Stay updated on news, articles and information for the rail industry
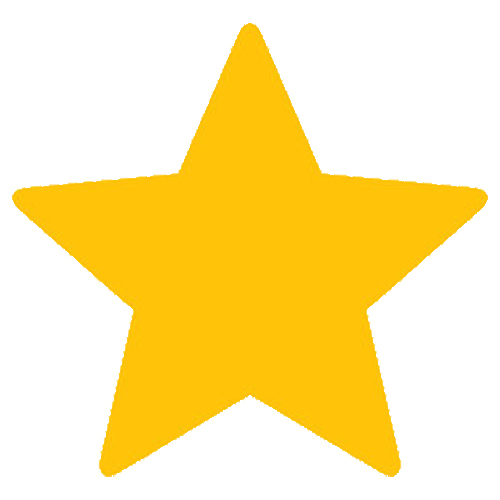
November 2012
Rail News: Norfolk Southern Railway
Norfolk Southern seeks to improve railroad safety by cultivating a new safety culture
— by Jeff Stagl, Managing Editor
In November 2010, Yardmaster Robert Garland sent an email to Norfolk Southern Corp. Chairman, President and Chief Executive Officer Wick Moorman. As part of an online “Wick’s Page” program launched several years ago, the CEO fields employees’ questions to enhance communication with the workforce.
Stationed at an Asheville, N.C., yard, Garland asked Moorman if the company would consider adopting a behavior-based safety program.
Moorman emailed Garland back and said senior executives for some time had considered implementing just such a program, one that emphasizes positive reinforcement to promote proper safe practices and focuses on determining the underlying reasons workers performed tasks in an unsafe manner. NS leaders long had sought to alter long-standing practices that relied too heavily on negative reinforcement, such as supervisor-employee confrontations and punishment threats, to ensure workers minded proper safety procedures.
The email served as a spark of sorts that helped convince Moorman and his senior team last year to move from contemplation to implementation. The primary reasons: NS was registering record safety performance and had won 23 straight E.H. Harriman gold awards, but safe practices weren’t promoted or employed in the best or most productive ways possible, and many employees believed the workplace environment was intimidating.
In addition, workers — especially new or young ones — weren’t engaged in the safety program and field workers weren’t part of the equation when it came to helping management find new ways to improve both safety and service performance.
“We had lights-out safety performance in 2011 [but] we didn’t have that buy-in from everyone in the workforce,” said Moorman during an interview at NS’ Norfolk, Va., headquarters in early October. “We want to make people feel better about the company.”
Led by Executive Vice President and Chief Operating Officer Mark Manion, the senior team now is trying to do just that by guiding a cultural change through the operating department, which will impact about 25,000 workers. The effort, which began in January and likely will cost several millions of dollars, involves training thousands of supervisors and field workers on better ways to communicate, resolve problems and positively recognize proper performance, a la more pats on the back than slaps on the wrist. The undertaking also calls for implementing dozens of initiatives designed to bolster safety and service, such freeing up supervisors from burdensome administrative tasks so they can spend more time with their subordinates.
“This isn’t really complex in any way, shape or form, but it’s extremely powerful. We have to be rule driven, yet we need to be more in a coaching mode than a compliance mode,” says Moorman. “We don’t want to overwhelm the field supervisor. We want to give them more time with workers to place more emphasis on positive feedback than to say, ‘You didn’t do this right.’”
Last year, NS hired Aubrey Daniels International Inc. (ADI), a consulting firm that specializes in behavior-based programs, to help review the railroad’s safety processes and put the cultural shift in motion. The firm conducted a written survey in late 2011 to gauge employees’ take on the safety culture.
“They basically said, ‘I like how we’re performing, but I want to be included more.’ People weren’t ranting, they were being thoughtful,” says Moorman. “The overall message was: ‘You can do this better if you rethink it.’”
Many survey respondents also “didn’t have anything good to say” about the Harriman award streak, he says.
“It’s a competition, one that created negative perceptions across the company. The general perception was that we were just trying to win the award,” says Moorman. “Sometimes, streaks turn into burdens after a while. It didn’t do anything for us anymore.”
NS is working with the other Class Is and the Association of American Railroads to institute a new award program in 2013 that recognizes teamwork and best safety practices. NS’ resolve to transition away from the Harrimans reflects the Class I’s strong commitment to move toward a new safety paradigm, senior execs say.
Perspiration and persuasion
With the culture shift in the infant phase, the senior team will need several years to try to pull off the entire exercise. A cultural change takes a lot of time and effort to foster, and senior execs want it to begin permeating the entire company next year after the heavy focus on the operating department. It’ll also take a lot of convincing by upper and lower management — and a lot of noticeable, useful changes in the workplace — to persuade all employees that NS’ safety culture is indeed transforming for the better.
“Some employees say, ‘I hope it’s true, but you gotta show me,’” says Moorman. “We’re trying to show them that we’re serious about this. This is a symbolic gesture, a real message, that maybe things will be different.”
The long, show-them mission began in earnest in mid-February, when 80 of the senior-most members of the operating group met to discuss ways that senior managers, their lieutenants and frontline supervisors could help improve the way workers from top to bottom lead, interact and communicate in a more positive manner. The top ideas generated at the meeting were freeing up supervisors’ time and engaging field workers more to participate in the cultural shift, says Manion.
“We want the supervisor to be where the action is,” he says. “If they only meet with their workers once a month, that’s a strained relationship. They should see their workers more often and get them energized, to the point where they want to see the boss coming.”
NS has implemented a number of initiatives this year to eliminate time-consuming tasks assigned to supervisors, says Manion. By spending less time enforcing minor infractions — such as ensuring train crews properly use locomotive handrails — supervisors can spend more time coaching their underlings to correct unsafe practices.
For example, an assistant trainmaster can best help his or her subordinates perform safely by listening to grasp what the issues are. They then can fix any problems while conducting themselves in a way that doesn’t alienate people when they’re critical about something, says Manion.
Many employees believed past enforcement processes made them feel they were being nitpicked and second-guessed, he says. Now, the positive-reinforcement techniques in play can improve their work and even personal lives (“If they’re happier at work, they’re happier at home,” says Manion.).
A 50/10 proposition
As they meet more often with subordinates, supervisors should spend about 50 seconds per minute complimenting the good safety practices performed by each employee and 10 seconds focusing on what still needs to be worked on, says Moorman.
One-on-one meetings tended to be a bit confrontational in the past, he says. But a worker who recently attended a positive-reinforcement meeting with his superior remarked that “it was the first time he felt it wasn’t done in a way where he believed he could lose his job,” says Moorman.
To get all one-on-ones to that point takes “putting boots on the ground” and being out in the field, says Manion.
Among the time-consuming duties that have been dropped to provide supervisors more field time: they no longer will drive crews to work sites affected by adverse weather. Since supervisors were the only ones in their area who drove four-wheel-drive vehicles, they performed that duty, says Manion. NS spent $1 million to purchase four-wheel-drive vehicles for crew transportation contractors, which now will handle that responsibility in remote locations.
Supervisors also no longer need to verify crew transportation contractors’ bills. A centralized group in Atlanta now handles that task, says Manion.
And if an incident occurs in their territory, supervisors no longer are required to fill out a lengthy report.
“It didn’t matter about the magnitude of the incident, they still had to provide a sizeable report on the root causes,” says Manion. “Now, they can fill out simpler reports for smaller incidents that are more user-friendly.”
Setting a new course
In addition to gaining more time for coaching, supervisors are receiving education and training to learn how to conduct more meaningful and productive one-on-one meetings. They are among the thousands who are or will be attending courses conducted by ADI, which is handling all training associated with the cultural shift. Training in the operating department should be completed by April 2013, says Manion.
Next year, field workers will begin attending half-day training sessions that will cover basic behavior-based skills, such as how to communicate with co-workers in a positive manner.
Training already has begun for the 200 senior-most managers, who attend a full-week course that serves as “a total immersion in behavioral science,” says Manion. Senior operations leaders then will provide coaching to help junior field supervisors.
Talking points
In addition, about 2,500 frontline supervisors will complete a two-day course, including a Crucial Conversations session that includes role-playing exercises based on work situations typically encountered in the field.
The training, which emphasizes problem-solving and conflict-resolution techniques, is especially beneficial to new supervisors, who are just beginning their managerial careers, says NS VP of Mechanical Don Graab.
“Some of them used to struggle with how to handle certain situations. Now, they have these skills that can be developed,” he says. “With so many young workers today, we need new techniques.”
After supervisors receive the training, it’s vital that the lessons learned on behavior-based safety and positive reinforcement “don’t evaporate,” says Manion. To that end, each supervisor is required to attend a debriefing session each week during which he or she must provide an example of how they used a positive-reinforcement technique.
Manion and his team do it, too.
“It helps you feel accountable,” he says. “With several thousand supervisors doing all of these things on a regular basis, it has to move the needle a bit.”
Another needle-moving mission carried out earlier this year: transforming all 145 safety committees into safety and service committees. Senior execs believe the move better aligns safety, operational performance and productivity throughout the company. Committee members solicit and brainstorm ideas on ways to notch improvements in all three buckets.
“One thing that rings a bell with people is customer service. They know who pays the bills,” says Manion. “By looking at safety and service, we’re coordinating better to zero-in on growth.”
A time-saving idea generated by a safety and service committee calls for inspecting intermodal trains while containers are being loaded. For safety reasons, inspections previously were performed after a train was completely loaded, says Manion.
“Now, the inspectors communicate with those performing loading operations to do an inspection while a train is loaded. It saves one-and-a-half hours,” he says. “We want to implement it at all of our intermodal terminals.”
In addition, safety checkups are being performed around the system in lieu of workplace safety audits. The word “audit” was negatively perceived, “like an IRS audit,” says Moorman. The checkups are geared toward recognizing employees for performing safely and promoting constructive coaching.
“The safety audits were conducted as to how things were done wrong. The safety checkups focus on how things are going well,” says Moorman.
It’s all in the mechanics
Because of the various transformational efforts, safety and operational performance are progressing well in the mechanical department, which accounts for 6,000 of the operating department ranks.
For example, a safety and service committee-assisted effort helped boost performance on both counts in a Harrisburg, Pa., yard. Committee members and workers developed a process to ensure hand brakes are released on all cars on outbound trains, says Graab.
“Sometimes, too many hand brakes were applied than necessary, which caused delays on outbound trains,” he says. “The safety tie-in is that workers were exposed to injury if too many hand brakes were applied.”
In addition, the mechanical department has begun using a PIC/NIC Analysis® tool developed by ADI that’s designed to examine forms submitted by mechanical supervisors on an employee’s behavior during a task and the factors that influenced it. The “P” and “N” stand for positive or negative consequences that could occur if an employee performs a task a certain way, and the “I” and “C” stand for immediate and/or certain consequences.
The tool will help department managers better understand how employees’ chosen way to perform tasks are involved in work-related injuries and incidents, such as a worker who tries to move a heavy piece of equipment without proper assistance or an employee who rushes to complete a mechanical repair. The tool also will help them determine how to improve work behaviors in a positive manner.
Thinking caps on
Meanwhile, mechanical and transportation workers at a Chesapeake, Va., yard worked with managers and committee members to determine ways to improve safety and operational efficiency. Rob Oliver and L.A. Griffin, both carmen at the yard, hatched an idea to replace defective wheels at the facility’s intermodal ramp instead of the shop. Now, rail cars can be back in service in less than an hour versus the several days it takes to switch a car into the yard, complete repairs and switch it back onto the ramp. The reduction in train movements helps reduce the risk of injuries or incidents, as well.
Car department and transportation workers also jointly redesigned a ground air hose system, which is used to conduct initial brake tests, to eliminate potential tripping hazards and cut service delays caused by the old hose system.
The various initiatives adopted by the mechanical department aren’t “pie-in-the-sky” concepts, but process changes that make sense to workers, says Graab.
“I’ve been here 34 years, and it’s not an exaggeration to say this is a cultural shift, that it’s real and we’re committed to it, and that we’re passionate about it,” he says. “People feel like they’re contributing and their contributions are welcomed. Before, we could become more of a fractured workforce.”
‘A more collaborative tone’
Alabama Division Superintendent Todd Reynolds concurs. There’s a more collaborative tone in the organization, and service and safety now are on par with each other, he says.
“Our people know our business, and to some degree, better than anyone,” says Reynolds. “It’s a change in the way people look at production. It’s very invigorating.”
For example, Creed McDaniel, a young engineer who co-chairs a safety and service committee in the division, came up with the idea to reactivate a spur in Bessemer, Ala., that had been out of service for eight years because it could alleviate congestion on a mainline and save transit time, says Reynolds. A conductor for about five years before he became an engineer in December 2010, the 29-year-old McDaniel and committee members worked closely with the engineering department workers to develop the idea.
The committee also suggested changing diamond types to an “owls” diamond at one location crossed by a short line to accommodate higher train speeds.
“It has been really interesting to see the level of thought and sophistication put into some of the ideas that are coming from these committees,” says Reynolds. “We are seeing suggestions for all kinds of things that are, quite frankly, surprising. As I think about how much potential can be unlocked by the culture initiatives, I am humbled.”
Still In the infant stages
Senior execs are a tad humbled by NS’ third-quarter safety performance, which showed the early stages of the cultural shift are paying dividends. The injury ratio per 200,000 manhours improved 1 percent to 0.77 compared with the third-quarter 2011 ratio. ADI consultants had said there could be a slightly negative change in the railroad’s safety data due to the cultural shift, “but we haven’t seen it,” says Moorman.
Service performance improved, too, as the third-quarter composite metric climbed to 83.3 percent versus 82.9 percent in the second quarter and 82.8 percent in the first quarter.
Despite the progress on both fronts, there’s still a long way to go, says Moorman.
“It sounds like a cliché, but it’s true: This is a journey, a long process,” he says. “It’s like an oil tanker, which might inch off to the right ever so slightly.”
For example, there still are “many behaviors out there that need to be unlearned,” says Moorman.
“In the past, we weren’t that much concerned with how things were done. This will change how we interact with each other,” he says. “It has to become a different way of doing business for us.”
Keywords
Browse articles on Norfolk Southern rail safety rail operations rail laborContact Progressive Railroading editorial staff.