Stay updated on news, articles and information for the rail industry
August 2017
Rail News: MOW
Product update: Material handling equipment 2017
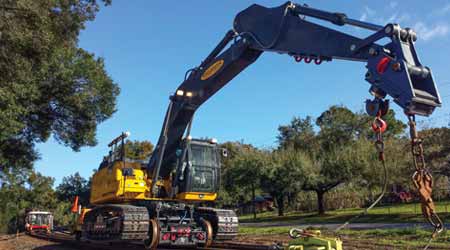
As work windows narrow, maintenance-of-way (MOW) managers continue to try to find ways to improve work practices. They also continue to seek equipment — including machines that handle and distribute such materials as rail, ties and ballast — that’ll help them minimize the time crews spend on the track.
What’s new in the material handling equipment realm? What are railroads looking for to help them safely and efficiently excavate soil, transport and unload rail or ballast, or haul materials to and from a derailment site?
For answers, Progressive Railroading recently reached out to a cross-section of material handling equipment suppliers. Emailed responses from nine companies follow.
Georgetown Rail Equipment Co.
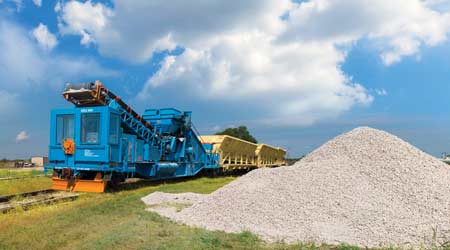
Georgetown Rail Equipment Co. (GREX) offers the DumpTrain®, which allows a single employee to efficiently and safely unload up to 2,000 tons of aggregate per hour without requiring railroad employees on the ground. The DumpTrain enables the operator to sort through various types of ballast in a single delivery, which provides customers the freedom to deploy multiple types of ballast in any project, the company says.
GREX recently expanded its DumpTrain technology with the introduction of the DumpTrain for Curves™. In addition to offering the same characteristics of the original DumpTrain, DumpTrain for Curves allows operators to unload ballast in up to a 27-degree curvature and permits customers to create custom-sized DumpTrains to suit the specific needs of their individual projects. As a result, customers can extend the efficiency and effectiveness of their ballast by utilizing GREX’s technology on portions of track that historically haven’t been easy to access, the company says.
Herzog Railroad Services Inc.
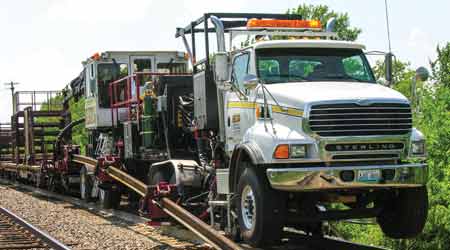
The Rail Unloading Machine from Herzog Railroad Services — also known as “RUM” — puts the emphasis on safe and efficient single- and dual-sided rail unloading.
Completely self-contained, the RUM moves under its own power between job sites and sets on at 40-foot road crossings; it sets up in about 20 minutes, company officials say. The unit is compatible with most rail trains (although minor modifications to tunnel cars might be required), and no winch car is necessary.
The RUM unloads an average of 12 to 16 rails per hour and is flexible enough to meet a variety of unloading requirements, according to Herzog. The production rate also can be increased when the RUM is used in conjunction with the Herzog automated tie-down car.
Additionally, the unit eliminates the need to fishplate and tie off rails when unloading — increasing productivity while significantly reducing manpower, and allowing MOW crews to focus on other projects, the company says.
Loram Maintenance of Way Inc.
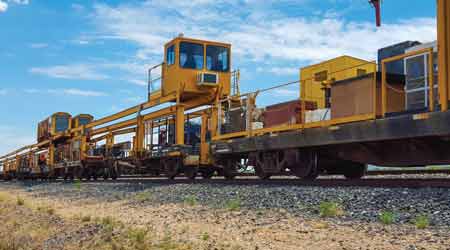
Loram Maintenance of Way Inc.’s Raptor is designed to outperform traditional rail-handling systems with double the production of 3,000 feet per hour, the company says. The Raptor rail-handling system provides a better solution for the entire process of rail relay, as opposed to a system focused solely on rail delivery, company officials believe. The system also lowers injury risk by reducing the human interaction and retaining complete control of the rail while loading and unloading.
The Raptor’s modular design allows for easy adaptation to machines that provide services in any of the four areas of the rail logistics cycle: transport of rail to welding plant, delivery of continuous-welded rail from plant to trackside, pick-up of relay rail for reuse or re-welding, and pick-up and disposing of scrap rail.
Meanwhile, the unit’s versatile design features anticipate future changes in rail size and long rail delivery needs, the company says.
Plasser American Corp.
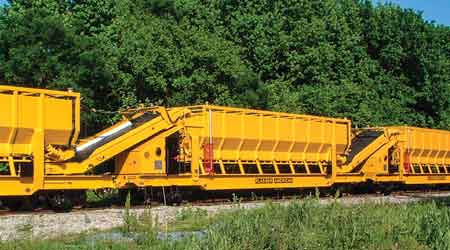
Plasser American Corp. offers conveyor and hopper cars designed to transport ballast, spoils or other material to and from various work sites. The advantage of the company’s MFS units, according to Plasser officials, are their ability to transport, store, load and unload material as a single unit, or in tandem with similar units.
MFS cars are available in various sizes to meet loading needs and clearance requirements and restrictions, and material storage capacity can be increased by coupling multiple units together.
Additionally, MFS cars can be coupled directly to ballast undercutter cleaners or shoulder cleaners, and waste material is loaded directly from the ballast-cleaning machine.
When multiple units are coupled together, half of them may be towed away (when loaded) by a locomotive or power unit for unloading, while the ballast-cleaning machine continues working uninterrupted to load the remaining cars.
The MFS also can be used in conjunction with Plasser’s distribution, loading and unloading systems for cost-effective ballast management, the company says. Each MFS car is individually powered with its own engine, hydraulic supply and electrical system.
Railquip Inc.
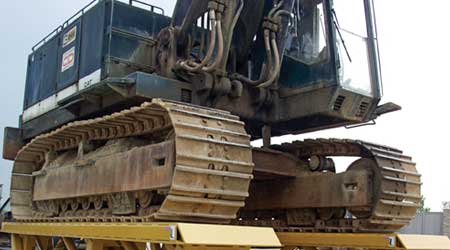
Railquip Inc. says its RQSL-8000 is the first “extreme duty” lifting system specifically designed to lift and safely support vehicles and equipment weighing up to 100 tons. Designed for the military, the lifting system is an “ideal addition” to maintenance facilities servicing large tracked or heavy armored vehicles, company officials add.
With a lifting height of 39.5 inches, the vehicle undercarriage is accessible for inspection and maintenance.
The hydraulic power unit is driven by a 20-horsepower gasoline engine with electric start.
With no reliance on facility power, the entire lift system is designed to be disassembled and deployed for field maintenance operations. All that is required is a concrete support pad, according to the company.
The unit’s safety features include 12 lifting cylinders with pilot check valves, six double mechanical lock rack assemblies to back up the hydraulic system, high-tensile strength steel, a 25-foot pendant operated by remote control and a heavy-duty four-piece ramp connection system with safety pins.
Pettibone/Traverse Lift LLC
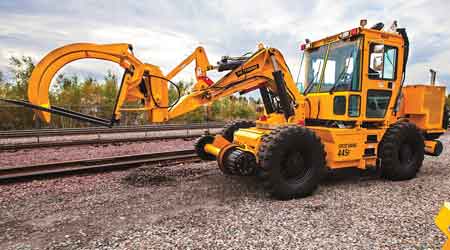
Pettibone/Traverse Lift LLC offers the Speed Swing 445F. Designed for multiple railroad service applications, the unit offers “precise hydraulic engineering and ample power” to lay rails, set ties and perform other tasks, the company says.
Powered by a 163-horsepower Cummins QSB4.5 Tier 4 diesel engine that offers fuel savings up to 10 percent over the previous model, the Speed Swing 445F features a Dana T20000 three-speed transmission with twist grip electric shift control. The machine has a front load capacity of 10,000 pounds and side load capacity up to 8,000 pounds.
Operators can move the Speed Swing 445F between job sites quickly, traveling at 25 mph on hi-rail and 20 mph with all-terrain rubber tires. The unit also can be built to meet customer specifications, the company says. Common options and attachments include a tote boom, hydraulic tool circuit, magnet package, AAR coupler, track cleaning bucket, load bucket, 20-foot extendable boom, fork frame, backhoe, brush cutter and snow plow.
Custom Truck & Equipment
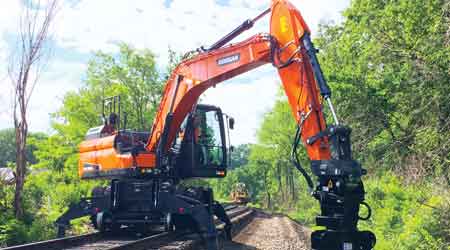
Custom Truck & Equipment supplies a range of trucks to the rail industry, including high-rail pickups, elliptical dump-body trucks and tandem axle material handlers.
The company’s Doosan DX190W-5 wheeled excavator with railgear features a 173.5-horsepower diesel engine and travels up to 21.75 mph. It accepts a variety of railroad MOW attachments, including a 10-foot undercutter bar with a 6-foot chain width, automatic chain adjustment, 360-degree rotation capability and a hydraulic tilt bar.
The heavy-duty railgear has a capacity of 70,000 pounds per axle and 16-inch-diameter steel wheels, and it is designed to handle the rigors of excavation work.
Omaha Track Equipment
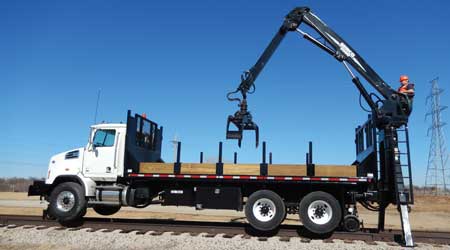
Omaha Track Equipment engineers and “upfits” material handling (or grapple) trucks, which load and unload rail, ties and other track materials. The trucks typically are furnished with a grapple, magnet system and creep drive system that enable the operator to drive the truck on rail from the upper crane operator seat. A pintle hitch allows for the towing of equipment trailers and material carts.
The company also manufactures heavy-duty material carts for hauling rail and ties on track. Optional cart features include clam-bucket attachments, hydraulic tool circuits and knuckles with train air for moving rail cars.
The newly designed, custom heavy-duty high-rail carts are lighter in weight with higher capacities than Omaha Track Equipment’s previous carts, and they can be hauled to and from work sites using a material handling truck with a minimum 20-foot bed, the company says. Carts are placed on the track with an on-board crane and can hold up to 100,000 pounds each — an industry first, according to the company. Carts for both rail and ties are equipped with insulated flanged guide wheels, and each wheel has integral air-actuated brakes.
RCE Equipment Solutions Inc.
RCE Equipment Solutions Inc. — previously known as Rail Construction Equipment Co. (RCE) — has expanded its Railavator line of high-rail excavators. Whether pulling rail, cutting brush, craning items, undercutting, tamping ties, or digging and trenching, the Railavator proves its versatility, the company says.
RCE now offers six John Deere Railavator models, from a compact 50G excavator all the way up to a large 350G excavator. The company’s latest hi-rail gear package features RCE’s patented hydraulic hi-rail system that can be installed on John Deere, Caterpillar or Komatsu 20-metric-ton class excavators. The rail gear package is designed to simplify service and minimize downtime and expense.
The company’s recent name change and new website, effective June 1, reflect RCE’s growth beyond the rail market, where it built its reputation by adapting conventional heavy equipment such as excavators, wheel loaders and motor graders to specialized applications within the rail and energy industries.
Michael Popke is a Madison, Wisconsin-based freelance writer. Email comments or questions to prograil@tradepress.com.