Stay updated on news, articles and information for the rail industry
August 2020
Rail News: MOW
Equipment update: Material handling
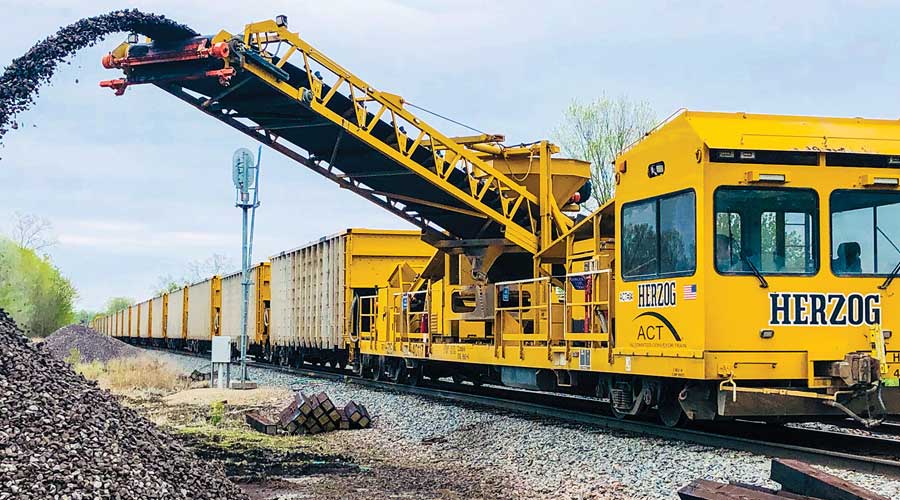
Compiled by Vesna Brajkovic, Associate Editor
Progressive Railroading last month reached out to a sampling of material handling equipment suppliers to share information on some of their newest or in-demand offerings — from ballast excavators to rail threading machines to rail cranes. Emailed responses from 10 suppliers follow.
Georgetown Rail Equipment Co.
This year, Georgetown Rail Equipment Co.’s (GREX) material handling equipment — including its DumpTrains, Slot Trains and Self-Powered Slots — are in demand, especially the DumpTrain for Curves. To keep up, GREX has continued to add to its fleet.
The company’s second generation tie set-out solution has been deployed on multiple systems throughout the country, and several more deployments are planned. The tie set-out system uses data collected from the Aurora automated tie-inspection system to determine where ties need to be replaced. The system improves the tracking of tie distribution and increases efficiency within tie gangs, GREX officials said.
Last year, the company introduced its second generation GateSync and HydraDump kits for the automation of ballast cars and side-dump cars. The new GateSync kit offers a closed-loop communication system between the cars and the operator to accommodate longer train lengths and faster set-up and performance times, GREX officials said.
Both the GateSync and HydraDump kits are ideal for car rehabilitation programs or new car builds, they said.
Herzog
Herzog offers comprehensive services in maintenance of way, material handling and new track construction that involve versatile equipment. The machinery can help increase productivity and safety for right-of-way maintenance by transporting, loading and unloading high volumes of materials to work sites across the country, Herzog officials said.
To solve the challenge of base rock distribution, Herzog recently improved the ballast delivery system on its Automated Conveyor Train. This second-generation system will be released in fall with changes to the geometry of the hopper car, belts and gates. The redesign will yield a faster discharge, increasing the flow rate by 30 percent, Herzog officials said.
To find efficiencies in unloading base rock and reach optimal production standards, Herzog’s research and development team studied material properties and undertook extensive testing with various design considerations to ensure the company’s equipment could handle base rock across the spectrum of size and moisture content, said Michael Mastio, president of Herzog Railroad Services Inc.
Industry-Railway Suppliers Inc.
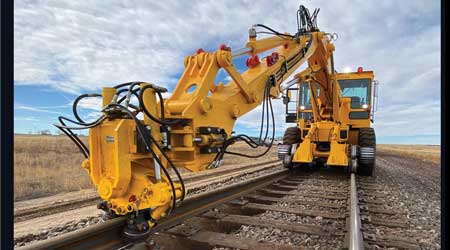
Industry-Railway Suppliers Inc. is a distributor of Swingmaster machines, which have provided the rail industry with custom-engineered material handling equipment since 1985. Swingmaster is a leading producer of U.S.-made mobile hi-rail swingloaders designed specifically for the railroad industry, Industry-Railway Suppliers officials said.
The Swingmaster Rail Threader (SRT) is the newest addition to the company’s product line. At the boom tip, the SRT’s rail-threading workhead uses a four-axis, electronically controlled, hydraulic manipulator head to offer complete control of the rail threading operation. The manipulator head is designed to rigidly constrain the rail during threading, enabling installation of rail into curve block plates and existing spiked plates for out-of-face rail remediation, along with handling of tipped rail.
The SRT’s mechanical boom-swing prevents fouling of adjacent track and its dual-sided operator cab improves visibility. The SRT does not require certifications associated with operating a crane.
Industry-Railway Suppliers also provides track tools, abrasives, heavy equipment, work equipment wear parts and mechanical shop tools to railroads, transit systems and contractors throughout North America.
L.B. Foster Co.
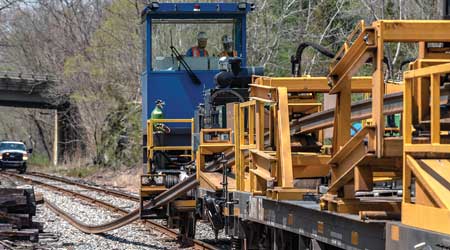
In third-quarter 2020, L.B. Foster Co. plans to upgrade the fleet of trains it operates to ship continuous-welded rail (CWR) to railroads and transit agencies throughout North America.
Rail industry trends over the past several years continue to have an impact on CWR demand, handling and distribution. Despite soft economic conditions, demand for CWR remains solid, L.B. Foster officials said.
For track replacement and expansion work, railroads and transit agencies remain committed to transitioning from the use of stick rail — or individual pieces of rail that require joints — to welded or ribbon rail. Welded rail results in a safer, smoother track that requires less maintenance, L.B. Foster officials said.
Additionally, as precision scheduled railroading continues to be implemented, it’s important that customers can unload trains carrying CWR as quickly as possible, they said.
Railroads and transit agencies also continue to outsource more functions, including offloading rail. To meet that growing need, L.B. Foster offers a range of services, including project management, unloading supervision and full unloading crews.
For example, the company supplies an unloading operator supervisor with every CWR train to ensure safe and efficient operations. L.B. Foster also can furnish full unload crews and equipment when requested to help reduce unloading times to as short as one day.
Loram Maintenance of Way Inc.
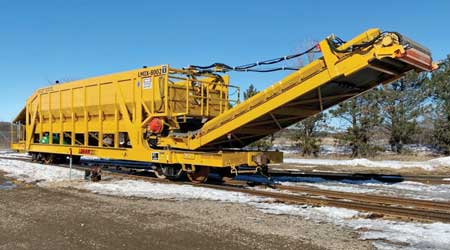
Loram Maintenance of Way Inc.’s newest addition to its line of ballast maintenance equipment is the MHC60 Material Handling Car. The MHC60 transports and offloads new ballast or excavated roadbed materials, such as ballast and spoils.
The car can self-unload into another MHC60 or directly into the right of way, and can connect to and receive materials from any undercutter, shoulder ballast cleaner, ditch cleaner, LRV specialty excavator or other material handling cars.
The MHC60 features 60-cubic-yard hopper capacity, which exceeds the industry standard throughput by up to 30 percent. The car can discharge material up to 20 percent further to either side of the track centerline compared with other material handling cars in the market, Loram officials said.
The transfer conveyor is equipped with dual-speed motors that can shift to high speed to cast material over 20 feet from a track centerline, or to low speed/high torque to discharge the heaviest loads. The cast distance is far enough to eliminate secondary handling to move the discharged material further away from a track centerline, reducing the total amount of equipment required for a project, company officials said.
To prevent unintentional overload, Loram designed the transfer conveyor with enough torque and horsepower to prevent stalling.
The offload rates and cast distances allow for quicker turns between filling and unloading, leading to increased production for the excavating equipment, company officials said.
Omaha Track Inc.
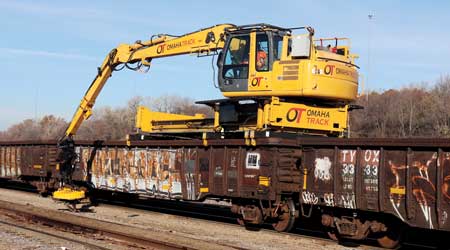
Omaha Track Inc. now offers the full-service ability to pick up rail and other track material (OTM) using an OTM tracker and power unit combo. The service involves providing the equipment and labor to load rail and OTM directly into rail cars instead of transporting it to load-out locations.
In addition, Omaha Track now offers a tie reclamation service using two flat cars with an excavator and power unit. The company can pick up and load out 1,500 to 2,000 ties in one move to different load-out locations.
The services minimize material touches and eliminate the need to wait for power from a railroad to move a car between load-out locations, helping to boost efficiency and reduce cost, Omaha Track officials said.
The company’s power unit used in both services has the added advantage of traveling by road instead of exclusively by rail, which makes asset deployment and arrival timelier, company officials said.
Pettibone
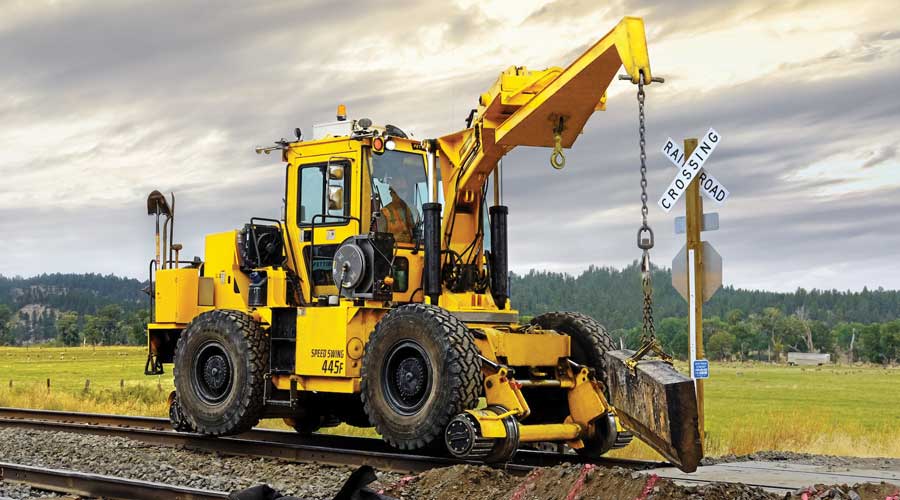
Pettibone updated its Speed Swing 445F rail crane to be more versatile for multiple rail applications. The 445F offers precise hydraulic engineering and ample power to lay rails, set ties and perform numerous other tasks, Pettibone officials said.
The rail crane is powered by a Cummins QSB4.5 Tier 4 diesel engine that offers fuel savings up to 10 percent over the previous model. The machine offers a front-load capacity of 10,000 pounds and side-load capacity up to 8,000 pounds, and can travel at 25 mph via hi-rail and 20 mph with all-terrain rubber tires.
The tires — along with four-wheel drive and a rear wheel disconnect — also allow greater maneuverability off the rails to simplify most jobs, company officials said.
Providing 180-degree boom rotation, the 445F is primarily used to replace old rail, but it also can serve as two rail carts, move rail cars and supply air or hydraulics for hand tools.
The rail crane can be built to customer specifications for particular applications. Common options and attachments include a tote boom, hydraulic tool circuit, magnet package, AAR coupler, track cleaning bucket, load bucket, 20-foot extendable boom, fork frame, backhoe, brush cutter and snow plow.
Plasser American Corp.
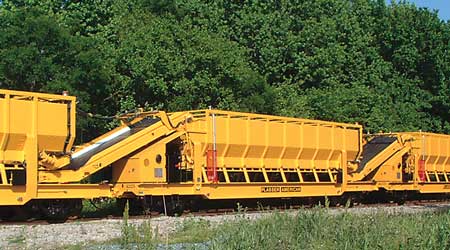
Plasser American Corp. produces MFS Conveyor and Hopper Cars designed to transport ballast, spoils or other materials in trains to and from various work sites, as well as work with various machines.
The equipment has been in operation for many years, with hundreds of units delivered, Plasser American officials said.
The advantage of the MFS is its ability to transport, store, load and unload material as a single unit or with other like units, they said. Each MFS car is individually powered with its own engine, hydraulic supply and electrical system, and its material storage capacity can be increased by coupling multiple units.
MFS cars are available in various sizes from the MFS15 to the MFS120 to meet customer needs and loading and clearance restrictions.
The floor of the MFS has a wide, hydraulically driven, variable-speed conveyor belt, and the front of the unit features a rotatable, hydraulically driven conveyor. The front conveyor is used for unloading the MFS or transferring material to another MFS, a ballast-distributing machine or other hopper cars into trucks or onto a rail right of way.
Used with the BDS100/200, MFS cars can be used to increase the storage capacity of ballast for a more cost-effective means of ballast management, Plasser officials said. MFS cars loaded with new or clean ballast also can be used to feed ballast onto a track via a Plasser undercutter.
RCE Equipment Solutions Co.
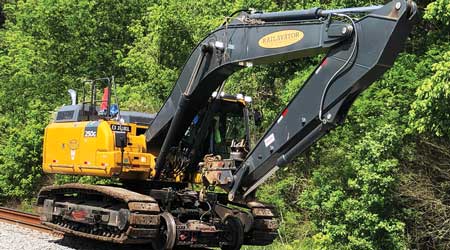
RCE Equipment Solutions Co. (RCE) released a new series of Railavators hi-rail excavators, the company’s most popular machine.
The new series include John Deere 210G, 245G and 250G model hi-rail excavators that feature RCE’s new Ultra Life Axles and hydraulic-powered, retractable hi-rail. The Ultra Life Axles sport increased axle bearing capacity, and are rebuildable and repairable, RCE officials said.
The new Railavators’ hydraulic system now includes more components in the common manifold, which means less hoses, separate components and joints that potentially could leak.
The company also updated the Railavator structure, including the hi-rail linkages and supports, to extend support gussets and add weight to the links and frames. The modifications reduce frame flexing and potential cracking, company officials said.
The drive axle mounting has been changed for more strength and durability, and an improved rotary manifold has a higher pressure rating and longer life, they said.
RCE also provides all makes of hi-rail gear for Komatsu, Caterpillar and John Deere 20 metric-ton excavators. The 20 metric class Railavator is ideal for such rail maintenance applications as rail laying, tie handling, scrap pick up, ballast and site preparation, and undercutting.
Vancer
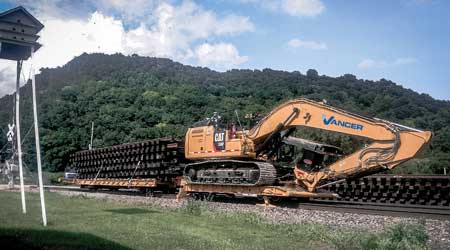
Vancer engineers, builds and distributes maintenance-of-way equipment for the rail industry. Its product line ranges from the mini excavator to the CHX25 Hi Rail Excavator for hauling and distributing loaded rail cars, ballast carts and tie carts to the Hi Rail CTB41.
Vancer’s Hytracker Rail Cart’s low-profile and heavy-duty construction creates a sturdy platform for a variety of equipment, company officials said. The ballast cart is designed to remotely distribute ballast from the cab of the excavator on the rail cart that is pushing or towing it. The tow cart is available with a 100,000-pound capacity.
Paired with the company’s attachments and maximum power for material handling and transport, Vancer offers products engineered to enhance operator ease of use for all material handling projects.
For example, operators of the company’s Cat-based hi-rail equipment, rail bound machines and Hytracker can handle concrete and wood ties with greater visibility and enhanced tie placement accuracy, company officials said.
Email comments or questions to vesna.brajkovic@tradepress.com.
Keywords
Browse articles on MOW material handling equipment Georgetown Rail Equipment GREX GateSync HydraDump Herzog Automated Conveyor Train Michael Mastio Industry-Railway Suppliers Swingmaster Rail Threader L.B. Foster continuous-welded rail Loram Maintenance of Way MHC60 Omaha Track Pettibone Speed Swing 445F Plasser American RCE Railavators Vancer Hytracker Hi Rail ExcavatorContact Progressive Railroading editorial staff.