Stay updated on news, articles and information for the rail industry
SPONSORED
Vision Research - Branded Feature
Machine Vision Railway Inspection Gets a Boost From High-Speed Cameras
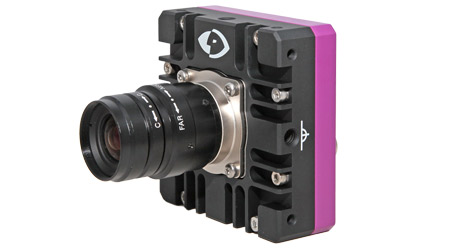
Regular inspection of rail tracks and the associated components is critical to the efficient and safe operation of railways. However, a number of factors can make inspections costly and time consuming and produce inconsistent results. Traditionally, inspections were performed manually, with skilled inspectors reviewing the tracks visually. Not only was this process time consuming, but often produced inconsistent results derived from subjective assessments and inspector fatigue. Given the large amount of effort required and inconsistent results produced using manual inspection methods, there is significant benefit in developing alternative solutions using non-destructive testing (NDT) methods.
In recent years, NDT solutions have made great strides reducing the track inspection time required to analyze and removing inconsistencies. This has been done by standardizing results through measurement and algorithmic processes. These results were buoyed by significant advances in computing capability, ultrasound and machine vision technologies. However, new technologies offer an even greater leap forward in NDT capabilities. Many are looking towards these new technologies as the driving force behind inspection advancements. The industry will benefit from faster inspection processes as well as better capability to manage data and images impacted by weather, such as snow, rain and dust. As supporting technologies in computing, ultrasound and machine vision improve, inspection solutions can be poised to capitalize on those improvements to meet industry needs.
Many companies and institutions have engaged in numerous academic studies and collaborations over approximately the past 15 years in the effort to improve rail inspection. They have primarily focused on automating portions of the inspection process and have laid the groundwork for new technology innovation in this area. These efforts have focused on two technologies for surface inspection: Ultrasound and Machine Vision. As would be expected, each technology offers advantages as well as carries challenges unique to the applied application.
Ultrasonic Inspection Systems
Ultrasound is a very popular technology for NDT of rail tracks. Ultrasound transmits sound waves using transducers which then receive reflected signals back to measure an object’s surface and detect any flaws through variation in the measurements. The data is reported immediately for an operator to analyze. Systems may either be hand-held and walked along a track or part of a vehicle. These systems are used for identifying and analyzing defects in rail tracks as opposed to other components such as anchors or ties. Its widespread use is beneficial in terms of training and learning curves. Another benefit is simultaneous inspection of the three sides of the track subject to wear and defects. An additional benefit is the standardization of measurement data to assess defects. Ultrasonic NDT also faces some challenges. First, it can be time consuming, especially for walking units. It also often requires the operator to monitor, understand and react to the data as it is being presented. Also, while Ultrasound is commonly used for rail track inspection, the technology does not lend itself well to other components critical to the track infrastructure, such as anchors.
Machine Vision Inspection Systems
Machine Vision is an alternative to Ultrasound and is growing in popularity for NDT of rail ways. Machine Vision Systems often use a set of cameras paired with lights or lasers used to illuminate the subject. The fastest machine vision technology until recently was line-scan technology, a method where individual rows or sets of rows are read from the camera sensor as an object passes through its field of view. The rows are then stitched to form a complete image. Algorithms and measurements are then applied to the image to identify defects. The data can be stored with long-record time DVRs or used for real-time analysis.
The benefits of a Machine Vision NDT system are multi-fold.
- Machine Vision systems are among the fastest inspection systems and can gather and process data at up ranges between 20 - 50 Mph.
- Algorithms provide consistent analysis of defects as images are compared against an established set of parameters, providing a high level of automated inspection.
- Because the cameras capture all objects in the Field of View (FOV) a Machine Vision system is capable of analyzing multiple components for defects, including tracks, anchors, and other items intrinsic to the safe operation of the railway. This capability gives added flexibility to railway inspection processes.
However, many machine vision systems also face challenges.
- As they typically use standard machine vision cameras that are used in other typical inspection processes, the maximum frame rates impact the speed a rail NDT system can perform at
- Many machine vision cameras have image quality and light sensitivity that works well in indoor, controlled environments, but are not designed for the environmental challenges seen in railway inspection. In situations such as poor or wet weather conditions, where the object being analyzed is not clear or there is excessive glare or darkness, typical machine vision cameras may not be able to properly capture and analyze the required images.
New Imaging and Inspection Technology Advancements
Recent advances in machine vision camera technology can alleviate these challenges. Vision Research, manufacturer of Phantom high-speed cameras, has introduced several of the world’s fastest extreme high-speed cameras with functioning CoaxPress CXP6 interface. This brings cameras and sensors specifically designed for extreme high-speed imaging to machine vision applications like NDT inspection. High-speed sensors differ from the sensors found in many conventional machine vision cameras because they are designed to process data quickly, have as much light sensitivity as possible, as well as have high image quality. Previously, high-speed sensors were primarily available only in stand-alone cameras with RAM to capture the images, which then needed to be downloaded for analysis. Placing the Phantom high-speed sensors in a camera with a CXP6 interface brings high quality imaging at high frame rates to machine vision applications. The accompanying video shows the difference between a Phantom S210 high-speed machine vision camera and a commonly commercial camera while imagining a road way and a car tire to highlight the image performance of the S210.
This advance in machine vision camera technology can bring significant improvements to railway NDT. Phantom high-speed cameras use area scan technology, capturing an entire frame at once. The most modest high-speed machine vision camera of the Phantom family, the Phantom S200, operates at 7,000 frames per second at a 640 x 480 resolution, or the Phantom S210 performs at 1,730 frames per second at a 1280 x 1080 resolution. Each provides significantly more imaging speed than many conventional machine vision cameras, allowing the entire inspection system to travel more quickly and still capture the required images for analysis. Additionally, the low noise levels and high dynamic range inherent in the high-speed sensors allow them to more readily manage the poor image conditions caused by weather. This capability can allow machine vision NDT systems to achieve the same job in half the time and also be used for more hours or days in imperfect weather conditions.
Traditional machine vision cameras often use interfaces such as GigE, CameraLink, or USB. While Phantom high-speed machine vision cameras use CoaXpress CXP6 interface because it allows for higher data transfer rates. Phantom cameras rely on the same GenICam protocol as other interfaces. This means that camera control follows the same protocols as standard machine vision cameras, reducing learning curves in applying this new technology.
Given the advantages that Phantom high-speed machine vision cameras can bring to automated NDT of railways, they may fuel new improvements in the inspection industry.
For more information, go to: www.phantomhighspeed.com/xtrmmv