Stay updated on news, articles and information for the rail industry
November 2022
Rail News: MOW
Equipment update: Hi-rail technology 2022

Compiled by Jeff Stagl, Managing Editor
Brandt Road Rail
To address the needs of the North American industry for maintenance-of-way equipment fleets offering improved safety, reliability and productivity, Brandt Road Rail recently upgraded its hi-rail packages for John Deere 310/410 backhoes and model 544/624 loaders.
The company’s multidisciplinary engineering team has developed a distinguished track record with machine conversions, creating innovative solutions in one of the most modern and best-equipped facilities in North America, Brandt officials said in an email. Supported by John Deere experts, the team enhanced the equipment chassis by adjusting structure and components to ensure the optimal operation and reliability of the hi-rail unit.
The updates provide operator safety through detailed analysis and validation of system design and associated control circuits, both standard and optional, Brandt officials said. They believe the equipment is more reliable since it uses components that are readily available in the North American marketplace and is designed specifically for the Brandt John Deere lineup.
High productivity is also achieved through careful consideration of operational performance requirements while engineers integrate the purpose-built conversions, Brandt officials said. Collaboration with the John Deere team helps ensure there is no compromise to the base equipment’s performance or longevity.
Diversified Metal Fabricators Inc.
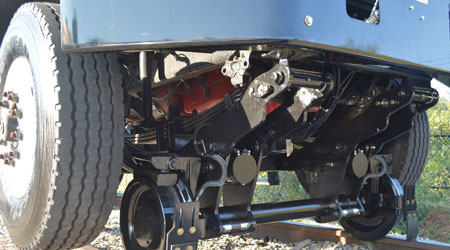
Diversified Metal Fabricators Inc. (DMF) recently redesigned its RW-1420 & RW-1630 rail gear. The company has upgraded key aspects of the Class 7 and 8 rail gear while maintaining key functions, DMF officials said.
The RW-1420-AML’s and RW-1630-AML’s standard front and rear functions include side-shift rear, over-center deployment, stub axle insulation and DMF’s new auto-mechanical lock (AML) system. All functions are designed to reduce long-term maintenance costs and improve safety, which are key drivers for hi-rail equipment end users, DMF officials said.
The AML System incorporates a spring-loaded locking mechanism in the front and rear rail gear that secures the gear in the stowed position. For safety redundancy, locking valves are built into each actuating cylinder.
For deployment, both front and rear rail gear rotate over center so no locking pins are required, DMF officials said. The design eliminates the maintenance costs associated with locking pin failure and wallowed-out pin holes on the arms and links, they added.
The company has incorporated stub axle insulation into all of its rail-gear offerings. The design removes the insulation from the wheel bearing case where there is high wear potential, DMF officials said. The insulation is designed to last the life of the rail gear and eliminate the maintenance cost associated with insulated wheels.
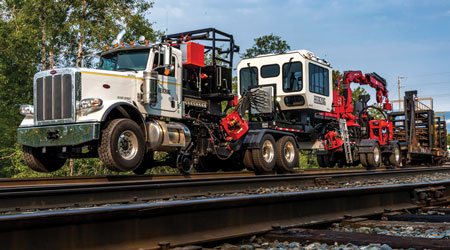
Herzog
Herzog has combined two pieces of equipment to make the rail-handling process safer, more productive and more reliable.
When operated together, Herzog’s Rail Unloading Machine (RUM) and Automated Tie-down Car® (ATC) can help railroads maximize their operations, company officials said. The dual machines can eliminate the need for manual intervention in rail transport and delivery from start to finish.
In a conventional rail unloading process, there are countless contacts that workers make with the rail using a winch car, which increases the potential for injuries. Alternatively, the RUM’s two-person crew directs the entire activity from inside an operator station with 360-degree visibility, Herzog officials said. They can maneuver the RUM’s knuckle boom crane to pull a rail off of a rail train and into a power box, feeding it through the machine and unloading it at the same speed a train is traveling.
Once unloading is complete with the RUM, there is no need to take up valuable track time planning equipment sequencing to reach another job site, Herzog officials said. Within a few minutes, the hi-rail vehicle can disengage from a rail train and exit a track at a grade crossing. The RUM’s portability offers scheduling flexibility with a quick setup.
The ATC further complements the RUM’s hands-free operation because crews do not need to wait while tie-down car personnel manually clamp or unclamp rail with impact wrenches. Continuous-welded rail is loaded and secured on a rail train at the manufacturing plant with powerful hydraulic clamps, then transported to a job site with fail-safe, mechanical holding power, Herzog officials said.
At a job site, a rail is more easily unclamped from a rail train via remote control from the safety of the RUM’s operator station, they said. A process that usually takes an average of five minutes per rail to perform manually can be achieved in 5 to 10 seconds with the ATC. The RUM and ATC can unload a 50-pocket rail train on one or both sides of the track in less than four hours.
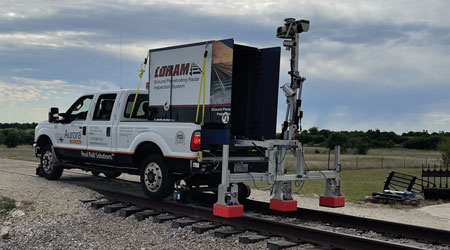
Loram Technologies Inc.
Loram Technologies Inc. (LTI) provides ground penetrating radar (GPR), LiDAR measuring services and imagery along with data analysis for substructure condition evaluations that involve hi-rail equipment for data collection.
GPR provides a continuous measurement of subsurface conditions, including layer configuration, moisture content and the fouling condition of ballast. LiDAR data and digital video images are collected to further evaluate right-of-way and track conditions, or for drainage design, the accurate location of assets and detecting the root cause of problems, such as shoulder heaves and insufficient internal/external track drainage.
To facilitate GPR and LiDAR inspection services and better adapt the technology for different inspection conditions (gauges or transport vehicles among them), LTI has developed a self-contained inspection box that can be set on the back of a small hi-rail pickup truck or a large hi-rail flatbed truck to collect data.
Weighing about 1,000 pounds and stretching 40 inches wide, 72 inches deep and 72 inches tall, the box features three-channel 400 MHz GPR antennas, dual LiDAR, a high-quality GPS with integrated IMU and rear-facing cameras. Those items are folded in the box and can be unfolded by pressing a button.
The system only requires an encoder feed and power cable connected to a truck’s 12-volt battery, and the operator can connect to the system wirelessly for data collection, LTI officials said. The antennas’ distance and height can be adjusted to operate on narrow, standard and wide gauges, and height can be maintained for different truck beds.
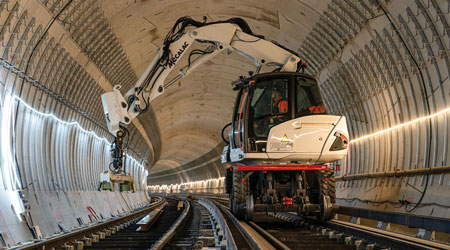
Mecalac
Late last year, Mecalac introduced a new MRail-Series, a dedicated line of excavation equipment for the rail industry. The line consists of four models with features designed to help meet the needs of rail crews, whether for maintenance-of-way work or constructing new tracks, Mecalac officials said.
Offering advanced safety features, high-level performance and versatility, the line is tailored to meet the requirements and track sizes of public and private railroads, light-rail systems and subway networks, they said.
The MRail-Series includes two tracked and two wheeled excavators that are positioned on hi-rail wheels to travel on rail. The wheels can be re- or de-railed by the operator.
The two tracked models — 106MRail and 136MRail — are based on the MCR crawler skid excavator concept and designed for various applications. The 106MRail can travel up to 6.2 mph on ground and 14.3 mph on rails, while the 136MRail reaches ground speed up to 5.6 mph and rail speed up to 12.4 mph.
A crawler-based excavator with factory integrated hi-rail, the 136MRail combines all the functions of a state-of-the-art excavator with lifting, towing and loading capabilities, Mecalac officials said. With its rail gear raised, the machine — which is designed for Class I, light- or industrial-rail operations — can be operated as an excavator on regular terrain.
The 156MRail and 216MRail wheeled models are tailored to various rail networks, different track sizes and available workspaces. The 156MRail can reach ground speed up to 21 mph and rail speed up to 18.6 mph, while the 216MRail can travel at speeds up to 18.5 mph on both ground and rail.
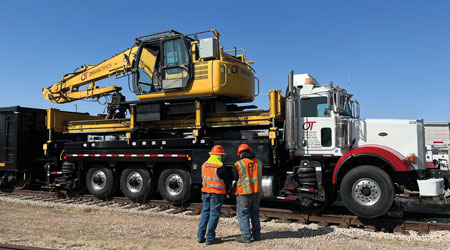
Omaha Track Equipment
The Class Is’ shift to precision scheduled railroading has created opportunities for innovation to help reduce the operational impacts of material handling in condensed work windows. Omaha Track Equipment has re-engineered its existing resources to provide additional value to customers and maximize efficiency, company officials said.
The company is currently using heavy-duty car-mover trucks that can pull flat cars and/or gondolas with an excavator to handle all types of railroad materials.
“This new spin on long-standing material handling concepts has increased our productivity by reducing handling and stockpiling of materials,” Omaha Track officials said.
In addition, the company is offering road-to-rail power by the day for maintenance-of-way, bridge rehabilitation and construction projects. Omaha Track owns and operates Brandt Power Units for internal operations and now is making that equipment available for outside short-term car pulling and spotting needs.
The OT power program package includes one Brandt Power Unit with up to 60,000 pounds of tractive effort and one qualified operator available for 10 hours per day, seven days per week.
Omaha Track also provides hi-rail grapple, section and rotary dump trucks, pickups, and rail and tie carts for sale or rent, with differing rental and purchase options.
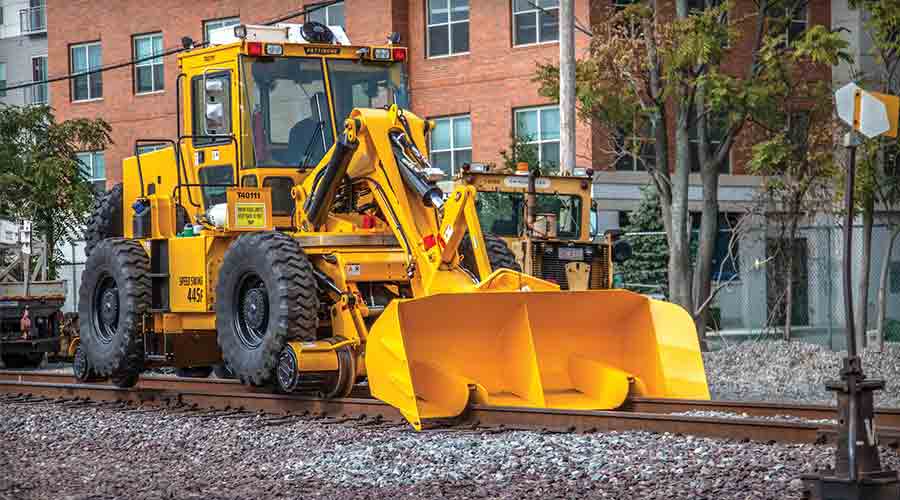
Pettibone Traverse Lift LLC
Featuring an updated design, the Pettibone Speed Swing 445F rail crane offers precise hydraulic engineering and ample power to lay rails, set ties and perform numerous other tasks, Pettibone Traverse Lift LLC officials said.
The Speed Swing 445F is powered by a 163-horsepower Cummins QSB4.5 Tier 4 diesel engine and features a Dana T20000 3-speed transmission with twist grip electric shift control that provides high torque. The rail crane’s front-load capacity is 10,000 pounds and side-load capacity is 8,000 pounds.
Operators can move the Speed Swing between job sites at 25 mph on hi-rail and at 20 mph with all-terrain rubber tires. Along with four-wheel drive and rear-wheel disconnect, the tires allow greater maneuverability off rails, company officials said.
Offering 180-degree boom rotation, the 445F model is primarily used to thread out and thread in rail, they said. An optional magnet package can be used to pick up old plates, spikes and small pieces of rail. The unit can also tow rail carts, move rail cars and supply air or hydraulics for hand tools.
Pettibone Traverse Lift offers X-Command® as one 445F option. The Pettibone telematics program is designed to provide real-time access to machine data. The platform allows for remote diagnosis, eliminating the need for certain field service calls, company officials said.
RCE Equipment Solutions
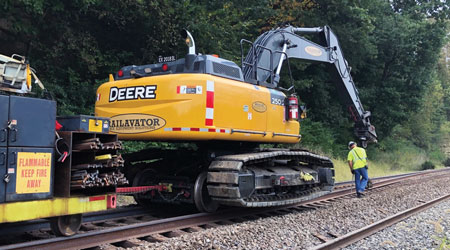
RCE Equipment Solutions provides all makes of hi-rail gear for Komatsu, Caterpillar and John Deere 20 metric-ton excavators. The company’s gear is a patented hydraulic hi-rail system.
The 20 metric class Railavator is designed for rail maintenance applications such as rail laying, tie handling, scrap pickup, undercutting and ballast and site preparation. The rail-gear package can be fitted with features designed to simplify service and minimize downtime and costs, RCE officials said.
In August, the company announced a new series of Railavators: the John Deere Models 210G, 245G and 250G hi-rail excavators. They feature RCE’s new “Ultra Life Axles,” which are final drives made of high-strength alloy steel that offers two times more structural strength than existing cast-iron final drives, company officials said.
The new series of Railavators features many design enhancements, including a new hydraulic system. They have more components in the common manifold, meaning fewer hoses and separate components, and less joints that could potentially leak. A push-button monitor controls the hi-rail gear and all available attachments from inside the cab.
RCE also announced that 50G, 85G and 135G Railavators feature an adjustable lower track frame. When retracted, the machine is now under the legal size for transit-rail work without a required permit, company officials said. In work mode, the hydraulically operated frame expands to straddle a track.
The three Railavators are ideal for rail customers and contractors seeking to perform work in more compact environments and gain easier transport, RCE officials said.
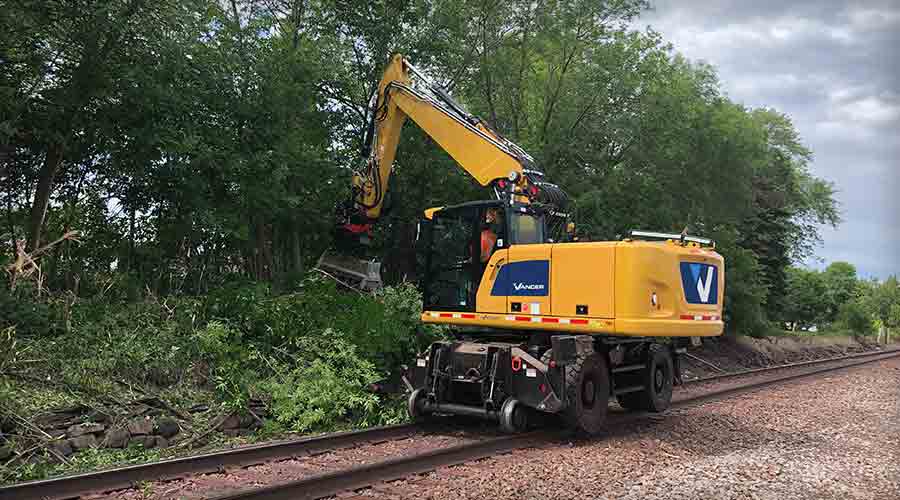
Vancer
Vancer continually strives to provide rail maintenance crews with various hi-rail machines that are designed to tackle a wide variety of MOW projects.
One such machine is the CWX20 Wheeled Hi-Rail Excavator, which offers 16% more swing torque and more than 170 horsepower. Paired with its hydraulically powered hi-rail gear undercarriage, operators can more easily perform undercutting, trenching, tie insertions, tamping, brush cutting and other tasks, Vancer officials said.
Since equipment uptime is critical, customers need the flexibility of remote monitoring for their hi-rail excavator fleet, they added. To that end, Vancer offers the Danfoss Plus one system on all next generation hi-rail excavators. The system features remote diagnostics and real-time data monitoring that provides machine updates 24/7.
As rail demand continues to rise in the nation, MOW work becomes exponentially more important, so Vancer aims to drive innovation to help alleviate the strain on rail infrastructure and keep tracks safe, company officials said.
Email questions or comments to jeff.stagl@tradepress.com.