Stay updated on news, articles and information for the rail industry
April 2012
Rail News: MOW
Railroading in the Laboratory: Recapping TTCI's 17th Annual AAR Research Review
— by Walter Weart
On March 20, a record number of registrants gathered in Pueblo, Colo., for the Transportation Technology Center Inc.'s (TTCI) 17th annual AAR Research Review. More than 500 participants filled a Pueblo Convention Center conference room. TTCI is a wholly owned subsidiary of the Association of American Railroads (AAR).
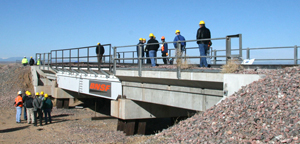
Walter Weart
Since 2011, TTCI has been evaluating a commercially produced hybrid composite beam span bridge at its Facility for Accelerated Service Testing in Pueblo, Colo.
At this year's event, participants from railroads, academic institutions, suppliers, government representatives and other related groups came to take notes on 20 research reports or take part in two concurrent workshops. Attendees hailed from 11 countries, including the United States, China, Germany, Republic of Korea and the United Kingdom.
Lisa Stabler, TTCI president, and Semih Kalay, TTCI senior vice president of the communication and train control business unit, kicked off the event with introductory remarks. Then, Federal Railroad Administration Director of Research and Development John Tunna provided a research update of sorts, discussing topics ranging from funding to specific technology. Regarding the latter: Tunna talked about a joint bar inspection system that has led to a "significant reduction" in accidents due to broken joint bars — from more than 30 in 2006 to fewer than 10 in 2010, he said.
The balance of the day was devoted to the 20 presentations and two workshops covering much of the R&D conducted at TTCI.
The presentations were divided into five technology categories — equipment, track, bridges, track inspection and maintenance, and system issues — and each section was led by a Class I engineering official. TTCI researchers delivered three to five presentations per technology category. Following each presentation series, Class I session leaders conducted panel discussions featuring engineering officials from other Class Is, as well as TTCI and the FRA. Regardless of topic, there was significant emphasis on heavy axle loads (HAL) and the implications for railroad maintenance and operation.
Key equipment technology enablers. The first section was "Key Equipment Technology Enablers" and presentations dealt with HAL-related freight car truck issues, such as wheelset life, truck maintenance and renewal costs, increased rail life and improved fuel economy. The importance of this research is borne out by annual wheel replacement expenditures estimated at more than $828 million; the replacement of about 582,000 wheelsets account for more than half of all car repair costs, said Scott Cummings, TTCI principal investigator. Included in this series was a presentation delivered by TTCI Senior Specialist Harry Tournay that covered integrated freight-car truck designs and included research on improved brake system performance.
Another presentation, delivered by TTCI Senior Engineer II Kari Gonzales, covered HAL-related couplers and related casting issues. On average, 350,000 castings were removed per year from service over the past three years with $65 million in replacement costs and $20 million dollars spent annually on train delays, Gonzales said. The project seeks to "reduce the number of train delays and broken components due to poorly fitting knuckles and couplers" by developing "recommendations to the Coupling Systems and Truck Castings Committee on tolerances for critical areas of E-type knuckles and couplers with recommended standard procedures for acceptance testing against a digital master gauge," Gonzales said.
Key track technology enablers. The "Key Track Technology Enablers" section contained five presentations covering topics ranging from fatigue and wear-resistant rail steels to welding methods to the latest developments in insulated rail joints. TTCI presenters included Daniel Szablewski, principal investigator; Daniel Gutscher, senior engineer I; Joseph LoPresti, principal investigator II; Muhammad Akhtar, senior engineer; and David Davis, senior scientist.
In the rail section, Szablewski recapped past research efforts and reviewed topics ranging from HAL-related rail issues associated with high-performance rail steels from a historical perspective to next-generation rail wear testing that's being conducted at TTCI's Facility for Accelerated Service Testing (FAST) track.
Meanwhile, Akhtar presented an insulated rail joint study that examined the effect HAL has on joint life. Performance of the insulated joint — a key component of the signal system — is critical. The aim of Akhtar's joint bar research project is to develop next-generation insulated joints with testing at FAST, then prototype testing in revenue service at five locations on Union Pacific Railroad, BNSF Railway Co. and Norfolk Southern Railway.
TTCI's Davis then reviewed the work being done in the special trackwork design and material realms. Topics included continuous mainline rail switches and frogs, flange-bearing frogs to eliminate flangeway impacts, the alignments in switches and frogs, and fatigue-and-wear resistant steels.
Bridges received special attention in a presentation dealing with extending the life of existing structures that are subject to heavy axle loads; other reports covered new bridge designs and materials. Chief concerns include aging bridges and the problems that can lead to load restrictions and slow orders.
"Freight-car axle loads have doubled during the life of many bridges and current axle loads are near bridge design loads," said TTCI Principal Investigator II Duane Otter.
A bridge originally constructed in 1912 has been installed on the FAST track and is being tested to determine how its life can be extended, Otter said. Two different types of bridge ties — glue-laminated Douglas fir and fiber-reinforced foamed urethane — are being evaluated in comparison with solid sawn timber deck ties. Researchers also are evaluating the performance of a hybrid composite beam span bridge (specifically, the commercially produced span).
Key track inspection and maintenance technologies. The "Key Track Inspection and Maintenance Technologies" session comprised four presentations. Highlights included research into the use of ground penetrating radar to examine ballast condition in an HAL context. Research is being conducted on car- and locomotive-based track geometry inspection "systems as "track geometry can change rapidly under heavy axle loading traffic," said TTCI Senior Engineer Abe Meddah, adding that the ability to use such systems will increase the frequency of inspections.
Research into automated inspection of turnouts and open track (another presentation topic) could lead to several benefits, including saving time from manual inspection and the consistency of inspection data gathering to help predict maintenance cycles and component life, said Rafael Jimenez, senior engineer I. Meanwhile, researchers also are evaluating automated systems at the open-track and turnout test facilities, he said.
The day's final session — "Key Technology Solutions for System Issues" — comprised six presentations that detailed the work being done in such areas as machine vision inspection of the underbody structure of freight cars as "heavier axle loads result in increased wear and fatigue rates to structural components," said Jim Robeda, senior engineer I. As Robeda noted, the underside of cars are difficult to inspect and about $6 million is incurred in annual accident costs related to structural component failure. Utilizing a series of light sources and cameras, the underside of moving cars can be inspected; so far, the results have been positive, Robeda said. More research is being conducted to improve detection rates for brake beams, brake rigging and the train line.
Huimin Wu, principal investigator II, presented a report about research into the causes of rail rollover derailments — work that has led to the development of recommendations that would apply to both wood and concrete ties. The research will continue this year.
Additional topics included a review of the causes of rolling contact wheel fatigue, presented by TTCI's Tournay, and the use of preventative rail grinding and friction control to extend the life of rail, presented by Dingqing Li, TTCI scientist and chief of FRA programs.
'Tour and Track Walk' talk. The next morning, Research Review attendees assembled at the TTCI test site for the "Tour and Track Walk" at the High Tonnage Loop, which is used for track component reliability, wear, and fatigue research under heavy axle loads. Fortunately, the strong, cold wind from the day before subsided until early afternoon, and by then, most attendees had returned to Pueblo.
A pre-walk orientation was conducted in one of the shop buildings, which also contained displays of some of the components that were the subject of the previous day's presentations.
There were 25 "points of interest" at various locations around the loop; attendees could view actual hardware, bridges, track components, electronic inspection equipment and techniques that were presentation subjects the day before. In addition, TTCI staff and, in some cases, the participating vendor, were on hand to discuss the work being done and answer questions.
At one location, attendees had an opportunity to witness the start of a research project where the rail, ties and old ballast had been removed in preparation for placement of four types of ballast. The aim: to study how well each held up under the test conditions at the loop.
Walter Weart is a Denver-based free-lance writer.