Stay updated on news, articles and information for the rail industry
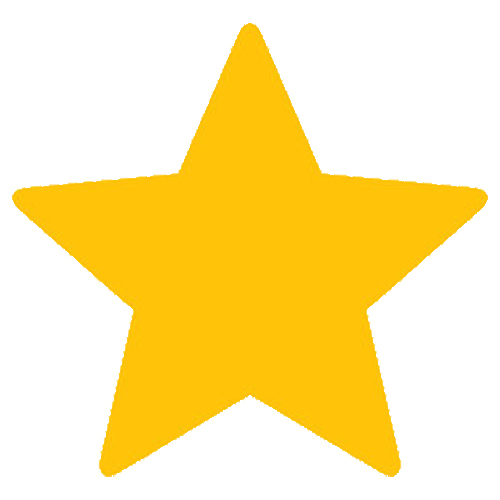
June 2016
Rail News: MOW
Product roundup: Ballast management 2016 (part 1)
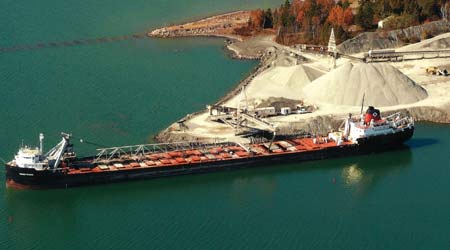
— Compiled by Pat Foran, editor
For more than a century, railroads have used crushed stone (i.e., ballast) to keep ties in place and solidify the track foundation. Railroads also spread tons of the stuff annually to replace fouled ballast, even out roadbeds and ensure proper drainage.
Although railroads’ maintenance-of-way (MOW) spending is down some this year, Class Is, regionals and short lines still have plenty of ballast-related work on their agendas, as witnessed by Progressive Railroading’s 2016 MOW Spending Report, which was published in the April issue.
Among the Class I crowd, BNSF Railway Co. plans to install 5.3 million net tons of ballast this year; CSX, 2.7 million tons; Norfolk Southern Railway, 2.4 million tons; CN, 1.2 million tons; and Canadian Pacific, about 240,000 tons.
In terms of regionals’ and short lines’ ballast-installation estimates for 2016, the report showed Riverport Railroad LLC is targeting 120,000 tons; Vermont Rail System, 75,000 tons; New York, Susquehanna and Western Railway Corp., 60,000 net tons; Indiana Harbor Belt Railroad Co., 52,600 tons; Finger Lakes Railway Corp., 25,000 tons; Alaska Railroad Corp., Indiana Rail Road Co. and Iowa Northern Railway Co., 20,000 tons each; Arkansas & Missouri Railroad, 15,000 tons; Central Maine & Quebec Railway, 14,000 tons; and Reading, Blue Mountain & Northern Railroad Co., 12,000 tons. Numerous other small roads are projecting between 25 and 8,000 tons.
To get all that rock laid properly and efficiently (i.e., keeping service interruptions to an absolute minimum), railroad MOW managers will be relying heavily on suppliers and service providers that offer cutting-edge ballast equipment and related technology — from automated conveyor trains and distribution systems to ballast cleaners and an array of system options.
Who’s offering what these days? Part one of Progressive Railroading’s annual ballast product/service roundup aims to provide some answers.
For this segment, information is provided by eight suppliers and service providers in the ballast realm: Georgetown Rail Equipment Co., Herzog Railroad Services Inc., Loram Maintenance of Way Inc., Miner Enterprises, Ontario Trap Rock, Plasser American Corp., Progress Rail Services Corp.’s Maintenance-of-Way Division and Rail Construction Equipment Co.
Note: Part two of the ballast management product/service roundup will appear in the September issue.
Georgetown Rail Equipment Co.
For situations where traditional ballast delivery methods aren’t sufficient, Georgetown Rail Equipment Co. (GREX) offers the DumpTrain® and the company’s newest development, the DumpTrain for Curves™.
A “railroading mainstay’ for more than 20 years, the DumpTrain provides pinpoint ballast placement of up to 2,000 tons of aggregate in as little as one hour, the company says. A 50-foot boom that can travel 180 degrees perpendicular to the track enables the DumpTrain to deliver aggregate to difficult-to-reach places.
When ballast is needed in areas of significant track curvature, GREX offers the next-generation DumpTrain for Curves. Each car has its own belt and drive motor: When unloading, each delivers material to the preceding car until the material arrives at the stacker. This new design also provides users the flexibility of creating custom-sized trains that can be adapted to fit individual projects, the company says.
While some customers may desire long consists for projects that require large amounts of material, others may prefer shorter consists that can more easily maneuver in situations where track conditions are limited due to a derailment or washout.
The DumpTrain for Curves prototype has been used extensively on “two high-profile” capacity expansion projects in which the train was employed to surface newly constructed track, the company says, adding that the prototype’s efficiency and reliability allowed customers to maintain “aggressive build schedules.”
Herzog Railroad Services Inc.
The Herzog Automated Conveyor Train’s (A.C.T.) entire consist (15 cars minimum) can unload in a curve of up to 13 degrees with a super elevation of up to five inches. The machine also meets “plate C” specifications. Each car within the consist can carry 97 tons of material up to five inches in diameter and as small as a particle of sand, the company says. It takes about three minutes to unload a car, and the material is distributed as far out as 50 feet from the track center — without fouling adjacent tracks.
The Herzog patented automation also enables operators to select individual cars for unloading, which enables the machine to carry and unload multiple materials within the same consist. The A.C.T. also features an automated plow at the front of the discharge car that can be seen from the operator’s cab with the aid of two strategically placed cameras. This enables the operator to distribute material in front of the machine and safely plow it off without having to push a tie along in front of the machine.
The stacker car also features a positive lock system for the discharge conveyor, enabling the operator to lock the conveyor to the side that is being unloaded and eliminating the opportunity to swing back to the opposite side without manually removing the lock.
Loram Maintenance of Way Inc.
The Loram SBC 2400 offers cab forward design with the ability to process more material within a shorter track window, enabling customers to reduce unit cost and cover more of their system with 2,400 cubic meters per hour output and an operational speed of up to 4 mph, the company says.
The Loram SBC 2400 also includes “enhanced” machine automation, which increases productivity and improves consistency in quality of product — the automation enables operators to spend more time on attaining a quality product and less time making manual adjustments as changing conditions warrant, the company says.
Meanwhile, a monitoring system is designed to prevent conveyor belt overloads from occurring — another way the SBC 2400 can help maximize productivity, company officials believe.
Miner Enterprises Inc.
Miner Enterprises Inc. offers safe, durable and maintenance-free ballast systems that can be applied to new or existing cars.
The AggreGate can effectively ballast inside, outside or both sides of the rail simultaneously. Features include large guillotine door openings designed to stop ballast flow with minimum effort; easy to operate toggle-type linkage systems; and tapered doors for easy ballast shutoff at switches, crossovers and bridges, the company says.
The remote control AggreGate also enables users to deposit ballast while remaining a safe distance from the activity.
AggreGate ballast discharge outlets are available in manual, air-operated, electric and remote control models to meet a variety of unloading needs. Engineered as a fabricated and completely assembled unit, AggreGates are easy to apply to new or existing hopper cars.
To help car builders and car shops streamline the applications and reduce labor costs — they’d been asking for a “safe, durable, maintenance-free way to ballast that can be applied to new or existing cars,” Miner says — the company has simplified the application of the AggreGate systems.
Miner also has improved the internal electronics of all of its AggreGate systems, including the Stand Alone system.
The Stand Alone Electric AggreGate enables independent operation of the car from anywhere within a ballast train, eliminating the need for grouping manual and automatic cars.
Miner AggreGate is available in pry bar manual, push button or remote control operations using pneumatic or electric power to operate the gates.
Ontario Trap Rock
A division of R.W. Tomlinson Ltd., Ontario Trap Rock is a specialty aggregate quarry located near Sault Ste. Marie, Ontario.
The 1,000-acre site contains more than 80 million tons of aggregate known as Diabase. Commonly referred to as “trap rock,” the aggregate is a “very hard, durable material with physical properties far exceeding the most stringent railroad specifications,” the company says, adding that its trap rock is used throughout the Great Lakes region by Class Is, regionals and short lines.
“This product is depended on for superior thermal and acoustic properties in rock wool insulation, [and is] relied on for strength in specialty concrete applications and trusted by the railroad industry for resistance to deterioration in rail ballast,” the company says. In addition, companies in the hot-mix paving industry use Ontario Trap Rock’s products to produce skid-resistant, durable road surfaces.
Railroad ballast is now shipped to docks located in Ashtabula and Toledo, Ohio; Chicago; Detroit; Erie, Pa.; and Sarnia, Ontario.
Plasser American Corp.
Only with sufficient ballast available can track can be correctly maintained and adequately tamped. Accordingly, Plasser American Corp. developed the BDS-100 and BDS-200 Ballast Distribution system to help customers restore the proper ballast profile. With their long reach, the shoulder plows are capable of retrieving ballast that is out of the reach of conventional ballast regulators; the pickup ballast broom loads excess ballast that can unload where needed.
The system consists of two independent units that also can work together as one machine. The BDS-100 is equipped with a hopper for ballast storage, four conveyors for ballast distribution, and Plasser’s shoulder and X-type plows for ballast profiling. The BDS-200 is equipped with two ballast brooms: The “pick-up” broom that sweeps the excess ballast from the track onto a conveyor, which loads the ballast into the BDS‑100 or into a Plasser MFS-type Conveyor and Hopper Car; and the “finishing” broom that provides the final track dressing.
The ballast handling capacity of the Plasser Ballast Distribution System can be increased by coupling Plasser MFS-type conveyor and hopper cars between the two units. All work is performed in a “one pass” operation.
The BDS-100/200 Ballast Distribution System can accompany the high-speed 09-3X tampers for final track dressing or work as an independent machine to distribute ballast. When working as an independent machine, it may be used to pick up excess ballast from the track shoulders for distribution as needed at any location, including switches.
Progress Rail Services Corp.
For more than 70 years, Progress Rail Services Corp.’s Maintenance-of-Way (MOW) Division has produced equipment designed to improve and maintain Class Is, short lines and passenger railroads around the globe.
In 1945, Progress Rail’s MOW division introduced the first Ballast Regulator under the Kershaw name. Since then, the company has enhanced it and offers three Kershaw Ballast Regulator models engineered for safety, speed, power, efficiency and performance, including the Kershaw 4600, Kershaw 46-2 and Kershaw 46-6 Ballast Regulator models. Now, all the company’s Ballast Regulator models are fitted with new high-performance, carbide-faced premium wear parts on wings and plows, extending the interval between replacements and reducing total operating costs, the company says.
The Kershaw 4600 Ballast Regulator has a one-pass transfer plow, 36-inch wide reversible wings and a broom attachment for ballast shaping, shoulder profiling, ballast sweeping and a variety of other track maintenance operations. The Kershaw 4600 comes equipped with a Cat® C7 engine, rated at 250 horsepower for reliable performance.
Rail Construction Equipment Co.
In 2015, Rail Construction Equipment Co. (RCE) focused on expanding the Railavator product line to feature smaller and larger models. Railavators can be used in many maintenance applications, including undercutting, pulling rail, cutting brush, craning, tamping ties, digging and trenching.
Part of the expansion effort included developing more under cutter bar sizes to enhance the use of the excavator undercutting process. Now, RCE can supply the 75G, 85G, 135G, 245G, 250G and 350G excavators with undercutter bars ranging from 9 feet to 15 feet.
By increasing these options, RCE customers can perform undercutting with all RCE hi-rail or standard excavator models. The largest machine — the 350G — offers more hydraulic power to perform in harsh conditions while the longer bar is beneficial for switch undercutting.
“We have received requests from railroads for greater versatility for switch undercutting, which has resulted in RCE developing the larger machine and undercutter bar,” says Sales Manager Dennis Hanke.
Email comments or questions to pat.foran@tradepress.com.