Stay updated on news, articles and information for the rail industry
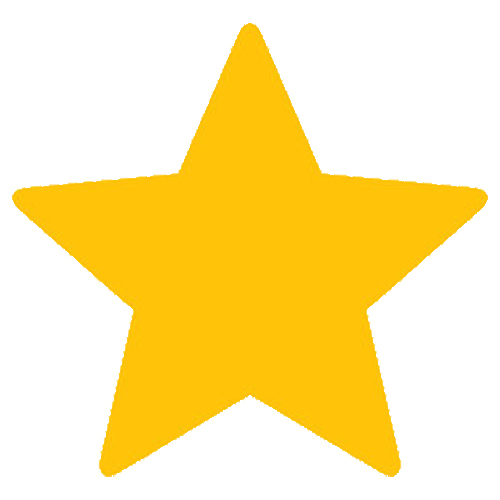
December 2023
Rail News: MOW
Fasten statements: Rail fastener and fastening system suppliers share product-line updates
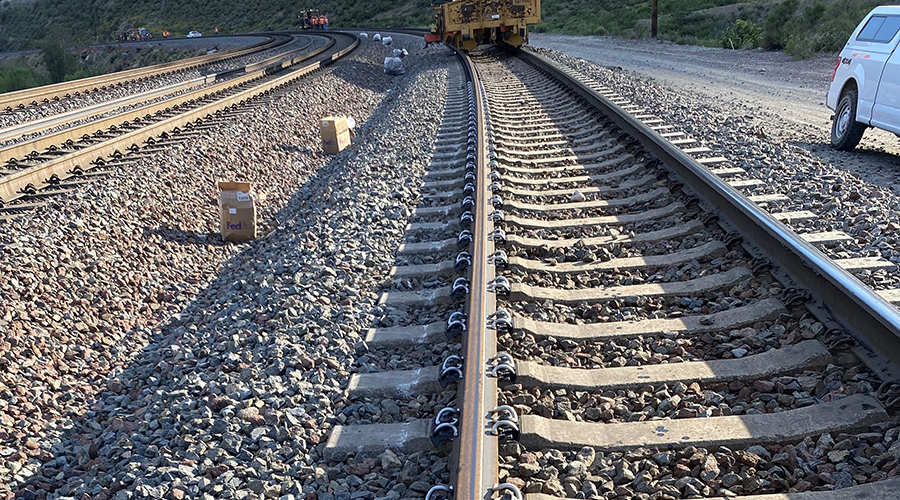
Compiled by Michael Popke
Vossloh
As rising traffic volumes lead to higher stress on rail infrastructure, the need for technologies that counteract wear and tear increases. Vossloh’s compact new M-generation tension clamps feature outwardly curved spring arms. Their geometry — which resembles a cursive “M” — provides both a larger contact area with the rail base to reduce contact stress and increased three-dimensional fatigue strengths, company officials said in an email.
In consideration of rising rail temperatures as a result of global warming, improved lateral track stability is becoming increasingly important, they said. The higher torsional resistance of the M9 is engineered to allow a higher critical rail temperature without causing lateral displacement.
A new micro-steel alloy, low-stress bending and enhanced hardening process contribute to improved performance and decreased carbon dioxide emissions, lowering lifecycle costs on a comparative basis and allowing use of more elastic rail fastening systems to further increase robustness and safety, Vossloh officials said.
Compatible with existing rail fastening systems, M-generation clamps combine properties of several previous clamp designs and are designed for nearly all North American applications. Installed in multiple demanding Class I revenue service locations over the past two years, the clamps “will continue to roll out more widely,” Vossloh officials said.
Progress Rail
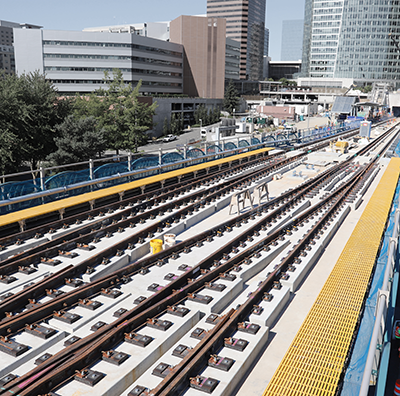
Progress Rail, a Caterpillar company, supplies a full line of fastening systems for heavy haul and transit railroads, ranging from the e-Style Clip to the Loadmaster DF for timber ties to the ADFF55 high attenuation direct fixation fastener.
For example, the DF Block System — which eliminates the risk of irregular support surface conditions, honeycombs in the concrete and improper elevation setting of concrete-embedded inserts — significantly improves the quality of direct-fixation fastener installations for both standard and high attenuation units, company officials said.
On the Los Angeles Westside Purple Line Section 1, the DF Block System has reduced installation time with less material handling and fewer personnel required for the same work, they said. The system also is designed to improve the life expectancy of DF units, reduce maintenance and provide initial installation savings compared with the top-down construction technique.
From rail anchors and all styles of clips to DF and ballast mats to turnouts, lift frogs and crossovers for transit, commuter and HAL applications, Progress Rail provides a full range of fastening and special trackwork solutions.
voestalpine Railway Systems Nortrak LLC
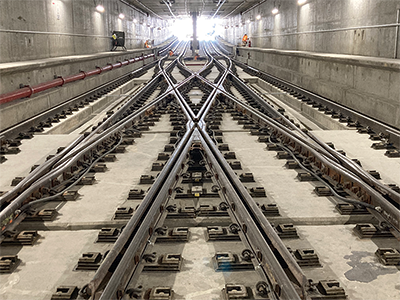
Now with a portfolio expanded beyond special trackwork, voestalpine Railway Systems Nortrak LLC provides a range of system solutions, including rail fasteners, concrete ties, switch machines and wayside condition monitoring. To that end, Nortrak has continued to grow its rail fixation business to include different types of rail fasteners and crossties.
In June, Nortrak acquired CXT’s concrete-tie business in Spokane, Washington. The company is now the only North American trackwork supplier with in-house production of direct-fixation fasteners, concrete ties, ductile iron tie plates and shoulders, injection molded plastic components and resilient rail clips for both turnout and mainline applications, Nortrak officials said.
“Having control of our own supply chain will allow us to provide exceptional quality, meet customer delivery needs, accelerate new product development and provide unmatched value to our freight and passenger customers, supporting them in their mission to move trains safely, reliably and cost effectively,” said John Strout, Nortrak’s senior vice president of fixation strategy and development.
Customers are beginning to see the value of Nortrak’s integrated systems approach with such products as the Keyway Concrete Tie for use in wood-tie track to improve gauge performance, High Attenuation Trackwork DF Fasteners for use in noise-sensitive urban environments and the NT2060 Safelok I style long-reach clip system for ongoing maintenance needs, he added.
L.B. Foster Co.
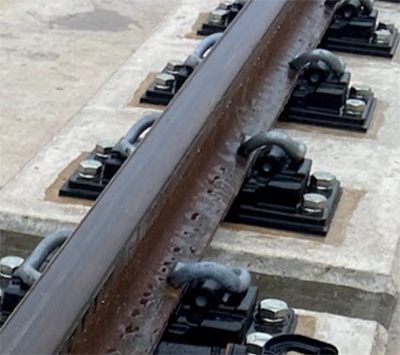
L.B. Foster’s Transit Products Division offers more than 70 different styles of direct-fixation fastener designs for a range of transit-rail and heavy-haul applications across the United States and Canada.
The fastener technologies offer an array of performance characteristics to suit each customer’s rail application needs, including noise and vibration mitigation, rail profile, rail seat height, cant requirements and lateral adjustment. They also can match existing footprints and anchorage locations, add additional anchorage locations (two versus four), address loading requirements and provide ease of installation and/or maintenance, L.B. Foster officials said.
The company produces fasteners for single rail, restraining rail, expansion joints and special trackwork in both standard and high-resilient stiffness options. L.B. Foster also offers both fixed rail clip shoulder housings and adjustable rail clip shoulder housing options for its special trackwork fastening systems.
The company’s newest fastener is the Model F52 fastener, which is designed to offer the performance of a high-resilient fastener in a standard direct-fixation fastener footprint and height. The Model F51 fastener series is a resilient, rubber-bonded SRS plate-pad replacement for wood-tie applications.
That fastener is currently being installed as part of the Chicago Transit Authority’s Red and Purple Line Modernization project and was recently approved for use on the Maryland Transit Administration’s Purple Line project for wood-tie applications, L.B. Foster officials said.
Lewis Bolt & Nut Co.
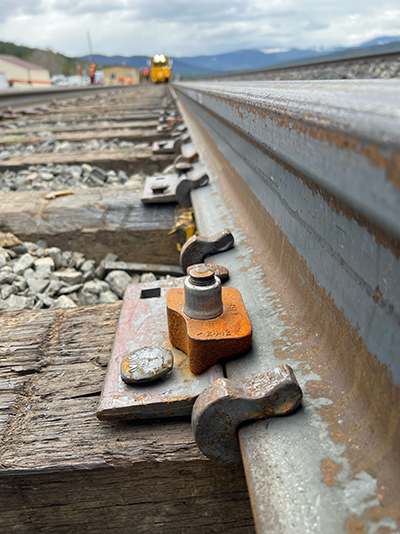
Lewis Bolt & Nut Co.’s introduction of the Viper-1® drive-on rail anchor represents a significant advancement in the rail fastener space, company officials said. Developed in collaboration with freight railroad partners, the anchor addresses critical challenges railroads face, thereby enhancing both performance and sustainability.
One main feature of the Viper-1 is its increased holding power, featuring a minimum capacity of 9,000 pounds, surpassing AREMA standards. Additionally, the Viper-1 design allows for deeper anchoring on the tie — the feature minimizes tie/plate cutting and therefore extends the life of the ties, company officials said. The improved tie-bearing surface also reduces wear and tear on the infrastructure.
The Viper-1 jaw design allows for easy removal and reapplication, making it a reusable solution that retains its initial holding power over multiple uses, company officials said.
Lewis Bolt & Nut produces a range of conventional drive-on anchors, screw spikes (such as the patented Evergrip G2® and Permagrip®), track bolts, recessed head timber screws, frog and switch bolts, and a diverse selection of bridge fastener hardware.
Pandrol
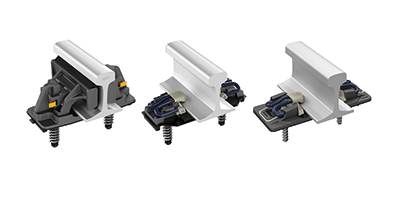
Pandrol’s Common Interface System offers a solution to the inherent inflexibility of non-ballasted track (NBT). NBT boasts lower maintenance needs and a longer lifespan compared to ballasted track, but its rigidity can create noise and vibration issues, particularly in urban areas. Historically, addressing those concerns often required expensive and disruptive modifications to the entire track system, company officials said.
The Common Interface provides a universal connection point for various fastening assemblies, allowing for quick and affordable adjustments to track performance without the need for extensive track modifications. Instead of replacing the entire track, rail infrastructure owners can swap out the fastening system to meet new performance requirements, company officials said.
Comprising two engineering plastic plates with retaining features, the Common Interface is compatible with all the main Pandrol fastening options. In a basic configuration, it accommodates a simple, medium-resilience fastening system.
As requirements for noise and vibration mitigation increase, the system can be upgraded to an intermediate configuration with more resilient components, and for extreme noise and vibration mitigation needs, the Common Interface can be upgraded to an advanced configuration to support even greater isolation of vibrations.
The system allowed for fine-tuning track resilience on Norway’s Follo Line to meet strict noise and vibration requirements, effectively controlling hotspots identified in a study, Pandrol officials said. The system is compatible with all NBT systems and ensures rail infrastructure owners can confidently adapt to changing performance needs for decades to come, they added.
Construction Polymer Technologies
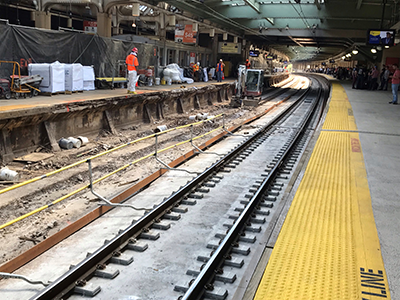
Construction Polymer Technologies is the North American licensee for the low-cost, easy-to-construct Sonneville LVT (Low Vibration Track) system, which is used on “many of the world’s premier transit systems,” company officials said.
The LVT system consists of a concrete block, a resilient block pad and a rubber boot surrounded by filling concrete. When properly installed, the system is “virtually maintenance free,” company officials said. The rubber boot separates the concrete block of the LVT support from the surrounding concrete, which reduces vibrations, provides electrical isolation and enables individual components to be replaced more quickly and easily.
LVT supports are available for all rail sections and special trackwork configurations. Construction Polymer Technologies offers LVT designs developed for wood tie-block replacement and for use in severe environments such as very sandy and very wet conditions.
Racine Railroad Products
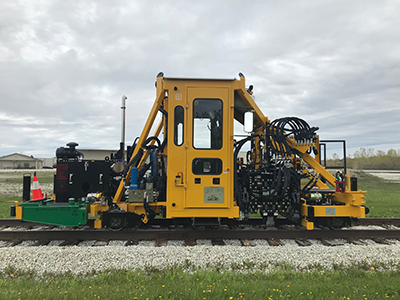
Racine Railroad Products offers equipment for adjusting, spreading and applying all types of modern-day rail anchors. It also manufactures equipment for applying and removing many styles of rail clips.
The company’s DAS anchor spreader and DAA anchor squeezer machines are built on a common chassis for more commonality of components. The company also offers a DASP machine that can either spread or squeeze anchors on both rails with either tie in plate spread or tie out methods on the same chassis.
Racine Railroad Products recently released the AM3 Anchor Applicator with touchscreen control technology designed to ensure faster workhead cycles and easier machine operation, company officials said. Adjustments for various rail sizes can be made right from the cab with no “wrench in hand” adjustments, and the machine will work with all modern-day anchor types from a 5.5-inch to 6-inch rail base.
Additionally, the company is an early pioneer of manufacturing ride-on equipment that can apply or retract “e,” Safelok and Fastclips on both rails and both sides of the rail (four clips) simultaneously, Racine Railroad Products officials said.
All the anchor and clip machines use touchscreens and electronic displays that replace analog gauges and switches for more reliability, as well as CMA valves and smart cylinders for programmable controls. All machines also rely on hydraulic smart-power distribution to efficiently divert power where needed and use less than 74-horsepower Tier IV engines that require no DEF or REGEN.
Michael Popke is a Madison, Wisconsin-based freelance writer. Email comments or questions to prograil@tradepress.com.