Stay updated on news, articles and information for the rail industry
December 2019
Rail News: MOW
Product update: Friction modifiers and rail lubrication systems
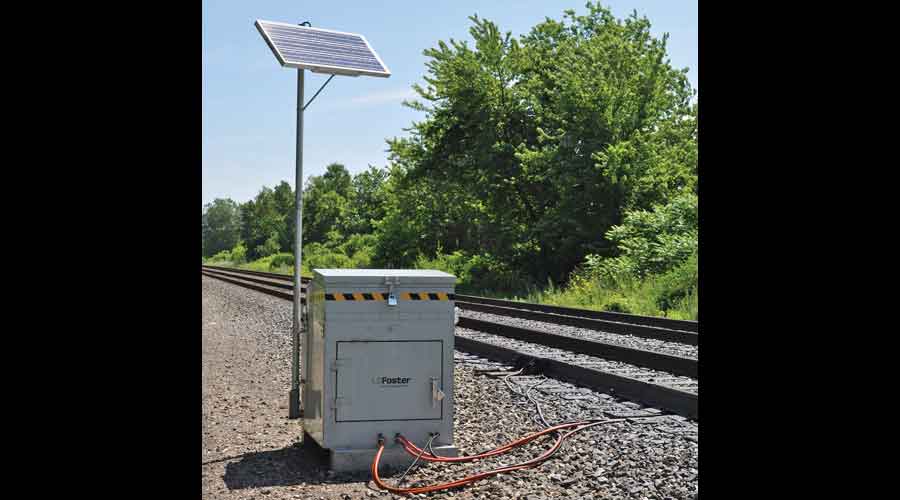
—Compiled by Michael Popke
L.B. Foster Co.
L.B. Foster Co.’s newest wayside unit, PROTECTOR® X, has been “redesigned to mitigate grease cavitation, as well as extending the refilling interval,” said General Manager-North America John Cotter in an email.
The company also plans to roll out a new web-accessible remote system monitoring platform, RPM 2.0 powered by Anatomy, which is designed to provide improved analytics and reporting “essential to mitigating program downtime,” Cotter said.
And with a Class I, L.B. Foster is wrapping up an assessment of an all-season, rail-curve gauge face grease that “allows for application at 50 percent of a typical application rate,” Cotter said, adding that the new grease has shown to be less prone to bar clogging.
Loram Maintenance of Way Inc.
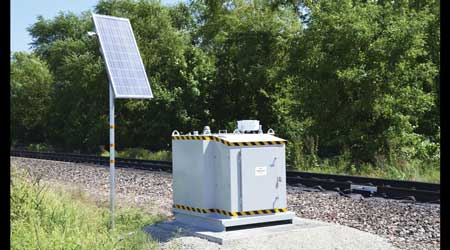
For Loram Maintenance of Way Inc., the technology and expertise gained from the recent acquisitions of GREX, SENSR and HyGround has “driven a broader understanding of factors relating to rail life,” company officials said in an email.
By combining tie expertise from GREX, sensors and monitoring technology from SENSR, and subgrade and ballast knowledge from HyGround, Loram provides “opportunities to evaluate and develop friction management solutions from an entirely new perspective,” officials said.
Loram is “the only North American company with extensive data history on rail grinding and friction management that can straddle both sides of the ‘Rail Life Extension’ solutions,” they said. The company’s friction management division has more than 60 years of experience in studying rail performance with accumulated data and expertise from top-of-rail to ballast subgrade.
TRAC Lubricants & Coatings
TRAC Lubricants & Coatings provides a variety of friction management products. Using aerospace technology, the company utilizes solid film lubricants to lower the coefficient of friction to a level that reduces noise, as well as wear on rails and wheels, company officials said in an email.
The molybdenum disulfide BLACK ICE™ is a wet liquid that dries quickly to a dry lubricant. The product either is brushed or sprayed on to the rail or wheel whenever friction becomes too high. The dry film lubricant allows for infrequent applications, and BLACK ICE burnishes into the rail — eliminating daily or weekly application, company officials said.
TLC also offers traditional greases, including a biodegradable version for wayside lubricators.
Railmark Track Works
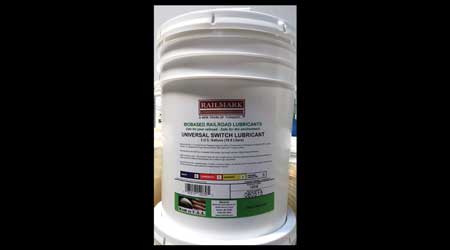
Railmark Track Works Inc. offers its ECORail™ branded line of bio-based switch and rail lubricants, with lubricity that results in less friction — and translates to less heat and less wear, company officials said in an email. Lubricants include universal switch lubricants, frigid climate switch lubricants, top-of-rail friction modifiers, ISO 32 and ISO 46 hydraulic oils, and universal tractor hydraulic fluids.
The company’s lubricants meet both the U.S. EPA’s Environmental Preferable Purchasing criteria and is a USDA “BioPreferred™” product. Manufactured in the United States from renewable U.S.-grown crop-based oils with a lithium-based thickener, Railmark’s lubricants are safe for the environment while supporting American farmers, officials said.
The lubricants also have a high viscosity index; the base oils’ viscosity indices are two times higher than equivalent viscosity petroleum-based oils, providing more stable viscosity at different temperatures and a wider range of operation, according to the company.
RBL Inc./Robolube
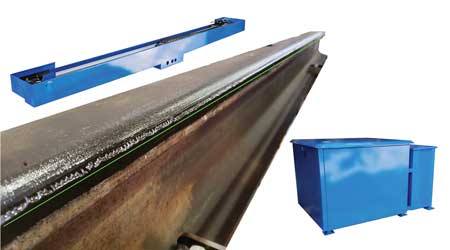
In addition to offering its Hyrail track lubrication units, RBL Inc./Robolube introduced Robolube 2000, a gauge face lubrication product, at Railway Interchange 2019 in September.
Based on results from year-long testing at the Transportation Technology Center Inc.’s Facility for Accelerated Service Testing, the company has improved the product, officials said in an email. The Robolube 2000 utilizes 75 percent less lubricant than similar products, and lubricates eight feet of track for the circumference of the wheel so trains can efficiently consume grease, they said. It mounts in the apex of the curve for bi-directional traffic, provides no train contact, decreases maintenance and includes a fully heated grease system for continued operation in cold-weather environments.
Additionally, a web-based user interface provides status updates, remote notifications and real-time diagnostics.
Deliveries are projected to begin during first-quarter 2020.
Whitmore Rail
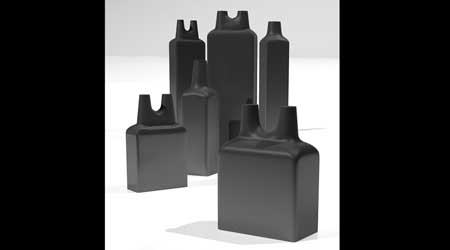
Whitmore Rail recently introduced the Whitmore® TSFM - Tread Stick Friction Modifier, and the Whitmore® FSL - Flange Stick Lubricant.
During normal rolling, the TSFM - Tread Stick Friction Modifier acts as a lubricant. When wheel creep occurs, the sliding friction immediately converts to “positive friction” — reaching a friction level of about 0.18 to 0.42 between the wheel tread and top of rail, company officials said in an email. This controls the creep condition and returns the wheels to a healthy rolling motion. The result: a substantial reduction in creep forces, which reduces corrugations and high-frequency squealing, officials said.
During normal rolling, the FSL - Flange Stick Lubricant transfers from the wheel flange to the gauge face/corner and lubricates both surfaces, reducing the coefficient of friction to as low as 0.10. The result: “a substantial reduction” in wear on the gauge face, gauge corner and the wheel flange, officials said.
Whitmore Rail also offers rail curve and switch plate lubricants such as RailArmor® and BioSwitch™, which reduce wheel flange and rail wear, extend rail and wheel life; and decrease fuel consumption and wheel squeal. The company’s friction modifier, TOR Armor®, reduces noise, wear and lateral forces, officials said.
Michael Popke is a Madison, Wisconsin-based freelance writer. Email comments or questions to prograil@tradepress.com.