Stay updated on news, articles and information for the rail industry
November 2023
Rail News: MOW
For suppliers, innovations plus process solutions equal better welding equipment
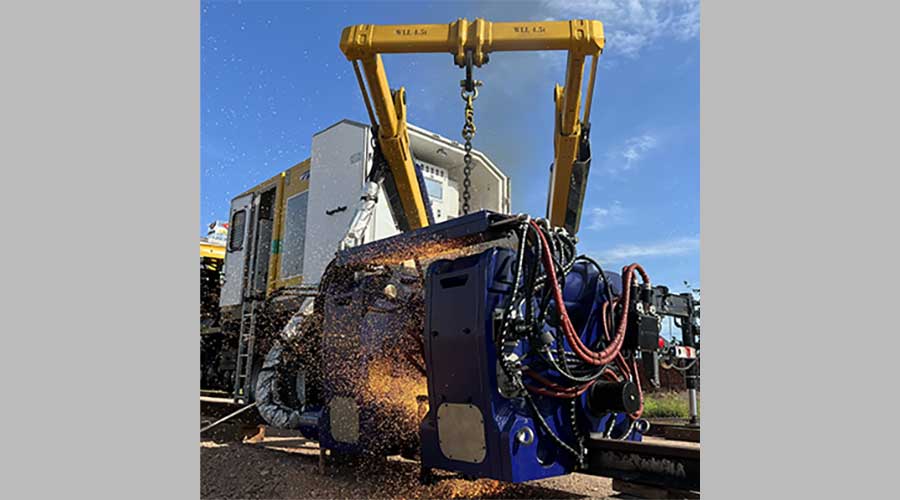
Compiled by Jeff Stagl, Managing Editor
Geismar North America
Since flash-butt welding was introduced to North American markets in 1968, the demand for it as a product and service has mandated constant improvements and advancements in technology and processes. To that end, Geismar North America continues to monitor rail industry demands to provide world-class solutions that meet industry partners’ ever-growing flash-butt welding needs, company officials said in an email.
Over the past two years, Geismar has developed four models of welders to meet those demands: the Flash Titan 600, 800, 1000 and 1200. Flash Titan 1200 is the latest version — a puller/welder combination designed to allow two processes to be completed with one piece of equipment, Geismar officials said.
The welder offers the ability to pull and weld with 1200 kN or 120 U.S. tons of force. It features an independent shear system and 5.9 usable inches of longitudinal stroke.
Geismar also is constantly working to meet industry demands by continually upgrading digital technology in the welding control system itself, such as faster processing speeds and predictive analytics that ensure safety, quality and reliability — the three key elements of welding, company officials said.
Geismar’s global presence and constant advancements in machinery, technology and process solutions help the company stand ready to meet customers’ current requirements and demands, they added.
Holland LP
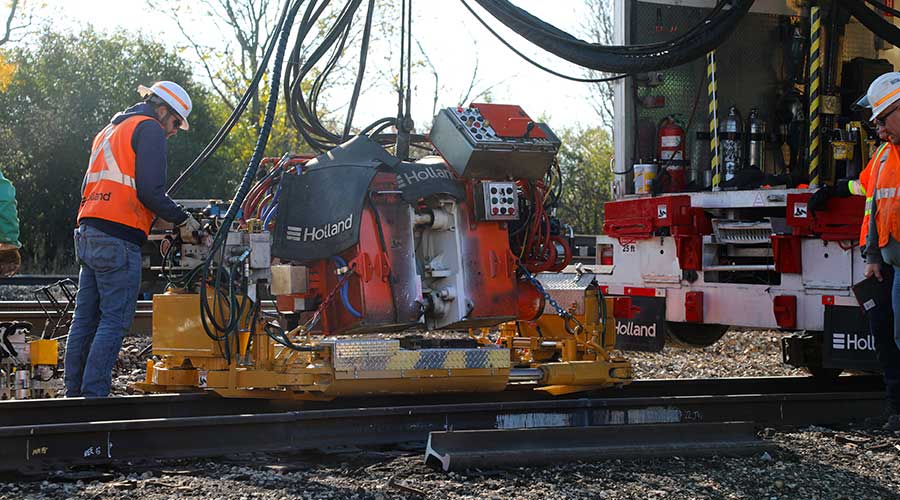
Holland LP is continually working to improve and adapt its core flash-butt welding business to the rail industry’s evolving needs. Efficiency, quality and sustainability are the key drivers of welding for today’s customers, Holland officials said.
The company’s newest innovation is Short Plug Repair Welding, a process designed to provide higher quality and more efficient defect remediation with a smaller footprint than traditional welding methods. Holland’s Short Plug Repair Welding gang uses five-foot plugs instead of a 20-foot plug, which eliminates waste and lessens the need to procure new rail, company officials said.
Moreover, due to the smaller plug size, rail that previously was scrapped can be recovered and used. Typical repairs take 60 to 75 minutes — the process’ four-person crew can match the efficiency of three thermite welding crews, Holland officials said. Ultimately, resources and crews then can be repurposed elsewhere, helping to boost productivity, they added.
The process also uses two pieces of equipment versus three, helping to reduce emissions and the overall carbon footprint of the maintenance work. A grapple truck that’s typically necessary for this type of work — and is the largest vehicle with the highest overall environmental impact — is eliminated, Holland officials said.
The company also continues to offer an Automated Manganese Refurbishment (HAMR®) service. It has excelled at providing higher quality and longer-lasting repairs to frogs and diamond inserts, company officials said. HAMR — which is two to three times faster than the manual process — uses robotically controlled welding procedures to build back damaged areas to restore the rail components, they added.
It helps increase efficiency and resiliency by using recycled material as an alternative for frequently hard-to-source special trackwork. The HAMR service prevents operators from working in close proximity to passing trains on adjacent tracks and being exposed to fumes for prolonged periods.
Pandrol
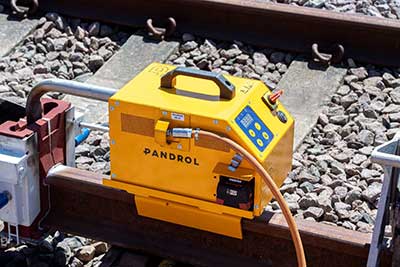
To perform a consistent weld, battery technology helps provide a safe, simple, repeatable and quality result every time.
To that end, the Pandrol High Flow Preheater is a battery-powered, fully automated and universal preheating system engineered for welding on site. It’s designed to replace the need for most existing equipment that’s currently used to raise the temperature of parent steel before welding.
The preheater’s ignition, timing and stop require no manual interference or flame adjustment. Unlike most existing preheating systems, it uses propane instead of oxygen, helping to reduce costs and make the equipment lighter and easier to carry around at a site, Pandrol officials said.
The preheater features only one propane hose to help minimize slips, trips and falls. It provides more consistent heating of the weld to eliminate failed welds from improper heating and preheating that’s performed the same each time with repeatable results, Pandrol officials said
The company also offers the Head Riser Removal Tool-Model HRT100 for the safe removal of the welded riser without the need of a hammer — the tool eliminates the need for hammering off the hot top of a weld, they said. The use of the HRT100 for the field weld process offers a safer method in day-to-day operations.
The handheld device can be used on any weld and weld shear for the safe removal process by the shear, Pandrol officials said. After shearing through a weld, the weld shear is retracted and the HRT100 is held in position for a secondary shear operation that clears the welded riser material safely off a weld.
RailWorks Corp.
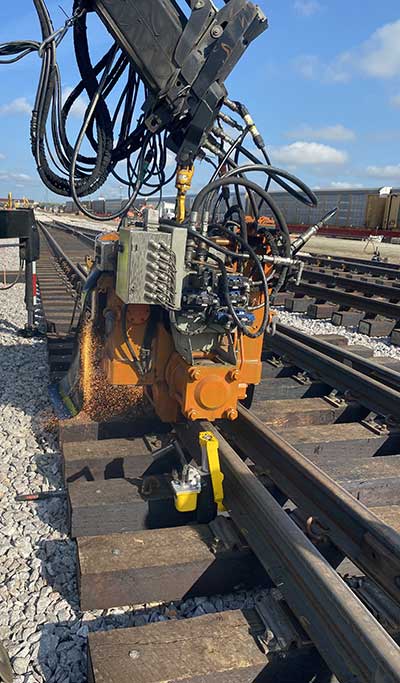
Along with its flash-butt original equipment manufacturer/supplier, RailWorks Corp. is constantly upgrading equipment to meet customers’ needs and changing rail chemistry, company officials said.
In 2023, RailWorks initiated an aggressive program to retire aging equipment and replace it with the latest technology. Part of that program aims to ensure remote monitoring capabilities and cloud-based data storage are available for customers on demand.
In recent years, the constant demand within the rail industry has been less track time, so RailWorks works closely with its customers to ensure the proper equipment is available with adequate manpower to take advantage of shorter work windows.
The company’s fleet operates at over 99% uptime. Therefore, customers have confidence in RailWorks when they get a short window to perform rail welding work, company officials said.
Over the past 10 years, flash-butt welding has become a staple in standard production gangs, such as rail and destressing work. A current trend noted by RailWorks: Customers are using more flash-butt welding in other work groups, including turnout programs.
Email questions or comments to jeff.stagl@tradepress.com.