Stay updated on news, articles and information for the rail industry
September 2015
Rail News: Short Lines & Regionals
Short Line Safety Institute to spread the safety culture gospel among small railroads
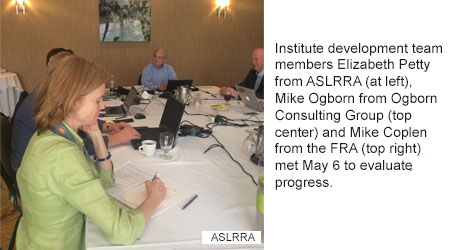
By Jeff Stagl, Managing Editor
When it comes to safety, regional and short line managers aim to ensure employees comply with all federal regulations and their respective railroad’s operating rules to help prevent accidents and injuries.
But compliance typically is measured against a safety standard that can’t be changed, so a worker’s behavior must change to comply with a rule or regulation. And since workers sometimes make incorrect decisions or take unnecessary risks, compliance doesn’t always result in the safest of behaviors, American Short Line and Regional Railroad Association (ASLRRA) officials believe.
Instead, conformance — which is measured against a chosen standard, perhaps influenced by a necessity or best practice — is a better approach, they say. A conformance standard can be changed to prompt or align with optimal behaviors that can help reduce the risk of accidents and injuries.
The ASLRRA is trying to promote the merits of a conformance-driven approach through a Short Line Safety Institute that’s in the early development stages. The institute’s primary mission: to enhance regionals’ and short lines’ safety processes and conformance through voluntary, non-punitive partnerships that help facilitate the best-possible safety culture.
The institute is charged with assessing each railroad’s culture, identifying ways to improve it, and providing leadership, training, education and research assistance. The ASLRRA defines a safety culture as the shared values, actions and behaviors that demonstrate a commitment to safety over competing compliance goals and demands.
The association is developing the Short Line Safety Institute with the Federal Railroad Administration (FRA), Volpe National Transportation Systems Center and University of Connecticut (UCONN). Initially, the partners are focusing on assessing the safety cultures of 12 regionals and short lines that transport crude oil.
The institute essentially will touch on “four pillars” in the safety realm: culture/awareness, education/training, research and benchmarking, says ASLRRA President Linda Bauer Darr.
The timing is right for the initiative because crude shipments have increased on short lines, there are a number of new small railroads and there’s a heightened awareness about safety in the rail industry, primarily due to recent crude-by-rail accidents, the positive train control mandate, new federal tank-car rule and ongoing two-person crew debate, she says.
Since short lines tend to follow the Class Is instead of taking the lead in a lot of areas, there are many things that aren’t under short lines’ control, says Darr.
“The institute will foster big differences in the control of safety affecting people and [operations] on tracks,” she says. “We can be more effective in the human-factor space, and we can help make significant improvements for rail safety at large.”
FRA has a say
The effort to develop the institute began two years ago, when the FRA sought to forge a long-term, supportive relationship with the short-line industry regarding safety. The agency also hadn’t conducted any pilot projects with short lines before, FRA officials say.
In late 2013, U.S. Transportation Secretary Anthony Foxx reached out to then ASLRRA President Richard Timmons to discuss ways to improve crude-by-rail safety. In January 2014, Timmons sent a letter to Foxx proposing the establishment of a Short Line Safety Institute. The FRA then provided two start-up grants and Congress appropriated $2 million to help launch the institute.
Job No. 1 for the institute is the initial assessments, which are performed by a group of safety experts. The ASLRRA in January lined up the following five experts as contracted assessors: Wayne Hamm, who has more than 36 years of rail safety and operating experience; Pat Black, who has more than 30 years of rail safety and operating experience; Annie Richardson, who has more than 20 years of safety assessment and related experience; Shannon Adamson, who has more than 14 years of rail and assessment experience; and Sam Cotton, who has 17 years of rail safety and operating experience.
The assessors analyze a railroad’s practices and culture, then provide confidential, unbiased and candid recommendations on ways to implement changes and improvements. They help determine whether: the railroad’s leaders are committed to safety; there are continuous-learning practices in place; employees feel personally responsible for safety; open and effective communication is practiced organization-wide; mutual trust is fostered between employees and management; and training and resources are available.
“We’re asking railroads to be candid and self-critical,” says Darr.
Filling the safety gaps
A team of three or four assessors observe operations and conduct interviews with senior managers, supervisors and employees according to a strict protocol or standardized “script,” says JR Sampson, a former vice president of safety and rules for OmniTRAX Inc. who in late 2014 was appointed by the ASLRRA as the institute’s assessor/assessment coordinator. The railroad receives a confidential report after an assessment is completed.
“The assessors aren’t determining compliance but the conformity to the safety standards set by that particular railroad. They look for gaps,” says Sampson. “Then, we stand ready to work with the railroad to close the gaps.”
Conducted in a “non-invasive” way so operations aren’t interrupted, the assessments are free and take five to 10 days to complete based on a railroad’s size, he says. Prior to an assessment, a coordinator meets with the railroad’s leaders to review the project, scope and safety-related information needed by the assessors. All employees are encouraged to complete surveys before assessors arrive.
The initial assessments target the 12 crude-carrying railroads — which won’t be identified for confidentiality reasons — not only because they transport oil, but because they vary in sizes and track lengths, says Mike Ogborn of Ogborn Consulting Group LLC, a former OmniTRAX managing director and executive VP who serves as a liaison on the ASLRRA’s institute development team.
To date, three assessments have been performed and the other nine are pegged for completion by year’s end or in early 2016. The goal is to conduct assessments at every regional and short line, says Ogborn.
Follow-up visits to gauge progress will be conducted with each railroad within several months of an assessment. The assessment/follow-up process is being tested and, going forward, likely will be tweaked, says Ogborn.
The Volpe center helped develop the institute plan and train assessors, while UCONN helped develop the surveys. The university also will compile survey results and provide “industrial psychology ideas,” says Ogborn. The FRA will help develop a curriculum and education/training resources, as well as monitor and assess the institute’s effectiveness and how the concept could be applied beyond the short-line industry.
The intent is to create a freestanding institute with a director and staff that will provide guidance, educational opportunities and training, says Ogborn.
The institute also will share best practices and develop data analysis and research capabilities.
“Eventually, it will issue reports about commonalities,” says Ogborn.
Seeking a full-time director
In fall, the ASLRRA plans to begin interviewing and evaluating candidates for the director position, says Darr.
“We need a person to look out for the institute, to manage it full time,” she says, adding that she will continue to oversee it.
The ASLRRA wants to involve stakeholders in the institute’s development process, so the association scheduled a listening session on Sept. 10 in Washington, D.C. Fifty invited guests — including short-line holding company executives and ASLRRA committee members — were selected from a controlled list to prompt discussions and engagement at the event, says Darr.
The session was set up to delve into how Class Is develop their safety cultures, and how Genesee & Wyoming Inc. delivers the same messages and prompts consistent safety performance among its 120 North American railroads, she says.
In addition, representatives from other trade associations were expected to discuss their approaches to changing safety cultures. Plus, executives from organizations outside the rail industry were scheduled to talk about “how they drove cultural change, and how they got the mindset and the commitment,” says Darr.
After the listening session, ASLRRA staffers plan to meet to determine how to provide short-line members information that was reviewed and disseminated at the event.
Distributing pertinent information will be a primary function of the institute. Since a railroad accident on the East Coast can impact short-line operations on the West Coast, learning where safety gaps exist — and then identifying the best methods to reach and engage short lines — can help transform safety industry-wide, ASLRRA officials believe.
For now, institute development team members are analyzing ways to reach out to regionals and short lines.
“We need to determine how to best deliver and customize information, and share best practices. Is it a lunchtime webinar or a poster with tips?” says Darr.
Since the leaders of many ASLRRA member railroads “wear a lot of hats,” the assessments are a critical first step in developing the institute, she says.
“This is just the tip of the process now. The pilots underway are a major focus,” says Darr. “But this is a ‘forever’ deal, and we will continue to assess safety.”