Stay updated on news, articles and information for the rail industry
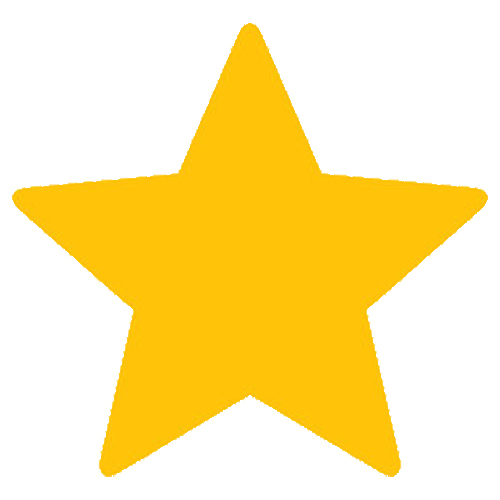
November 2009
Rail News: MOW
MOW Officials "In Their Own Words"
![]() Dave Freeman BNSF Railway Co. |
Dave Freeman is BNSF Railway Co.'s Vice President, Engineering. He is responsible for leading the construction and maintenance of BNSF's track, structures and signal systems. Before being named to his present post in May 2007, Freeman had served as BNSF's Regional Vice President, North Operations, since June 2006. Before being named to the North Operations post, he served as Assistant Vice President and Chief Engineer, South Engineering Operations, a position he was named to in 2004. Freeman began his career with BNSF in 2001 as Assistant Vice President, Fort Worth Service Region. He subsequently served as General Superintendent, Transportation, BNSF Network Operations Center in Fort Worth; and as Assistant Vice President, Intermodal and Automotive Operations. |
How much will your railroad ultimately spend on MOW this year, and how might that compare with your proposed 2010 Budget?
Our 2009 forecast for engineering capital spending is approximately $1.5 billion, with a focus on maintenance capital rather than expansion. BNSF's 2010 capital improvement plan will be in the same range, excluding spending associated with our positive train control (PTC) initiative, which is still under development.
From a rail, tie and ballast standpoint, we are continuing to invest in maintaining the reliability and efficiency of our infrastructure during the recession of the U.S. economy. For 2010, based on current forecasts, we are planning more than 3 million ties, 800 track miles of rail and an increased focus on ballast maintenance through additional undercutting, surfacing and shoulder-ballast cleaning.
With this proposed level of investment in our infrastructure, we will be positioned to provide even higher levels of service and infrastructure reliability to our customers once the economy begins to recover.
How has the employment marketplace changed during the past year or so? To what extent has it affected the way you recruit, retain or even outsource?
Obviously, with the overall condition of the U.S. economy, we have made several adjustments in our hiring plan for 2009 as well as for 2010. Our focus has been to keep current BNSF employees in a job, yet at the same time prepare our workforce for the start of the multi-year PTC initiative in 2010.
In 2009, in Engineering, we have been able to limit our MOW furloughs to the number we routinely have every year based on the seasonal nature of our capital work.
We scaled down both scheduled and exempt hiring in 2009. Prior to hiring from outside the company, we reached out to furloughed Transportation or Mechanical employees to place them in engineering positions as part of our hiring plan. We will continue this process for the 2010 work season.
As we went through the hiring process for attrition, we did not experience any difficulties in finding qualified applicants.
![]() John West CSX Transportation |
John West joined CSX Transportation predecessor railroad Baltimore & Ohio in 1979 as a trackman/welder. Over his 30-year career, he has served in a variety of positions in the company's engineering and information technology departments. Those positions range from Signal Maintainer to Director of Information Technology for then-CSX affiliate Sea-Land Corp. He was named President of CSX Technology in 2004, CSX Transportation Vice President-Maintenance of Way and Structures in 2007, and Vice President-Engineering earlier this year. |
How much will your railroad ultimately spend on MOW this year, and how might that compare with your proposed 2010 Budget?
Our goal is to ensure that CSX Transportation's (CSXT) track infrastructure supports current and future demand for rail services, and does so safely and reliably. CSX Corp. has maintained its 2009 capital investment at $1.6 billion. Decisions will be forthcoming on future investments but are expected to be in this range. Overall, engineering expenditures at CSXT (maintenance of way, bridges, communications and signals) have been responsible for about 60 percent of capital expenditures.
These investments are supporting new equipment and technologies to improve safety and efficiency. As one example, over the past year, engineering has installed "flange-bearing" crossing diamonds and turnout frogs at selected locations. These minimize the "speed bump" effect at track crossing points, reducing stress on rail segments, lowering maintenance costs, reducing noise and delivering a longer track life cycle.
More broadly, investments are also targeted on new capacity to support future increases in demand for rail freight transportation. Railroads are the most fuel efficient land-based mode of transportation, carrying a ton of freight 436 miles on a gallon of fuel. That fuel efficiency is galvanizing public policy around the desire for increased rail freight traffic.
The most notable capacity project is the National Gateway, a public-private partnership consisting of $840 million in projects that will result in the ability to move containerized freight in double-stack service between Mid-Atlantic ports and the Midwest. The majority of the National Gateway work will be focused on bridge and tunnel clearances, along with new intermodal terminals. Other work in 2009, which will continue into 2010, are network adjustments such as connection tracks to improve transportation efficiencies, and cooperation with customers on new track infrastructure to serve their facilities.
How has the employment marketplace changed during the past year or so? To what extent has it affected the way you recruit, retain or even outsource?
Overall hiring is down considerably in 2009 compared with 2008, reflecting the economic downturn. Along with fewer available jobs, most of the operations positions are filled internally from furloughed employees in other crafts, primarily train and engine- service and mechanical forces. Correspondingly, CSXT is doing less active recruiting at this time.
However, job losses in other industries have resulted in a much larger pool of available external talent when CSXT does post vacancies. The company is seeing people who have changed careers and therefore represent varied backgrounds and experiences. Candidates perceive the railroad as a stable, long-term employment opportunity.
As for the current engineering workforce, retention of maintenance-of-way and other employees has been enhanced through an intensive program of career advising that begins the day the employee reports for duty. In one-on-one sessions, new employees are counseled on career opportunities. These sessions are later complemented by career progression planning for those who choose to participate in ongoing skills training and interview preparation courses, as well as other advancement resources.
Consistent with normal attrition and what is widely expected to be a growing demand for rail freight, CSXT is poised to leverage the expanded pool of potential candidates. Recent surveys indicate that the company's branding campaign and national advertising have helped to raise awareness of not only rail's environmental benefits and economic contributions, but employment opportunities, too.
![]() T.J. Drake Norfolk Southern Railway |
T.J. Drake is Vice President Engineering for Norfolk Southern Railway. He began his railway career in 1976 as a management trainee at NS, where he served in various engineering capacities — from Tie Inspector to Division Engineer-Maintenance to Assistant Vice President MW&S — before being promoted to his current position. |
How much will your railroad ultimately spend on MOW this year, and how might that compare with your proposed 2010 Budget?
In 2009 at Norfolk Southern, the Engineering Department was able to maintain the original approved capital spending authority. In addition, the leadership at NS gave the department an additional 58 track miles of rail, and recently approved 160,000 additional ties. These additional authorities complemented improved production levels established by reduced traffic volumes and cooperative transportation efforts attained throughout the year. On the expense side of our budget, the focus was on cost control, where there was a lot of effort put forth by all Engineering Department employees working together to accomplish a reduction of nearly $100 million in expense spending while maintaining our safety effort, which stands among the leaders in the industry with a safety ratio less than 0.75.
At the time of this writing, the NS 2010 Capital and Expense Budget had not been finalized, yet the goal of the Engineering Department is to maintain reasonably close spending levels compared with 2009's total, in line with our 10-year Capital Plan and insistence upon maintaining a strong physical plant. Our Capital Category One Program — which includes rail (focusing on defect elimination), ties (focusing more on yard improvements), surfacing and roadway equipment (continual focus on rebuilding and replacing our aging fleet) — supports our position. We stand strong behind our continued signal and communication replacement programs, which include our continuation of Process Control System improvements. In addition, we ask for additional funding in our Capital Bridge Replacement and Bridge Tie Program. A significant amount of spending will also be added to the 2010 Capital Budget to initiate our PTC/OTC efforts.
The expense budget will strive to restore our maintenance service levels in rail grinding, rail testing, undercutting, bridge repair and other necessary services that were slightly reduced in 2009. We will finalize our fly mapping efforts to develop an Engineering GIS System. We will ramp up our hiring efforts to reinstate necessary employment levels to offset significant attrition in labor with the utmost importance placed on safety.
How has the employment marketplace changed during the past year or so? To what extent has it affected the way you recruit, retain or even outsource?
The economic downturn starting late in 2008 and continuing in 2009 had a big effect on our employment levels. We really ramped up our hiring effort in late 2008 to offset shortages in employment, and we were able to retain these newly hired employees by reducing expenses in other areas and absorbing new hires into our program gangs and other new construction projects. I believe we are hiring quality employees at all levels of the Engineering organization, somewhat different than the newly hired employees years ago. The majority of these new employees see their employment as a career, not just as a job. We see the opportunity to utilize our workforce and their abilities to perform work for others, in lieu of contractors, to install rail, ties and surfacing. With the present unemployment levels throughout the country, we should expect to be able to hire more motivated, conscientious and dedicated employees that we feel we can retain for the long term. I am very proud of the effort put forth by the officers and employees at the Norfolk Southern Engineering Department for maintaining a quality operation and the production levels while reducing expenses in line with corporate goals.
![]() David Connell Union Pacific Railroad |
David Connell is Vice President - Engineering for Union Pacific Railroad. He has worked for UP and predecessor companies for 26 years, having held a variety of field and staff positions, including AVP-Construction, Chief Engineer-Maintenance of Way and various track research positions. He currently directs the design, construction and maintenance of all track, signal and bridge infrastructure for UP. He currently chairs the Committee on Track Structure System Design of the Transportation Research Board and serves on several other research steering boards. |
How much will your railroad ultimately spend on MOW this year, and how might that compare with your proposed 2010 Budget?
At Union Pacific, we are planning another year of significant replacement and restoration capital spending to support our infrastructure needs. We are still developing our capital plan for 2010, but our spending level will be balanced between current low demand levels and our commitments to long-term strategic growth. In addition to surfacing and ballasting efforts, this includes supporting our tie program, as well as installing and undercutting track in our heavy-haul corridors.
We also will take on the additional capital burden for the development and installation of positive train control, the unfunded mandate resulting from the Rail Safety Improvement Act of 2008. We will aggressively pursue meeting the 2015 deadline.
How has the employment marketplace changed during the past year or so? To what extent has it affected the way you recruit, retain or even outsource?
Due to the global recession, overall hiring is down compared to recent years at Union Pacific. From an employment standpoint, the company is focused on sizing our organization to match existing business levels while continuing to improve our strong levels of customer satisfaction.
We peaked at 5,300 TE&Y employees on furlough in April/May, though that number was reduced to about 4,100 by the end of the third quarter. Rather than going outside the company for jobs such as track laborers, we have been successful in providing furloughed TE&Y employees opportunities to work in these positions. This has been appreciated by the train service furlough employees and, for the most part, they have worked out very well in their new roles.
Over the next several years, we expect retirements and business growth rates to create significant needs for people with civil, electrical and structural engineering degrees. The expected retirements could create rapid career advancement opportunities. We are focused on having the right training and talent development strategies in place to handle this knowledge transfer and employee development challenge. For example, our Operating Management Training Program provides a structured program and a mentor/coach for each individual, which prepares the trainee to move directly into a managerial position upon completion of the program.
Keywords
Browse articles on Dave Freeman BNSF John West CSX T.J. Drake Norfolk Southern David Connell Union PacificContact Progressive Railroading editorial staff.