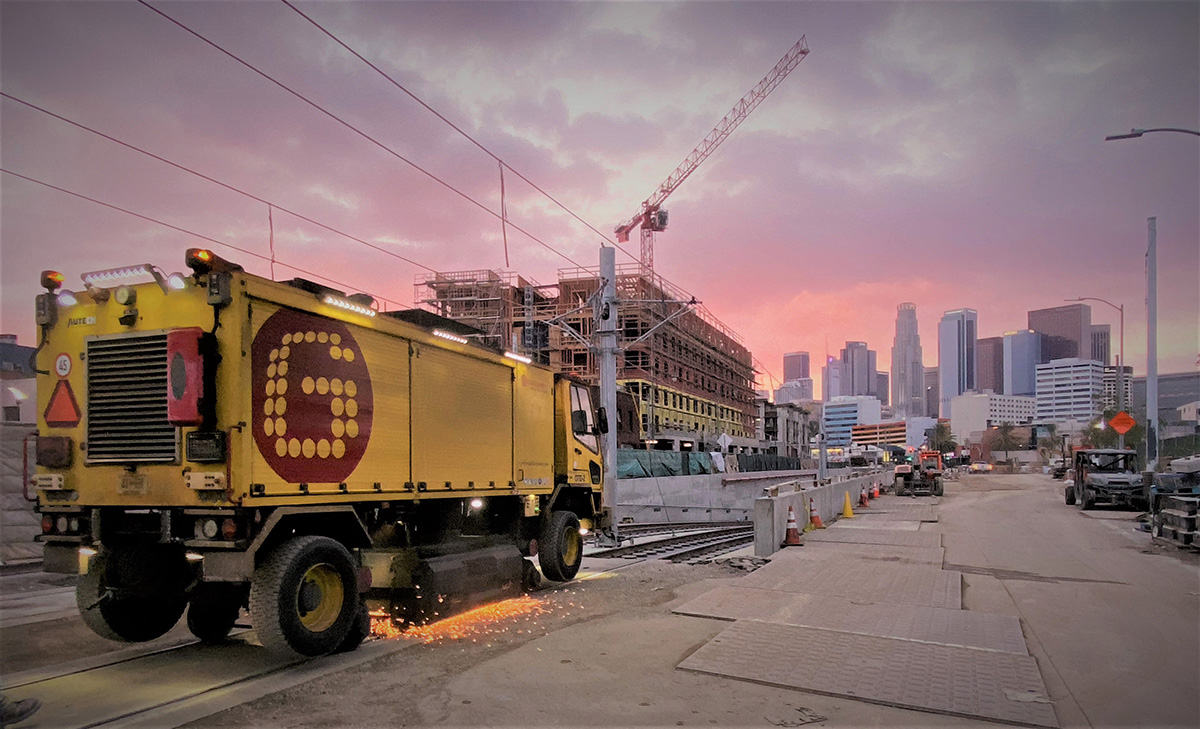
Orgo-Thermit Inc., a Goldschmidt company, offers a complete grinding service. With the ability to analyze a track using its proprietary Eddy Current system and Trackscan Mira with up to eight probes on each rail, Orgo-Thermit can obtain a full picture of the rolling contact fatigue (RFC) in a customer’s track and optimize a grinding or milling program accordingly, company officials said.
The probes measure from the gauge corner, where most RCF originates, over the head of the rail, to ensure a complete analysis.
This analysis enables Orgo-Thermit to ensure efforts are focused on the most affected areas of a railroad, as opposed to a strategy where the complete system is ground, company officials said. This saves customers money as well as the required track time to perform the work, they added. The Eddy Current system is offered as a trolley or a mounted system.
Orgo-Thermit combines the use of the Eddy Current system and its 12-stone hi-rail vehicle, which offers great performance for embedded track as well as open track, company officials said. Featuring an ability to get on and off track in less than a minute at grade crossings, the 12-stone hi-rail vehicle offers a high level of flexibility, they said.
Orgo-Thermit uses the combination of Eddy Current technology and the grinding vehicle to provide service for a number of transit agencies. Those agencies have benefitted from a focused grinding program that targets the specific areas that need addressing, which saves money by reducing the RCF and avoiding areas that do not need grinding, Orgo-Thermit officials said.
Plasser American Corp.
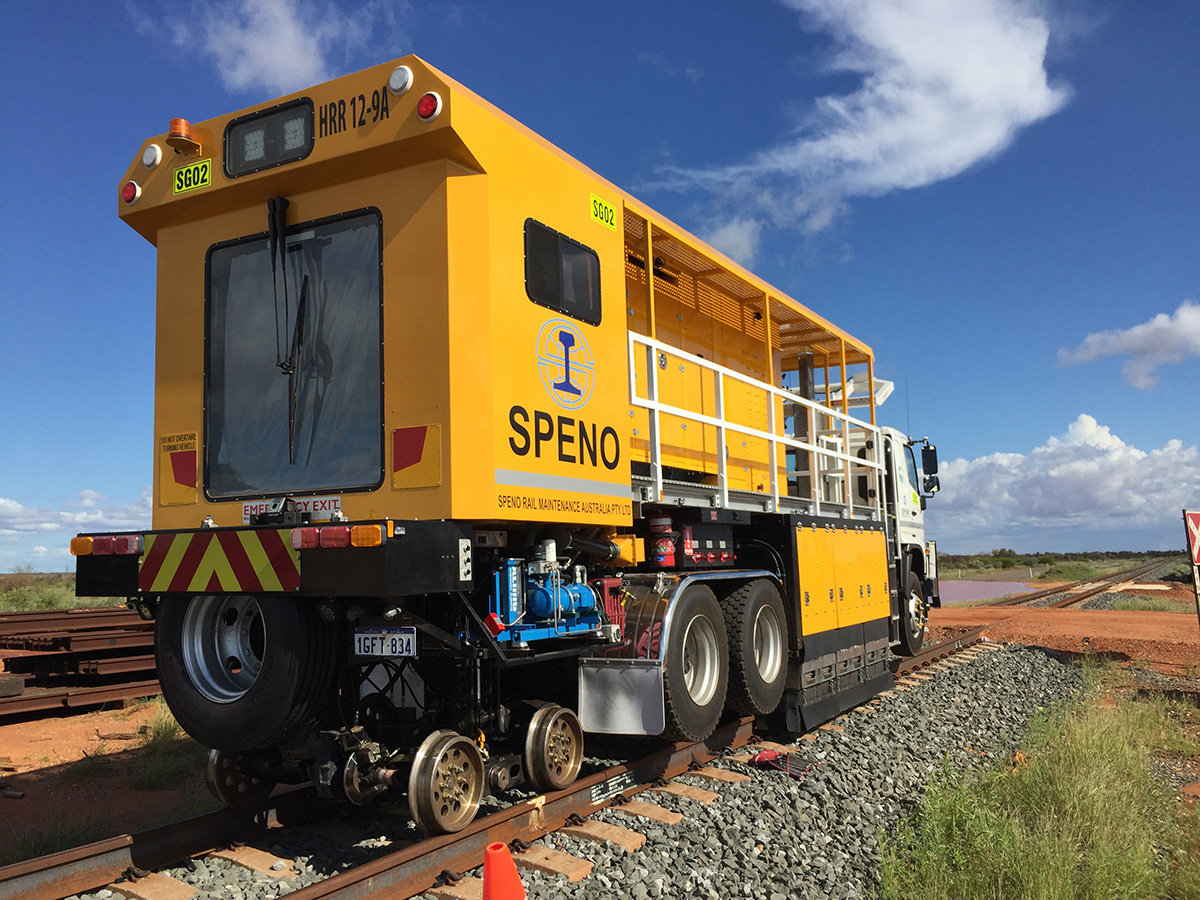
Rail grinding and rail milling have moved from a competitive situation to perfectly complementing technologies. Rail grinding is the optimal tool for preventive and medium corrective applications whereas rail milling can show its strengths for corrective and regenerative applications and in scenarios where rail grinding might be restricted or banned, Plasser American Corp. officials said.
The company is dedicated to bringing advanced grinding technology into the market. This technology will improve productivity, quality and sustainability of rail grinding in North America by drawing on the extended global expertise of Speno International, Plasser officials said.
As a first step, the company plans to soon introduce a 12-stone hi-rail truck in the market to act as a technology demonstrator. The truck can be flexibly used for mainline track and switches on both heavy-haul and transit systems, Plasser official said.
In addition, the company is operating the Romill Urban 3 E3 hybrid milling machine. Equipped with advanced milling technology, it’s designed to cope with severe rail damage and challenging track conditions while delivering superior treatment quality, Plasser officials said.
A key component for successful rail management is measurement technology to characterize the condition of the rail. For that reason, both the ROMILL Urban 3 E3 as well as Speno grinding trains are equipped with state-of-the-art technology, Plasser officials said.
With grinding and milling in one hand, the company offers comprehensive, efficient and sustainable solutions as a full-service rail treatment supplier, they said.
RailWorks Corp.
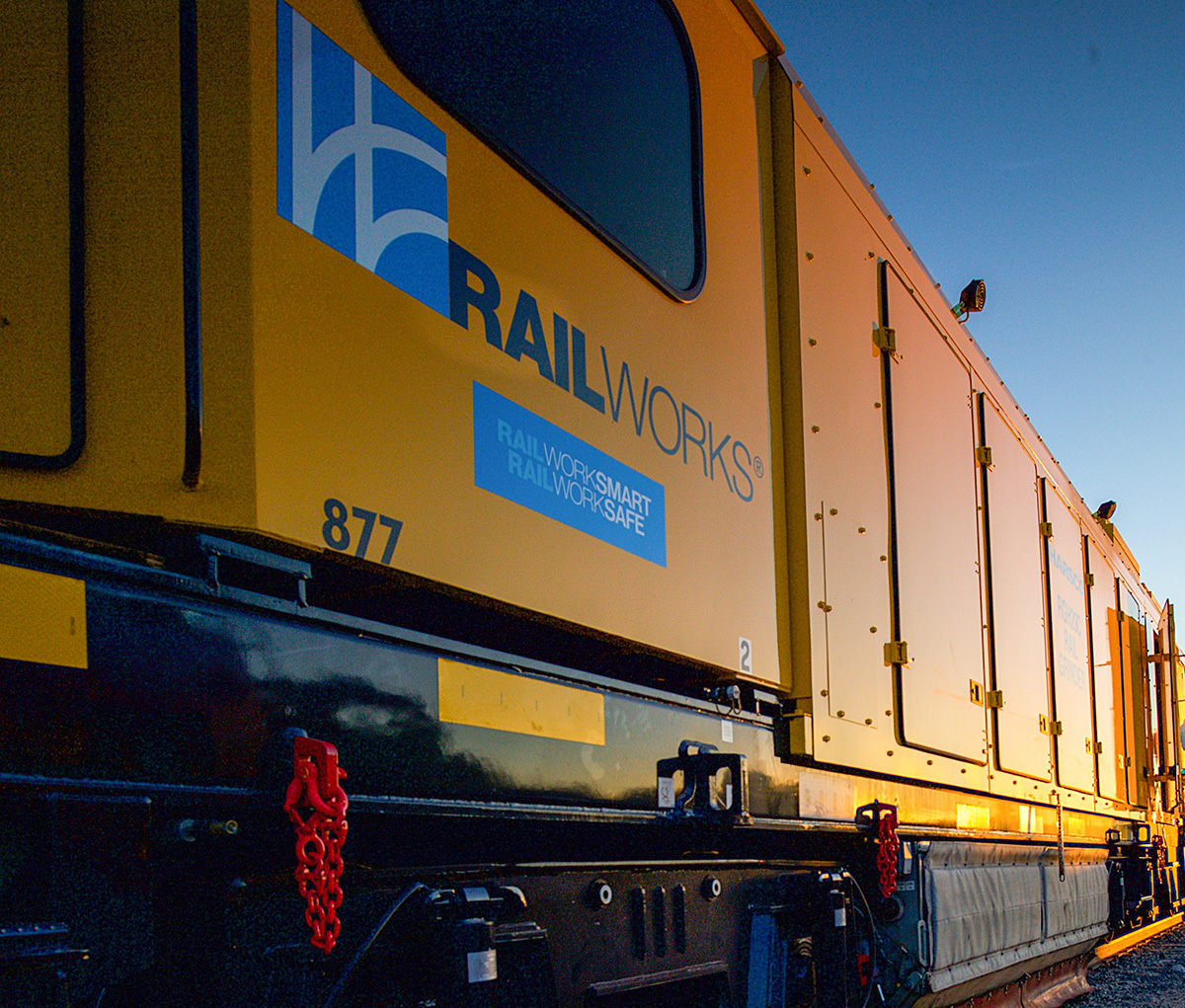
RailWorks Corp. provides advanced turnkey switch and crossing rail grinding services for both freight railways and transit lines. The company’s seasoned team ensures its services enhance durability, dependability and efficiency across customers’ rail networks, RailWorks officials said.
With a focus on safety and customer satisfaction, the company has earned a strong reputation for delivering high-performing solutions designed to thrive in high-activity environments, they said.
Those services are essential for maintaining rail longevity, reducing wear on rolling stock and improving train performance and fuel economy, RailWorks officials added. The company’s grinding solutions also can help enhance ride quality, making them a key component of an effective rail maintenance program.
RailWorks’ specialized equipment excels at grinding switches, curves and roadway crossings, company officials said. It features independent hydraulically powered grinding units, the advanced Jupiter II Control System, hydrostatic propulsion and full computerized control. Additional features include efficient dust collection, a reliable pneumatic braking system, a water mist fire suppression system and ergonomic control cabins for operator comfort.
Tailored to meet customers’ specific needs, RailWorks’ comprehensive solutions ensure safety, quality and timely performance, providing long-term value and improving the efficiency of an entire rail system, company officials said. Railworks’ crews are committed to delivering results that keep railroad operations running smoothly and safely.
Vossloh AG
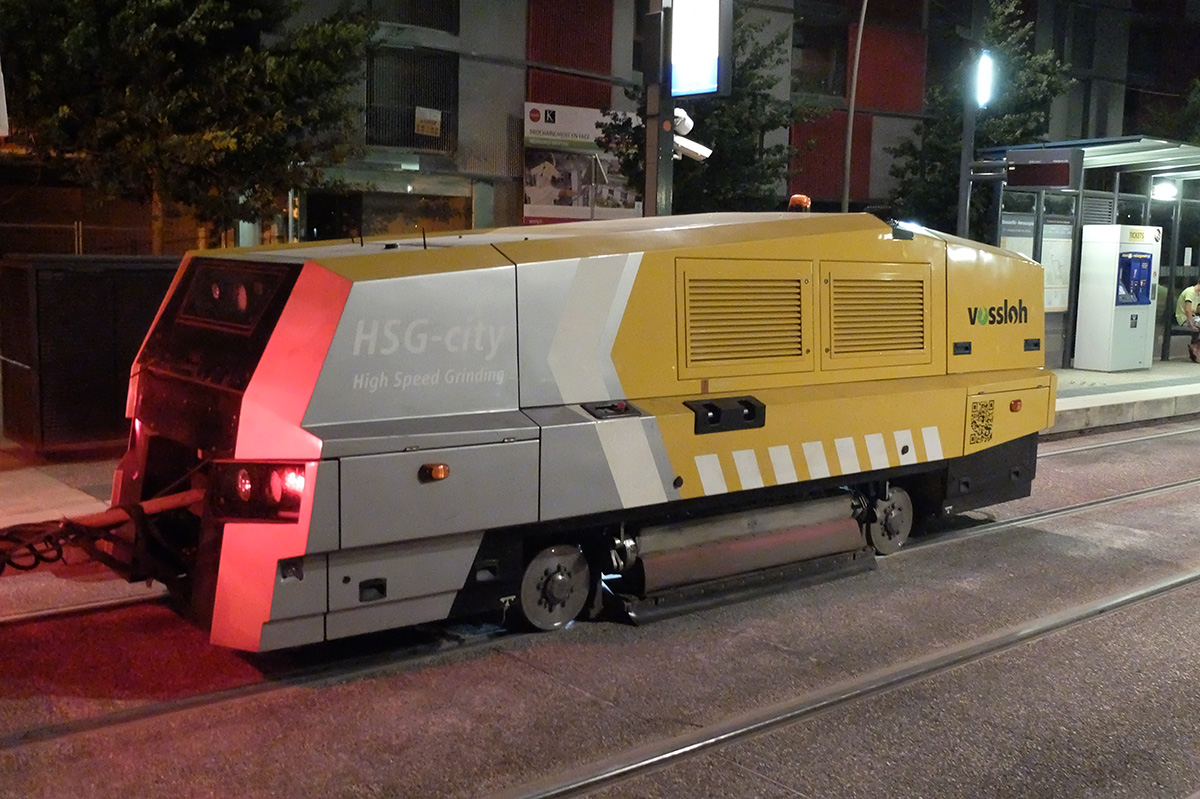
Following the launch of milling technology in North America in 2021 and numerous projects with the compact hot-spot milling machine, VTM-compact, on various networks, Vossloh now has introduced its smart High Speed Grinding (HSG) to North America.
Due to increasingly shorter track possessions, rail maintenance must have a minimal impact on overall operations. The basis for this is sound knowledge of a current track condition through digitalization, Vossloh officials said.
The very compact and extremely flexible grinding machine HSG-city is equipped with sensor technology designed to record the condition of rails (longitudinal and cross profile) during operation. The data collected is algorithmically converted directly into specific recommendations for action for Vossloh operators.
The grinding unit combines measurement, data processing, visualization and precise implementation of grinding work without requiring any track closures. And, with working speeds up to 45 mph, the HSG-city can maximize short windows of track availability between trains in revenue service, Vossloh officials said.
The company provides solutions to increasing customer requirements of cost-effectiveness, noise reduction and reliability. Initial projects in Canada and the United States on local transportation networks confirmed the success of a data-based and route-specific grinding plan that considers known hot spots that result from different rates of wear, Vossloh officials said.
Email comments or questions to bridget.dean@tradepress.com.