Stay updated on news, articles and information for the rail industry
March 2016
Rail News: Rail Industry Trends
Internet of Things: Freight railroads are elevating efforts to collect, analyze and merge information from many sources
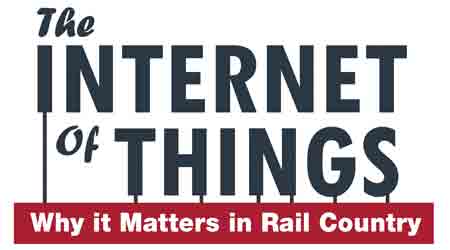
By Jeff Stagl, Managing Editor
There are dozens of sensors and electronics on a freight locomotive that monitor a host of things, such as the throttle position, track speed and fuel level. After Class Is, regionals and short lines finish implementing positive train control (PTC) by 2020, there will be exponentially more electronic devices installed on locomotives, as well as along waysides, on back-office computers and in communication systems.
So, freight railroads are trying to determine the best ways to manage and process all the information generated by the myriad systems already in place while preparing for the data onslaught to come. On both fronts, the Internet of Things (IoT) is playing a major role. Elevating efforts to collect, analyze, merge and leverage information generated from a host of sources is helping railroads increase efficiencies, boost productivity and improve processes in a number of departments.
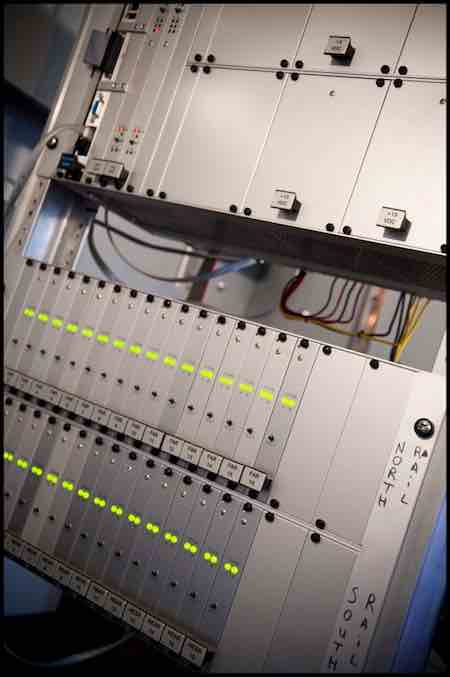
Photo: Norfolk Southern Corp.
IoT helps overcome such ongoing processing issues as data integration and correlation, and information quality and accuracy, says CN Vice President and Chief Information Officer Serge Leduc.
"We think there are infinite benefits we can gain [from IoT]," he says. "We can see patterns and leverage information to help make better business decisions."
CN can employ IoT to automate processes and decision-making, and materialize investments, says Leduc.
Ultimately, IoT congregates a lot of past and current data that needs to be manipulated and analyzed to help predict future events. In that vein, CN is developing predictive analytics capabilities with engineering and mechanical data to boost safety by preventing derailments caused by root track causes, and detecting defective track or mechanical components.
"Predictive analytics are the biggest value of IoT," says Leduc.
Pulling together data from a growing number of sources and finding the proverbial needle in a haystack — perhaps an engineer’s incorrect, yet preventable throttle-up operation — also is of high value, says CSX VP of Safety and Field Career Development Jim Marks.
"There is more and more disparate data, and we are looking to marry it together," he says. "We want a more useful stream of data that provides the precise information we need to review."
When it comes to marrying and managing a host of data, nothing compares to PTC — which will serve as the "ultimate example" of railroads leveraging IoT, says Leduc. PTC systems will integrate thousands of software-driven devices installed along track and in locomotives, he says. Wayside, locomotive and back office systems will be integrated by wireless radio, cellular, Wi-Fi and GIS satellite tracking communications.
Source: CSX
A CSX graphic illustrates a five–step work flow generated by its Event Recorder Automated Download system, which collects and transmits data from a number of locomotive sensors and devices.
An onboard computer system will receive and analyze track data from wayside locations and base-station radios, providing a locomotive engineer with advance warning of movement authority limits, speed limits and oncoming track conditions to bring a train to a safe speed or controlled stop.
If corrective action is not detected within a warning period, the PTC system will automatically apply the train’s brakes and bring it to a controlled stop without the engineer’s assistance.
Union Pacific Railroad this year expects to spend $375 million on its ongoing PTC installation, which in total is projected to cost about $2.5 billion. The Class I plans to equip more than 20,000 route miles and 5,600 locomotives with PTC components, and install more than 10,000 wayside antennas.
Through January, the railroad had installed 67 percent of total track miles with hardware and software, partially installed equipment on about 81 percent of locomotives and installed 72 percent of necessary wayside antennas.
All told, adopting PTC — a complex system of newly developed technologies that will continuously relay critical information — means implementing software designed to understand how much a train weighs, how fast it's going, whether it's traveling uphill or downhill, and other parameters.
Another interconnected layer
Adding to PTC's complexity and high IoT value is the requirement that each railroad’s chosen system be interoperable with other systems, UP officials said in an email. Any breakdown in interoperability presents unacceptable risks to the safety and efficiency of the U.S. rail network, they believe.
"Each locomotive will be programmed to work with all types of trackside equipment and vice versa, enabling passenger, commuter and freight trains from various companies to communicate and operate seamlessly across all railroad systems," UP officials said.
At CN, the total PTC price tag is about $1.2 billion (in U.S. dollars) to install the technology on portions of its U.S. network, including nearly $300 million in 2016.
In part, the Class I’s implementation plan calls for installing 1,750 control points or wayside interface units at all signals and switches in 39 subdivisions; equipping 550 locomotives with onboard computer processors and display/communications equipment for crews; placing 175 new wayside data radio base stations every 25 miles to support radio communications; and establishing Wi-Fi capability in all yards.
Intelligence gathering
Meanwhile, CN continues to pursue another information-processing initiative: the ongoing development of its Real Time Business Intelligence (RBTI) application to obtain a more integrated view of all network operations.
RBTI is designed to monitor business processes and assets by integrating current information generated from various sources and electronically displaying a single view of the "state of the railway." Operation managers can use the tool to make timely, actionable decisions that can help drive safety, service and productivity improvements, CN officials say.
The application has been available the past four or five years, but the railroad now is leveraging it more to make RBTI "a highly valuable operational tool," says Leduc.
At first, RBTI focused on delivering train and locomotive information in near real time, with drill-down capabilities to a specific region or train. In the near future, managers will be able to use the application to monitor, predict and notify crews of operational events.
Automating the detection and notification of potential operating issues will enable managers to identify and respond to incidents more proactively — using relevant, real-time information — as well as aid in documentation, communication and decision-making/preventative actions.
"To my knowledge, we are the only railroad that has reached a level of maturity with the [application] and how we use it to manage the railroad," says Leduc. "We continue to add capacity and functionality to it each year."
CN also is taking an IoT approach to analyzing track conditions. The Class I uses two track geometry cars and 25 hi-rail vehicles equipped with advanced technologies to examine rail.
In addition, CN is testing an unmanned geometry inspection box car that can be included on any freight train to provide added track monitoring capabilities of the network.
Moreover, by year’s end the railroad expects to install Vehicle Track Interaction units on 30 locomotives. An accelerometer mounted on a locomotive will detect unusual movements or accelerations resulting from track geometry and rail joint issues. The units are designed to issue email alerts to engineering forces when exceptions occur.
Under detection
Detecting anomalies along track also is an IoT-related pursuit for Norfolk Southern Railway. The Class I is pursuing a wayside detection project that will enable 1,100 hot-box and 17 wheel-impact load detectors to wirelessly collect and send commodity-based data in real time on such operational issues as hot bearings and flat wheel spots.
Collected information will be processed via a real-time analysis program supported by software supplied by TIBCO Software Inc. The program will issue four types of alerts if an anomaly is detected: minor, moderate, critical and very critical.
By July, NS expects to complete the project's first phase: integrating communications from the old system used at the detectors to a wireless and wired system.
In the year's second half, work is slated to start on phase two, which will focus on sending notifications electronically to train dispatchers’ computer screens.
"The idea is to collect more meaningful data to make complex decisions," says NS Director of Information Systems Development Warren Stubbs. "We will gain more powerful alerting capabilities."
Next year, the Class I plans to transition to phase three, which calls for developing the ability to electronically create and transmit a record about a bad order car to a mechanical shop.
"They will gain the knowledge that a car needs to be repaired — it's a much more efficient process," says Stubbs. "We want to automate human transactions and send electronic notifications directly, straight to the next party, to get accuracy and frequency."
NS also is evaluating a tool designed to assess and measure a detector's health, and electronically send the data to a back office.
To possibly be deployed yet this year, the tool would generate a ticket that would prompt a worker to check on a detector’s battery level, communication devices or other components, says Stubbs.
Computing power
For CSX, a device installed on about 3,600 locomotives is generating information-processing benefits — and is being counted on to provide even more. The Event Recorder Automated Download (ERAD) feautures an onboard computer that applies longitude and latitude coordinates to each second of train-handling event information.
ERAD downloads information to a data center, which uses computer algorithms to flag anomalies that need further attention, such as a mishandled train operation. Functional since 2011 and more broadly used since 2012, ERAD captures one event record every second and processes about 250 million rows of data daily.
Road foremen use the data to diagnose locomotive issues and provide engineers information about the safe handling of a locomotive during a trip.
Prior to 2011, foremen employed a more manual process to coach and work with engineers, says CSX's Marks.
"A more accurate name for [ERAD] is 'Virtual Road Foremen System,'" he says.
ERAD pulls data from a number of sensors and systems on a locomotive, such as those that monitor throttle position and braking.
Data is transmitted electronically and then data center workers sort out false-positive readings. Exceptions — which are determined according to certain parameters, such as an engineer’s train-handling and fuel management decisions — are emailed to a foreman, who conducts a face-to-face meeting with an engineer to discuss what was found.
"It ties into coaching and training. We can make our very good engineers even better, to develop better skills," says Marks. "If a bad behavior is detected, we want to change it."
ERAD also provides a precise GPS-type location of an exception, which is critical so an engineer can better understand exactly where he or she faltered during a trip, he says.
A safety tie-in
Since 2011, engineer-initiated emergencies involving hard braking have dropped 90 percent. The sharp decline means that in much fewer instances, brakes have shown wear and tear or trains have derailed due to hard braking.
"For us, the huge benefit has been to safety and to less wear and tear on our system," says Marks.
ERAD currently generates 18 types of exceptions, four of which are fuel-related with the remainder associated with safety issues or component wear.
CSX will continue to change exemption types as warranted, perhaps eliminating one if it doesn’t come up often, says Marks.
"We're also trying to marry the data with locomotive health information," he says. "We're working on that now."
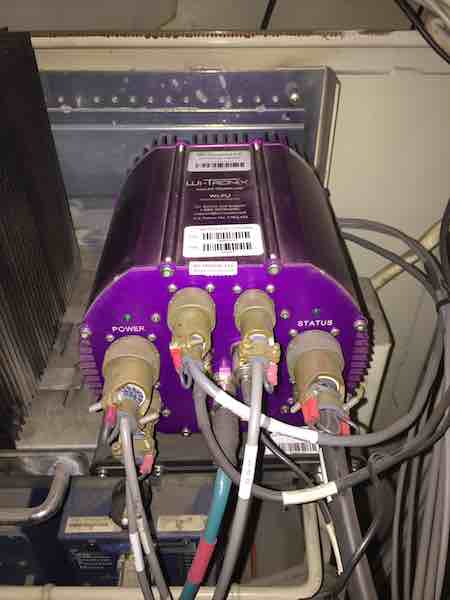
Photo: Indiana Rail Road Co.
Regionals and short lines also are working on locomotive device strategies to better process and leverage data. OmniTRAX Inc. is beginning to use a GPS-enabled device supplied by Wi-Tronix LLC to connect all sensors on a locomotive — such as those that monitor speed and fuel level — via the Internet.
"The engineer then can know the amount of fuel necessary to be effective and efficient, and if there’s enough so the train doesn't get stranded," says OmniTRAX Chief Financial Officer Hubert Gassner. "It helps us optimize fuel purchases and gain feedback so we know if a locomotive needs service."
The company began to implement the device last year on the Great Western Railway of Colorado LLC and now is focusing on installations at the Illinois Railway LLC.
"We will go from our largest and most productive railroads on down the line. We figure to complete installations in early 2017," says Gassner.
The device paid dividends on the Great Western Railway last year, when a locomotive's fuel tank was punctured and all the diesel quickly drained out.
"A sensor told us about the rapid fuel loss. We usually wouldn't have known the whole story about it until the locomotive had stopped," says Gassner.
A handy handheld device
OmniTRAX also is beginning to provide iPad mini tablets to field personnel that feature a dashboard with all the data they need to perform their tasks. To be rolled out in the same manner as the Wi-Tronix devices, the iPad minis will eliminate the use of pencils and paper pads in the field — a helpful boost to efficiency, says Gassner.
"This isn't Big Brother watching over them. It's so they can be good railroaders out on the front line," he says. "They don't have to drive to an office location. They can be out in the field and start to pull the data they need."
Indiana Rail Road Co. (INRD) is using the Wi-Tronix device on locomotives, too. Railroad managers can request specific information from a device using standard Web services, says INRD Director of IT Matt Haire.
"This is the same information available through [Wi-Tronix's] Web application, but it now gives us a way to use this raw data with other applications," he says. "This information is also helpful to our GIS, which is our other driver for IoT."
INRD also has begun expanding its monitoring capabilities outside of traditional IT equipment, says Haire.
For example, the regional's AEI readers have been converted from standard analog phone lines and dial-up modems to cellular modems.
In addition, the railroad is determining ways to network its diesel generators to obtain metrics and monitor alarms, fuel levels and output voltage.
"What we have found is that many of the devices we have looked into monitoring already have software available," says Haire. "The real benefit is gathering all of this raw data in one location, and being able to view and analyze it."
That pretty much sums up why freight railroads are employing IoT principles. There already is a lot of data and insight at hand to help power business decisions. The question for OmniTRAX's Gassner is: How do you best use and employ it?
"It’s all about using the available tools we have and applying them in our space," says Gassner.
Email questions or comments to jeff.stagl@tradepress.com.
Rail IoT Application: Switch Snowmelters
Remote monitoring and control is a core Internet of Things (IoT) application, and there are a wide range of rail-specific uses. Here’s how track switch snowmelters are factoring IoT into helping railroads be more efficient.
If a switch snowmelter fails, it will result in an inoperative switch leading to service interruptions. It will invariably require a service call-out.
So how does anyone know what’s going on out there at that critical switch? Is the snowmelter working? Can we get advance notification if there is a problem that will lead to a snowmelter failure, and potentially avoid switch failures before they happen? IoT technology, such as that found in Sno-Net from Railway Equipment Co., gives railroad personnel the ability to know what’s happening with their switch snowmelters.
Switch snowmelter systems may now be connected via wireless communication networks to allow the flow of critical information direct to authorized staff via a Web browser. Staff can see if the snowmelter is operating when it is called for, or if it is operating when it’s not needed.
Sensors allow them to see if voltage, current, propane tank levels and other key parameters are within proper operating set-points. If not, such fault conditions can be transmitted to staff immediately via notifications to their email, voicemail or handheld devices. This allows for action to be taken before a failure.
Maintenance personnel can go online and see what the snowmelter is doing and troubleshoot for potential future problems. More than anything, they will know what’s going on before getting in their truck and driving to the site, probably in unsafe weather conditions, and probably after a switch failure. Authorized personnel can turn on snowmelters from their Web browser and verify they are operating properly, all without having to travel to the location.
IoT technology allows notifications of operating conditions as they happen. Systems can also store collected data and perform continuous analytics of the accumulated data, searching for potential failure signals.
For example, a blower motor may have been operating for extended periods of time at a relatively high current. Total kilowatt hours of operation may be nearing the point where the motor has approached the end of its useful life. A notification can be sent that warns of this impending failure.
Class Is across North America, as well as transit systems such as Metrolinx and MBTA, are operating Sno-Net remote monitoring systems and using remotely operated cameras to gain a real-time image of the switch. With complete pan, tilt and zoom control, the camera can provide 360-degree visual information.
In addition to ensuring that snowmelters operate when needed, remote monitoring systems can provide notifications when a snowmelter is operating when it shouldn’t. Snowmelters often get turned on and mistakenly get left running for long periods of time, wasting many hundreds of thousands of dollars in fuel.
To prevent this, the Weather-Watcher function within Sno-Net links the nearest weather reporting station from NOAA and Environment Canada with the snowmelter to determine if it should be running. Dispatchers and other rail staff can be advised and make a decision on whether or not to continue operation.
Contributed by Joe Ashley, vice president and general manager of Railway Equipment Co.
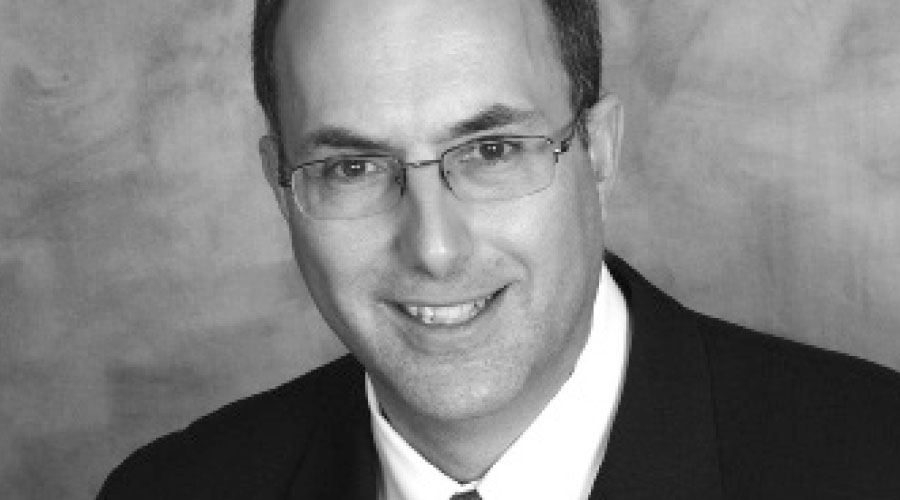
Keywords
Browse articles on Internet of Things IoT technology rail technology Big Data freight-rail technology freight-rail IoT rail IoT event recorder automated download positive train control real time business intelligence AEI readers TIBCO Software Inc. Wi-Tronix LLC Serge Leduc Jim Marks Warren Stubbs Hubert Gassner Matt HaireContact Progressive Railroading editorial staff.