Stay updated on news, articles and information for the rail industry
September 2023
Rail News: MOW
Primed to get track aligned: Surfacing and tamping equipment update
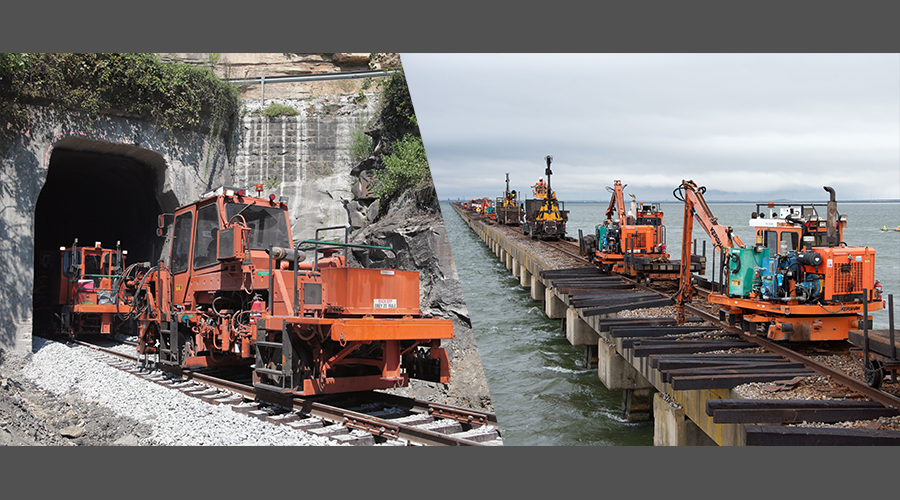
Compiled by Jeff Stagl, Managing Editor
Track condition is vital to both freight and passenger railroads. To ensure safety, reliability and/or rider comfort, tracks need to be in the correct geometrical position.
A train generates enormous forces when it travels over a track. Over time, such high stress can cause rails, ties and ballast to shift, deteriorate or return to their original position. If such anomalies occur, an ideal track geometry might be compromised and temporary speed restrictions might need to be enforced.
Therefore, railroads need to maintain track at regular intervals to retore geometry through leveling, lifting, lining, surfacing and tamping work.
For example, tamping efforts can repack ballast under ties to produce a stable tie bed and more compacted ballast bed, while surfacing work can raise, line and level track.
Equipment used to surface track includes on-track machines with machine operated and controlled tamping mechanisms, individual hand tools and unit tampers.
Equipment providers are striving to continually develop optimal surfacing and tamping machinery by incorporating more automation or upgrading features. In August, Progressive Railroading reached out to them via email to learn the latest about their equipment improvements, and how those efforts can help railroads better perform surfacing and tamping work.
Following are emailed responses from four equipment providers.
Ballast Tools Inc.
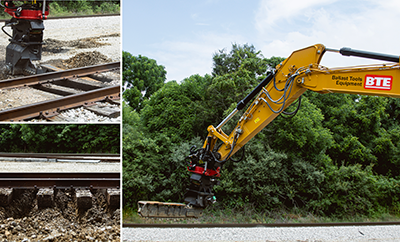
Mud spots and other fouled ballast defects that are not repaired promptly can lead to future track defects, potentially causing rapid deterioration of track components and compromising a track structure’s stability.
Traditionally, remediating these “FRA 213 defects” has required a crew of six-plus personnel using multiple machines, including an undercutter, dump truck, tamper and regulator. Ballast Tools Inc. (BTE) has pioneered a new approach to remediate FRA fouled ballast defects using a one-man crew equipped with a single BTE Hi-Rail Excavator and the new BTE CRIBBER, plus related work attachments, company officials said.
The CRIBBER attachment is derived from BTE’s trencher-style undercutter and features the company’s proprietary carbide-protected cutting chain that’s designed to withstand wear even in the toughest of conditions. Its continuous action allows for a faster, more efficient removal of ballast and debris, BTE officials said. The CRIBBER’s chain guarding protects against damage to the rails and ties while in use.
The introduction of the BTE CRIBBER now allows railroads to employ a single operator and a BTE Hi-Rail Excavator outfitted with a bucket, CRIBBER, dump cart and tamping attachment to completely remediate FRA-type fouled ballast defects with fewer workers and machines, and in less track time, company officials said.
With one operator and the hi-rail excavator equipped with BTE’s suite of attachments, railroads can clean mud spots and remediate fouled ballast defects in a fraction of the time and at a fraction of the cost, they added.
Harsco Rail
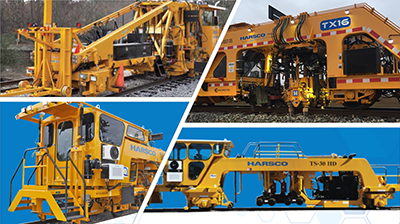
Railroads are demanding improved scheduling, high equipment utilization, equipment ease-of-use and digitization. Those demands not only combat declining maintenance windows and a transitional knowledge gap in the labor force, but support data-driven decisions and asset tracking, Harsco Rail officials said.
The company’s surfacing equipment portfolio — a suite of 16-tool tampers and stabilizers — is continually evolving to integrate new technologies and incorporate changes to ensure the machinery aligns with customers’ needs, they added.
A clear example of that strategy is the launch of the TX16 Production/Switch Tamper, which is a culmination of experience from an extensive tamper portfolio, global expertise and innovative solutions that resulted in a 16-tool tamper with unprecedented work-window utilization, company officials said.
The TX16 is designed to leverage tie-finding, non-contact measurement, hybrid indexing and cab push-button buggy deploy and stowage capabilities to reduce measurement, set-up tamping and stowage time. Those qualities help increase work within shrinking maintenance windows, Harsco officials said, adding that the same technologies can be implemented on many of the company’s other tampers.
The TX16 is engineered to safely speed up every aspect of a workday. Cab deployable/stowable reference, integrated high-speed measurement, automated tamping and hybrid index, combine to significantly increase overall productivity, company officials said.
The TX16 leverages Harsco Rail’s multigenerational product, technology and service experience, such as the Jupiter Control, Callisto Protamp and Mobile Asset Recording System, they said. The technologies can be added to the MK4, 6700 or MK6 tamper.
Plasser American
Today’s rail maintenance industry has a need for higher performance, increased efficiency and autonomous solutions to meet current demands. To that end, Plasser American is working on an ongoing implementation project aimed at helping to bring more automation to the industry, company officials said.
One such element of that work is the development of a smart tamping machine that would support the tamping operator with managing the machine’s operational system up to a full automation of the entire process, they added. The effort includes scanners, camera(s) and sensors that will drive information to the Convolutional Neural Network (CNN) to train the track maintenance machine to analyze the field to identify obstacles, turnout parts and tamping plans, and to calculate suggested operator actions. The suggested actions are delivered to the operator’s screen.
Plasser’s PTS90C remote stabilizer upgrade is an additional contribution to introduce more automation in the industry, company officials said. In fourth-quarter 2022, Plasser introduced an upgrade kit that allows the PTS90C to follow any lead vehicle — such as the GRM3000T — to guarantee a sustainable track geometry without the need for an additional operator, company officials said.
The machine applies controlled, accurate stabilizing forces into the track structure at speeds of up to 1.2 mph. Due to homogeneous compaction, the PTS90C cuts costs, leads to longer maintenance intervals and reduces slow orders after out-of-face track maintenance work, Plasser officials said.
The autonomous stabilizer keeps headcount low and performance high, while radar safety solutions ensure the safe operation on track, they added.
RCE Equipment Solutions
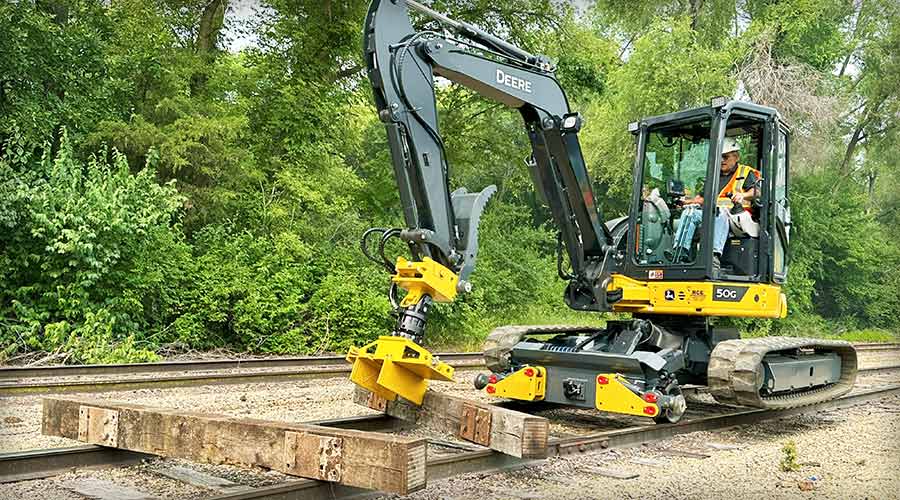
The Railavator hi-rail excavator is RCE Equipment Solutions' most popular machine because of its quality and versatility, company officials said. The excavator — which can be equipped with tamper heads — features a patented hydraulic-powered, retractable hi rail so it can travel anywhere on or off track.
The New Series 210P, 245P and 250P Railavators are equipped with RCE’s new Ultra Life Axles. The drives are made of high-strength alloy steel that’s two times more structurally strong than existing cast-iron final drives, company officials said.
Many rail maintenance operations require severe duty applications with high point loading. The Ultra Life Axles offer overall increased axle bearing capacity and are rebuildable and repairable, RCE officials said.
The New Series Railavators come with many design enhancements, including a new hydraulic system. There are more components in the common manifold, which means fewer hoses, separate components and joints to potentially leak, company officials said.
The F-N-R valves now are pilot-operated instead of electrical coils to provide a more reliable design. RCE also updated the Railavator structure, including the hi-rail linkages and supports, by extending support gussets and adding weight to the links and frames. The modifications reduce frame flexing and potential cracking, company officials said.
In addition, the drive axle mounting has been changed to provide more strength and durability, and the axle mount and front/rear bumpers and tow points have been redesigned. The improved rotary manifold offers a higher pressure rating and longer life, while the push-button monitor controls the hi rail and all available attachments from inside the cab, company officials said.
Email questions or comments to jeff.stagl@tradepress.com.