Stay updated on news, articles and information for the rail industry
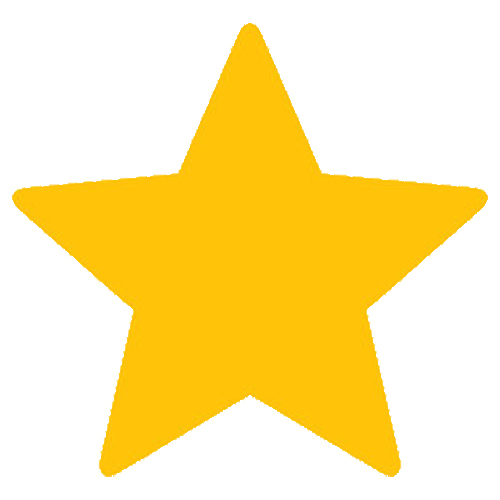
March 2007
Rail News: MOW
Hi-rail in high gear
By Jeff Stagl, Managing Editor
Frank Tartaglia Inc. custom-builds hi-rail trucks. Lately, that means equipping them with rail gear, large grapple units, magnets and, occasionally, remote-control devices.
“This equipment is necessary to round out a vehicle that will do it all — handle rail, ties and other track materials,” says Richard Barry, owner and general manager of the company, which since 1982 has supplied hi-rail equipment to the rail industry.
When it comes to meeting demands in every segment of the hi-rail marketplace — from light-duty trucks to rail gear to maintenance-of-way vehicles to track geometry systems — suppliers and distributors are giving their all to provide versatile equipment that’s reliable, easy to use and affordable. The pressure’s on railroads and rail contractors to keep up with track maintenance, so the heat’s on equipment providers to fulfill the industry’s hi-rail needs, providers say.
During the past year, K.W. Reese Co. officials have been busy filling orders because of increased demand. A hi-rail equipment provider the past 20 years, the company rents and sells vehicles to Class Is, short lines and Amtrak, but rail contractors are the firm’s primary customers.
“Railroads are outsourcing more maintenance work to contractors,” says Jeff Reese, vice president of K.W. Reese, which manages a fleet of 75 hi-rail vehicles.
And many contractors are searching for hi-rail equipment that’s harder to find than a rotary dump truck, such as a cement mixer or vacuum truck, he says.
Vehicle providers usually tap the used equipment market to help expand fleets, but railroads are holding onto trucks and rail gear longer than they have in the past, says Reese.
“We’re finding railroads are putting [used] rail gear onto another chassis,” he says.
Framing the issue
But railroads won’t find it easy to install older rail gear on new medium- or heavy-duty trucks’ chassis. This year, automakers are rolling out new diesel-engine truck models to comply with stricter U.S. Environmental Protection Agency air emission standards. The trucks feature redesigned frames to accommodate larger radiators, catalytic converters and exhaust systems — frames that pose a challenge for attaching rail gear, suppliers say.
“As the new truck models come out in the first and second quarter, we’ll have to do a little tweaking to make sure our rail gear fits,” says Nelson Carlson, VP of sales for Diversified Metal Fabricators Inc. (DMF), which supplies rail gear for light-, medium- and heavy-duty trucks. “We’ll make some changes to the mounting brackets and look at some adaptations of what we’ve done in the past.”
Automakers also are beginning to produce light-duty pickups with wider axles, so “we’ll need to make sure the tires line up with the rail,” says Carlson.
In addition, trucks no longer come equipped with integral front-frame extensions.
“There are fewer points to attach rail gear at the front of the truck,” says Carlson.
Harsco Track Technologies (HTT) also plans to make adjustments to its HY-RAIL® guide wheel attachments to comply with truck design changes.
“We’re waiting for the trucks to come off production lines,” says HTT HY-RAIL Manager Craig Sandsted. “As the automakers make final configuration changes, we don’t know if our mounting brackets will fit.”
Heavy-duty changes
The company’s already made its own product-line change. In May 2006, HTT introduced the HR4000 Series B1 HY-RAIL guide wheel attachment for heavy-duty chassis-cab trucks with single or tandem rear axles.
The rail gear has a smaller profile than HTT’s other heavy-duty model, says Sandsted, and offers dual control valves and positive safety pin locks for rail and highway position.
For the past two years, HTT also has marketed the HR3000 Series C2 for medium-duty chassis-cab trucks. The Series C2 is designed to minimize front unit overhang and place guide wheels close to the vehicle axle.
However, the company’s most popular models continue to be guide wheel attachments for light-duty trucks, says Sandsted.
Light-duty rail gear is a popular choice because railroad workers use light-duty trucks constantly to inspect track and make repairs, says Kevin Kyser, operations manager for Boatright Enterprises Inc., which markets rail gear to short lines, and provides rail-gear FRA inspection and repair services to all maintenance and inspection vehicles for railroads.
“Light-duty trucks are frequently used, so they accumulate more track miles, which wears out the rail gear more rapidly” than a medium- or heavy-duty truck, he says.
Another continuing trend: Railroads tend to prefer to electric over hydraulic rail gear instead of manual gear to make it easier for workers to operate the gear, says Kyser.
Workers carry a lot of equipment in their hi-rail vehicle, which oftentimes can overload the rail gear and make manual gear difficult to raise in the hi-rail position.
Because workers want to carry as much as they can on a hi-rail truck, more weight needs to be taken out of the rail gear, says Ralph Pollock, VP of sales and marketing for supplier G & B Specialties Inc.
“It’s an ongoing challenge,” he says. “If the rail gear is heavier, a railroad has to carry fewer people or less materials in a hi-rail truck.”
Sizing it up
In addition to producing lighter-weight rail gear, G & B Specialties is trying to offer a full light-, medium- and heavy-duty product line.
In November 2006, the company acquired ESSCO’s heavy-duty rail gear line to round out its products. G & B Specialties offered a heavy-duty model before the acquisition, but now can market a R-1100 Series that doesn’t protrude as much from under a truck, and “makes for a cleaner installation and is esthetically better looking,” says Pollock.
“We want to do away with bulky front rail gear,” he says. “We’re considering whether to use this design for medium-duty truck gear.”
The R-1100 Series is designed to speed up the rail-mounting process.
“It makes adjustments from side to side to get the guide wheels on track faster,” says Pollock. “The truck doesn’t have to be aligned perfectly to the track at a crossing.”
Brandt Road Rail Corp. also targeted a fast road-to-rail conversion for its recently introduced Brandt Rail Tool. The MOW machine features high-speed hydraulic rail gear and a turntable, and can convert to rail in less than one minute.
The Brandt Rail Tool is available with various attachments, including a grapple saw for brush cutting and a bucket magnet, and can be outfitted to move rail cars.
On the move
Brandt Road Rail also offers the rail gear-equipped Brandt Power Unit, a MOW machine that’s designed to move rail cars. Eighteen months ago, the company changed the power unit’s drive from two axles to three to boost tractive effort by 50 percent from 30,000 pounds to 45,000 pounds, says Sales and Marketing Manager Neil Marcotte.
To provide even more tractive effort, Brandt Road Rail last year introduced the Super Brandt Power Unit, a rail gear-equipped MOW machine and rail-car mover offering 65,000 pounds of tractive effort — enough to move 35 loaded freight cars.
“It has the tractive equivalent of a 1,000- or 1,500-horsepower locomotive,” says Marcotte.
The Super Brandt Power Unit is marketed more toward industrial customers, such as a grain terminal that wants the machine to move loaded cars, he says.
Meanwhile, Hytracker Manufacturing Ltd. officials are marketing the firm’s hi-rail MOW equipment to railroads as an alternative to mobile cranes. A 300-size excavator on a Hytracker end-load rail cart can handle a rail car for material loading or unloading, says Chuck Douglass, marketing manager for Hytracker, which offers hi-rail end- and side-load rail carts, and a low-bed rail equipment mover.
Cranes out, hi-rail carts in
Canadian National Railway Co. and Canadian Pacific Railway have retired older utility cranes and use excavators on rail carts to perform work formerly requiring cranes, such as unloading panelized turnouts, says Douglass.
“Excavators are not subject to being easily damaged, and require less capital investment and far fewer average hours of down time than a mobile crane,” he says.
At ImageMap Inc., officials continue to improve the Laserail® railroad infrastructure measurement system — which includes a hi-rail geometry system — to aid railroads’ MOW programs. The system offers a Global Positioning System feature to better locate rail defects, shock mounts to minimize rail-pounding effects and a more accurate digital rather than analog inertial package, says ImageMap Director of Sales and Marketing Robert Mullen.
“Railroads want more readings,” he says. “They can make better decisions with more data.”
Exploring the possibilities
Laserail also is designed to draw power from a battery and alternator rather than require a generator.
“We want to make it as compact as possible,” says Mullen.
Equipment suppliers and distributors are trying to ensure their products are as reliable and affordable as possible. For Frank Tartaglia’s Barry, customer service — such as fair pricing, realistic delivery times and standing behind your product — is key.
“If you give your customer your word that you’re supplying exactly what he requires and on his timeline, you better deliver,” he says. “It’s called reliability.”
Keywords
Browse articles on hi-rail high-rail hi-rail equipment high-rail equipmentContact Progressive Railroading editorial staff.