Stay updated on news, articles and information for the rail industry
3/17/2020
Rail News: Positive Train Control
Technology providers offer railroads a range of PTC solutions
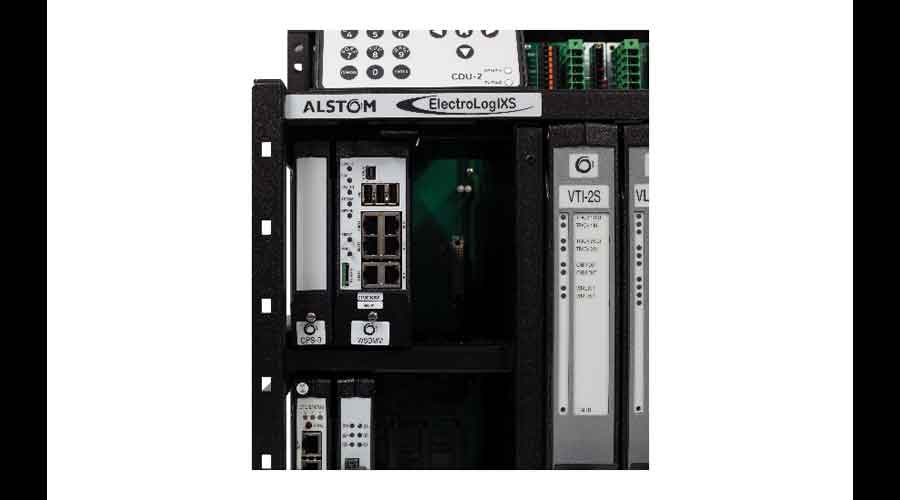
Alstom
The implementation of train-wayside-office networks across the United States for positive train control (PTC) compliance now provides a standardized communication method for “delivering the health and condition of the wayside devices to railway personnel for action,” as Alstom officials put it in an email. Accordingly, Alstom has developed technology and released new products designed to leverage this connectivity to “increase availability and incorporate predictive diagnostics into its systems,” officials said.
Wayside diagnostics have evolved to become “continuous monitors of operational aspects of devices that allow trending of the functional parameters of the devices,” they said. The company’s Wayside System Data Management Module and Data Acquisition Unit enable continuous monitoring of wayside devices such as track circuits, switch machines and signal lamps. “Continuous monitoring allows the system to self-diagnose, trend and notify railway maintenance of active and potential issues with wayside equipment,” Alstom officials said. “Ultimately, this allows action on issues much sooner and limits the impact to railway operations.”
The advantages of continuously monitoring wayside devices aren’t limited to railway signaling systems. Alstom has added continuous monitoring capabilities to its conventional grade crossing systems. Real-time status of the gates, lights and bells “lend value and provide migration into wireless crossing activation (WCA),” officials said.
Alstom’s latest generation of crossing control devices (XP4 & PMD-4) have the AAR wireless crossing activation specifications (9202, 9362, 9503) implemented. This incorporates health status messaging to the train when approaching WCA-capable crossings due to the train-to-wayside PTC network.
“Including the monitored status of devices into the PTC signaling network allows trains to take action such as slow/stop orders in advance of intersection entry, reducing the potential for collisions,” officials said.
Collins Aerospace
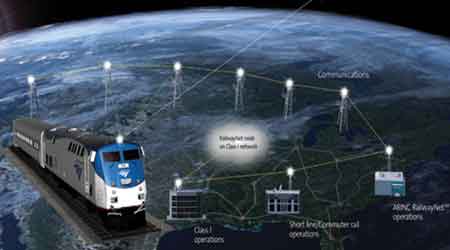
Collins Aerospace has developed a node on the Class I interoperable train control (ITC) federated network designed to enable seamless communications from the back office to the locomotive and between operations. Using VHF, cellular, Wi-Fi and MPLS, ARINC RailwayNet(SM) delivers a mandate-compliant, secure, tailored PTC messaging solution designed to reduce the need to hire and train new personnel.
“ARINC RailwayNet is built on our mission-critical communications infrastructure trusted by the global aviation industry and historically proven to achieve 99.999 percent availability,” Collins Aerospace officials said in an email.
The complexity of PTC requirements make it “paramount” for short-line and commuter railroads to choose a reliable, secure and cost-effective solution that supports seamless messaging interoperability, company officials said. Leveraging the company’s integrated rail control centers, information management and network solutions to deliver a true end-to-end solution, ARINC RailwayNet is designed to enable full back-office and inter-office messaging, security, data and configuration management, as well as provide monitoring, diagnostics and notifications.
ARINC RailwayNet is staffed with engineers experienced in PTC component development and system-level testing who “understand the criticality of proven configuration and software management processes,” officials said. Their aim: to support customers from design and testing to implementation, training and maintenance.
As a shared network solution, ARINC RailwayNet provides connectivity for short lines and commuter railroads that deal with Class Is through a node developed specifically for PTC on the ITC federated network.
Herzog
As Jan. 1, 2021 nears, more railroads are preparing to operate as PTC-protected networks. With this evolution, many railroads face significant challenges regarding PTC operation and maintenance, as Herzog officials noted in an email.
“The required skillsets and subsequent costs associated with complex troubleshooting, systems management, back office services, change management, and general support staffing are considerable obstacles for railroads to overcome,” officials said.
To ease the burden, Herzog has developed a full suite of PTC-related services and software solutions for freight and commuter railroads nationwide — including offerings such as PTC Maintenance Support Services, PTC Survey and Validation Services, Change Management solutions and PTC Hosting.
“The goal of Herzog’s PTC solutions is to offer railroads a more economical option that simplifies PTC operations and maintenance while assimilating PTC into other railroad operations,” officials said. “Herzog integrates highly qualified personnel, specialized systems, and proprietary PTC software, into a simplified, economical service offering. By offloading these complicated responsibilities onto Herzog, ongoing maintenance complications are reduced or eliminated so clients can continue their focus on daily operations.”
Lilee Systems
Per the code of Federal Regulations Title 49, Section 236.1033, the FRA requires that all wireless communications between the office, wayside and onboard components in a PTC system provide cryptographic message integrity and authentication. This level of protection “ensures that the integrity of the PTC wireless networks cannot be compromised and result in an unsafe condition,” Lilee Systems officials said in an email.
Large commuter railroads have initiated the process of implementing solutions that fulfill the federal requirements of securing PTC wireless communications and are compatible with systems used by other Northeast Corridor (NEC) operators, company officials said. Designed with system interoperability in mind and the means to manage multiple keys across the railway, the company has developed a next-generation communications management unit (CMU) solution that consists of:
• advanced encryption technologies for all wireless communications between the office, wayside and onboard components to meet the FRA requirement;
• an interoperable key management system for Advanced Civil Speed Enforcement Systems; and
• next-generation locomotive and wayside CMU hardware.
The solution supports message watermarking to encrypt wireless railroad communications, which guarantees data integrity and authentication, company officials said. To optimize connectivity, the next-generation CMU hardware implements link balancing technologies to leverage additional communications paths besides the 220 MHz network.
PS Technology Inc.
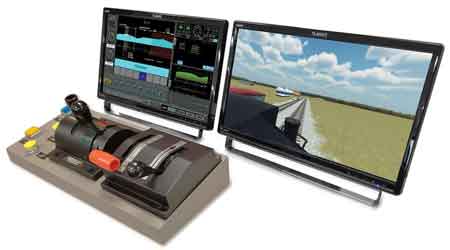
PS Technology Inc. has incorporated PTC Prime, a self-contained training tool, into all of its locomotive simulators. PTC Prime enables engineers and conductors to train at their convenience without actual locomotive cab time or dedicated instructor guidance.
“PTC training should be complete, fast and economical,” said PS Technology President Seenu Chundru in an email.
PTC Prime uses a mix of computer simulation and self-guided computer-based training, record-keeping and integration into learning management systems. The training can be linked into crew scheduling systems, which feature engineer qualification systems used to select qualified engineers for dispatchers.
PTC Prime meets FRA training requirements for engineer PTC training; the training course takes about eight hours to complete, company officials said.
For users who don’t have a PS Technology locomotive simulator, PTC Prime can be rented by the week, officials said. PS Technology can customize the training tool and provide an instructor module that allows for specific scenario-building, they added.
Siemens Mobility
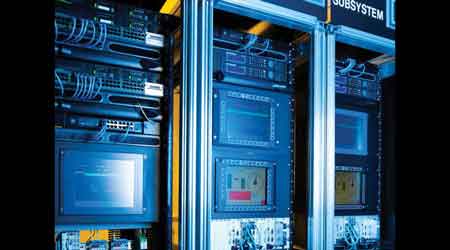
The Siemens Mobility Back Office Server (BOS) is a software solution designed to help railroads process the multitude of PTC messages delivered to a train’s onboard computer. The aim: to ensure railroads “keep running without delay,” Siemens officials said in an email. BOS is built off a SIL-3 certified architectural platform with multi-tier architecture, providing flexibility and robustness, and ensuring 99.9999 percent availability, company officials said.
Siemens Mobility’s BOS utilizes the Siemens digital WinCC OA — a flexible platform proven in mission-critical industrial applications such as scientific laboratories, gas pipelines, water processing, and “the nation’s largest railroads and subways that need to keep running 24/7,” officials said. The platform’s scalability can be increased to handle future capabilities, such as moving block and autonomous solutions. It also provides reliable load balancing as new PTC subdivisions are added.
The flexible BOS architecture is designed to provide end-user customization and continual BOS instance connectivity. It enables advanced data collection and functional migration at run-time with no operational impact, allowing software updates with no downtime, officials said.
Email comments or questions to pat.foran@tradepress.com.
Contact Progressive Railroading editorial staff.