Stay updated on news, articles and information for the rail industry
March 2024
Rail News: MOW
Rail grinding and milling revisited
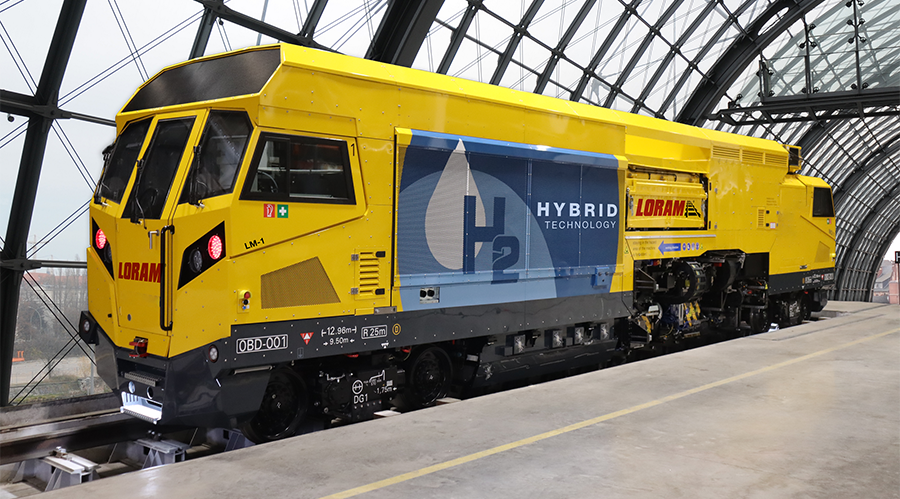
Compiled by Pat Foran
Loram
Loram continues to integrate its Rail Pro® Infinity software into the company’s production rail grinding operations. The advancement enables precise grinding and shaping of rails to desired profiles, and offers energy and fuel efficiency benefits for customers, Loram officials said in an email.
To provide more carbon emission savings, Loram partnered with Linsinger to offer the LM1 rail miller, Loram’s newest solution for reprofiling rail when heavy correction is needed. The rail miller can restore the lateral and longitudinal profile of a rail while removing surface defects; the milling technology makes it possible to remove up to 1 millimeter in a single working pass. Loram officials said. That helps extend the surface life of a rail while trimming costs, reducing a carbon footprint and improving safety, they added.
For spot treatment during tight work windows, the rail milling solution can be a cost-effective and environmentally friendly way to extend the life of rail, crossings and switches. Because milling is a rotary cutting process, only milling chips are produced and very few sparks and dust are generated by the polishing process, making it suited for use in areas that are highly sensitive to dust and fire, Loram officials said.
Loram Virtual Rail
Loram Virtual Rail uses digital twins on railroads around the globe — including in North America, Brazil, Europe and Australia — to plan grinding strategies designed to maximize rail life and improve reliability.
Loram Virtual Rail (VR) software and a patented digital twin approach helps quantify why to grind (life extensions and cost benefits), where to grind (frequency and schedule) and how to grind (rail profile and metal removal needed), Loram officials said.
Digital twins provide location-specific grinding strategies to maximize track life. Users compare how each alternative grinding strategy will impact their track life extension, return on investment and capital plans before they implement changes in the field.
The virtual testing of grinding strategies is performed by physics-based models and track data. With this approach, the simulated grinding strategy accounts for local rail condition, traffic and wheels, friction management, material selection, track geometry and other factors, Loram officials said.
The company’s digital twin models are expanding, including connecting the impact of grinding on multiple track systems like wheel-rail interface, ties, ballast and substructure, and evaluating new failure modes such as squat/stud defects. The software is modular, enabling users and their partners to input new digital twins and models and use these models in real-world applications, Loram officials said.
Once a grinding strategy is optimized and chosen, Loram’s series of scheduling tools can help users determine how to implement the grinding strategy in the most efficient way and monitor the compliance to ensure the grinding strategy is being executed as planned.
Orgo-Thermit
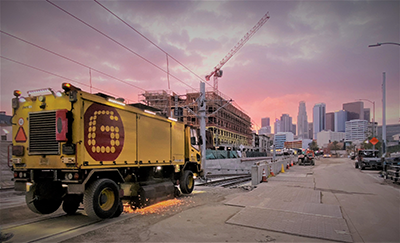
A Goldschmidt company, Orgo-Thermit offers a comprehensive grinding service that optimizes efficiency and cost-effectiveness for customers’ maintenance needs, company officials said.
Using technology such as the company’s proprietary Eddy Current system and the Trackscan Mira with up to eight probes on each rail, Orgo-Thermit conducts “thorough analyses of the track to assess and address the risks of Rolling Contact Fatigue (RCF) effectively,” company officials said.
The approach begins with a detailed examination of the track, focusing on areas such as the gauge corner, where RCF commonly occurs. By employing advanced measurement techniques, Orgo-Thermit aims to gain a complete understanding of the rail condition to tailor grinding or milling programs to target the most affected areas. This targeted approach can save customers money and minimize the track downtime required for maintenance work, Orgo-Thermit officials said.
“One of the key advantages of our methodology is the ability to prioritize maintenance efforts based on the specific needs of each customer’s track,” they said. “By concentrating resources where they are most needed, we ensure maximum impact and longevity of the track infrastructure.”
Orgo-Thermit’s trucks are equipped with profile measurement capabilities so that the required rail profile can be consistently met throughout the grinding operation.
Plasser American
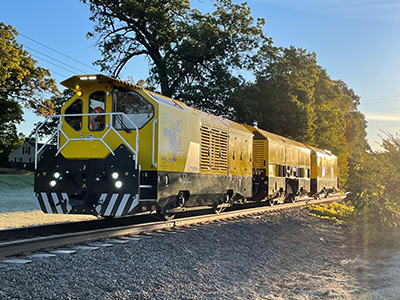
Plasser American recently became the exclusive Speno International agent for North America — a complement to Plasser American’s rail milling offerings, including the Romill Urban 3 E3 hybrid milling machine.
Rail grinding is used for preventive and medium corrective work; rail milling supplements this through corrective and regenerative maintenance capabilities, Plasser American officials said. Rail milling also offers additional advantages in dust and fire sensitive areas (tunnels, elevated tracks, urban tracks, fire ban areas, etc.) because it is a spark- and dust-free process.
A high-efficiency battery system enables the Romill Urban 3 E3 milling machine to operate in fully electric mode for up to three hours so users can work emission free (no dust, sparks or exhaust fumes, and less heat generation) in enclosed environments such as tunnels or stations. The batteries can be recharged externally or quick-charged (less than two hours, while milling) with the integrated low-emission diesel-generator, company officials said.
Romill Urban 3 E3 and Speno grinding trains are equipped with state-of-the-art technology to measure the transversal and longitudinal profile, as well as the surface crack condition.
Pandrol
Pandrol manufactures a precision frog grinder to repair shelled, spalled and corrugated (SSC) defects.
When SSC defects are caught early, they can be repaired quickly, keeping a track in service longer and preventing the need to replace the entire frog, Pandrol officials said.
By targeting the repair area in the center of the frame, and “blending out” by grinding over the length, the defects are removed, permitting smooth and continual train traffic with minimum interruption and down time, Pandrol officials said.
RailWorks
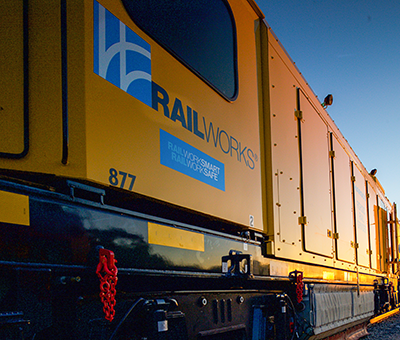
RailWorks provides state-of-the-art, turnkey switch and grade crossing rail grinding services for freight and passenger railroads.
RailWorks’ services are designed to increase rail longevity, mitigate rolling stock wear, optimize train performance and fuel economy, and refine overall ride quality.
The equipment is “highly proficient” in grinding switches, safeguarded curves and roadway crossings, RailWorks officials said.
Features include standalone hydraulically powered grinding units, advanced Jupiter II Control System, hydrostatic propulsion mechanism, comprehensive computerized control, efficient dust collection assembly, pneumatic braking apparatus, water mist fire suppression system and ergonomic control cabins for operator comfort.
Email comments or questions to pat.foran@tradepress.com.
Keywords
Browse articles on rail grinding milling Loram Loram Virtual Rail Orgo-Thermit Plasser American Pandrol RailWorksContact Progressive Railroading editorial staff.