Stay updated on news, articles and information for the rail industry
September 2023
Rail News: MOW
Track product update: rail lubrication and friction management
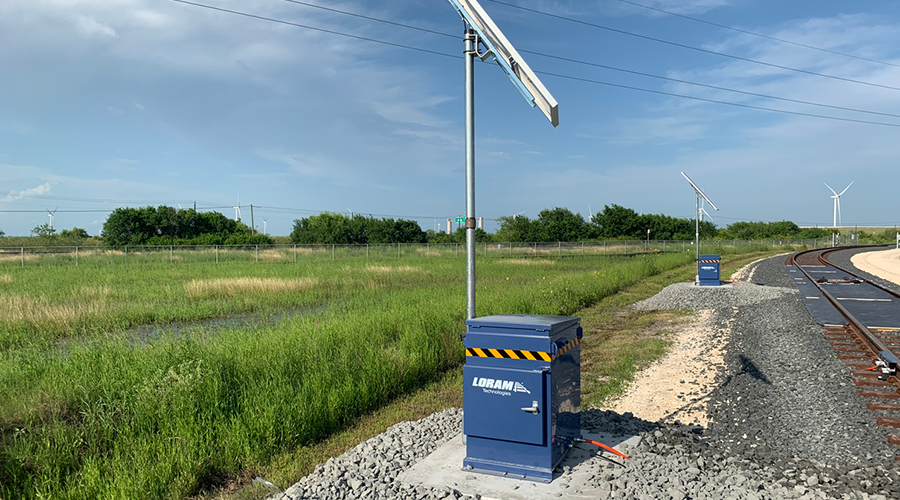
Compiled by Michael Popke
Loram Technologies Inc.
Adverse wheel and rail interaction pose one of the biggest threats to the life and performance of rail and rolling assets. To address them, Loram Technologies Inc. offers both gauge-face and top-of-rail consumables in biodegradable, synthetic and water-based versions.
Designed for transit or heavy-haul applications, the company’s gauge-face lubricants are biodegradable and remain pumpable in extremely low temperatures. EcoCurve Heavy Haul is biodegradable, carries the European Ecolabel and is suitable to use near bodies of water, Loram Technologies officials said.
EcoCurve Trackside is likewise biodegradable and has “found wide acceptance in the transit market worldwide,” they said. Meanwhile, Rail King HL is biodegradable and has high load-carrying additives suited for heavy-haul applications.
Loram Technologies’ top-of-rail (TOR) friction modifiers are designed for wayside applications. They can help reduce noise, extend rail and wheel life, and contribute to fuel savings, company officials said.
TOR-Extend is a clean synthetic friction modifier that offers a low evaporation rate, uses less material per application versus competitive products and has a carry distance of over six miles in most applications.
Loram Technologies also has introduced a family of modular tank sizes ranging from 25 gallons/200 pounds to 200 gallons/1,600 pounds in carbon steel or stainless-steel configurations. The units are available for TOR or gauge-face applications and can be solar- or AC-powered.
Easy to maintain and install, the 25/200 tank size is intended for low-traffic areas — such as switching yards and industrial spurs — and can also manage lower-tonnage Class I mainlines and transit systems, company officials said. The larger tank sizes are suited for Class I mainline applications., they added
Shell & Whitmore Reliability Solutions
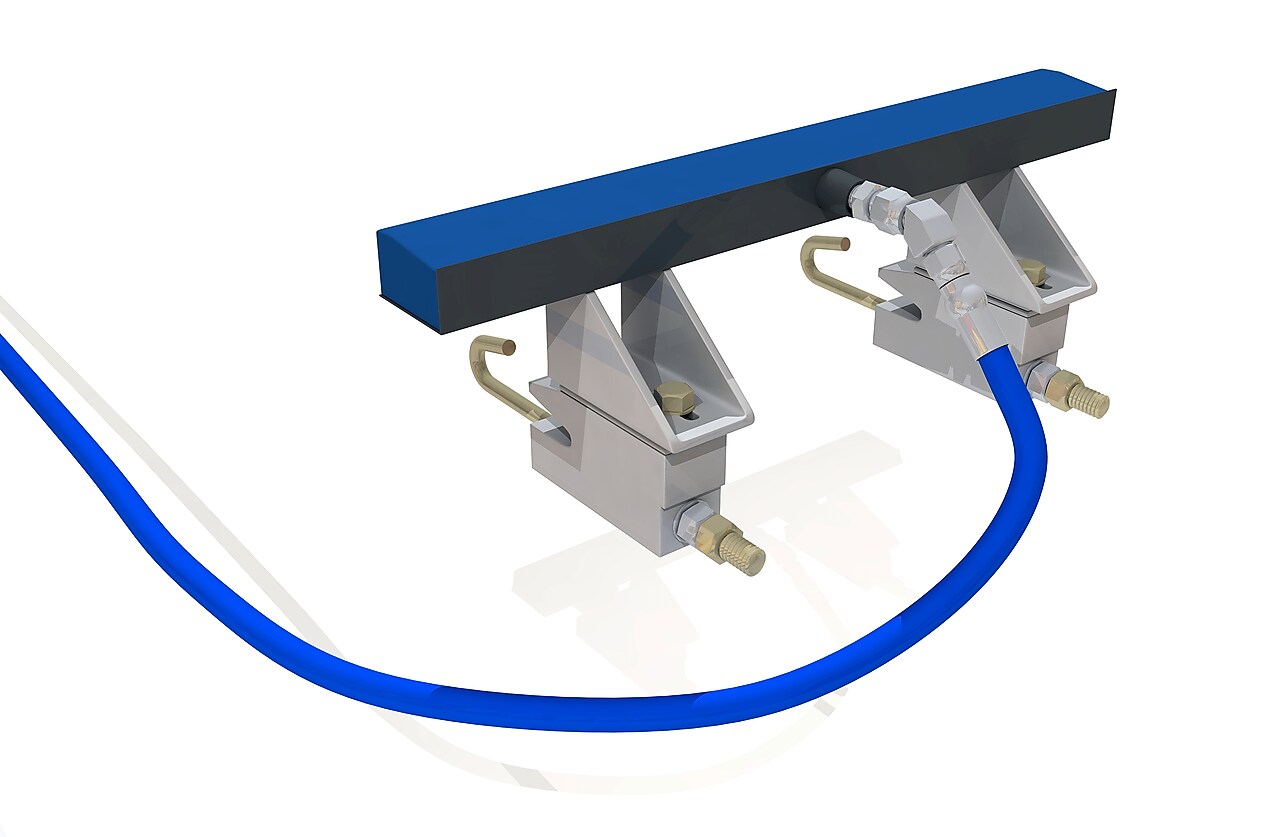
Shell & Whitmore Reliability Solutions serves Class I, II and III railroads by offering a range of equipment and services, including an integrated product portfolio featuring lubricants, friction modifiers and rail equipment.
The company’s friction management solutions include year-round, top-of-rail friction modifiers. Shell Gadus (TOR Armor) is designed to provide optimum friction at the wheel-rail interface, substantially reducing noise, wear and lateral forces, company officials said.
When wheel creep is not occurring, the coefficient of friction is lowered during normal rolling, resulting in less fuel consumption. These fuel-savings programs in tangent track are currently being implemented by Class Is, company officials said.
TOR Armor can be paired with Whitmore PolyTOR top-of-rail distribution bars, which are designed for friction modifier placement in the contact patch of the wheel and rail, reducing field-side splash and lessening the amount of product used, company officials said. Replaceable polystrip is available with the bars and can be replaced after normal wear or damage.
The company also offers a full line of gauge-face lubricants for reducing wear on a rail’s face and gauge corner.
L.B. Foster
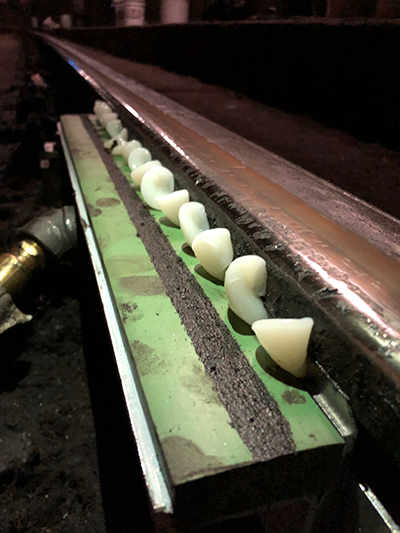
Continuously improving friction management (FM) programs to maximize fuel savings and extend rail life is important to freight railroads — especially as inflation continues and fuel remains among their largest expenses. A well-run FM program can help railroads achieve their SBTi emission reduction goals and reduce track stresses that can contribute to track spreading and derailments, L.B. Foster officials said.
The company recently introduced the MC-5 Gauge Face Grease Applicator Bar, which combines effective placement of lubricant to the gauge face/wheel flange interface with long lifecycle value for friction management customers seeking to maximize grease pick-up and carry-down while reducing waste, they said.
In the field, the bar has reduced “the propensity for bar clogging and provides our customers with best in-track performance and lifespan,” L.B. Foster officials added.
Meanwhile, there continues to be interest in remote monitoring of lubrication and friction management for validation of program performance. The use of supplemental analysis tools such as rail wear rate measurements also can be used to validate performance, said John Cotter, L.B. Foster’s general manager for friction management-Americas.
With L.B. Foster’s remote performance monitoring, railroads can use continuous geometry car data to accurately plot out the wear rate as a function of tonnage to demonstrate performance or nonperformance, Cotter said.
Robolube Industries
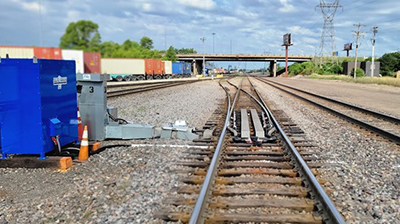
The Robolube R2K gauge-face lubricator is the latest technology in wayside lubrication from Robolube Industries.
“With the R2K, we have a fully heated system all the way to the application nozzle,” company officials said. “The R2K has no train contact, so we are able to mount it at the apex of the curve for bi-directional traffic, where solid flange contact is occurring. This allows us to achieve almost complete grease consumption by the train wheels, virtually eliminating cast off, lubrication inefficiencies and grease consumption.”
For an undisclosed Class I, the company recently installed a wheel count sensor to test and gather data for comparison to current systems in use. Over a five-day period, the number of axles that passed reached 64,000.
The aimed-for application rate of the existing lubricator units was about eight-tenths of a pound per 400 axles grease consumption, or 120 pounds of grease over the 64,000-axle timeframe. In the same scenario, the Robolube R2K Wayside Lubricator used only 10 pounds of grease per the 64,000-axle count, company officials said.
Also, Robolube last year introduced the Switch Plate Lubricator, which is designed to lubricate switch plates automatically by using switch point actuation. The idea: to eliminate the need for hand greasing on turnouts, crossovers and yard switches.
Features include user preference grease output, a 20-gallon heated grease reservoir, long refill intervals, elimination of monthly lubrication by field forces, minimal maintenance, and real-time updates and diagnostics. Railroads can lubricate from 10 to 28 switch plates, depending on turnout size and needs.
Cadillac Oil Co.
Lubricheq® RLI-100AW is made with high-quality oils, metallic soaps, extreme-pressure additives and oil-soluble surfactants, providing better lubrication and longer periods between applications compared with graphite options, Cadillac Oil Co. officials said. The product bonds itself to steel surfaces to reduce friction and wear between the base of the switch points and the switch-side plates.
Lubricheq RLI 100-AW provides high-performance lubrication, water washout protection and resistance to buildup, company officials said. Quality-tested to ensure proper viscosity under all temperature conditions, it can be used on all types of railroad switches, as well as other equipment where metal-to-metal friction needs to be reduced. It can be dispensed by pouring, brushing or spraying, and will resist wear and tear under the elements.
Key features include friction reduction to promote smooth switching operations in all weather conditions; low viscosity for easy application and pumping; water wash-off resistance for extended service life; and additive packages for low-wear and high-load carrying, company officials said.
The New Series Railavators come with many design enhancements, including a new hydraulic system. There are more components in the common manifold, which means fewer hoses, separate components and joints to potentially leak, company officials said.
Michael Popke is a Madison, Wisconsin-based freelance writer. Email comments or questions to prograil@tradepress.com.