Stay updated on news, articles and information for the rail industry
July 2021
Rail News: Supplier Spotlight
Fueled for thought: Today’s fuel management technology options
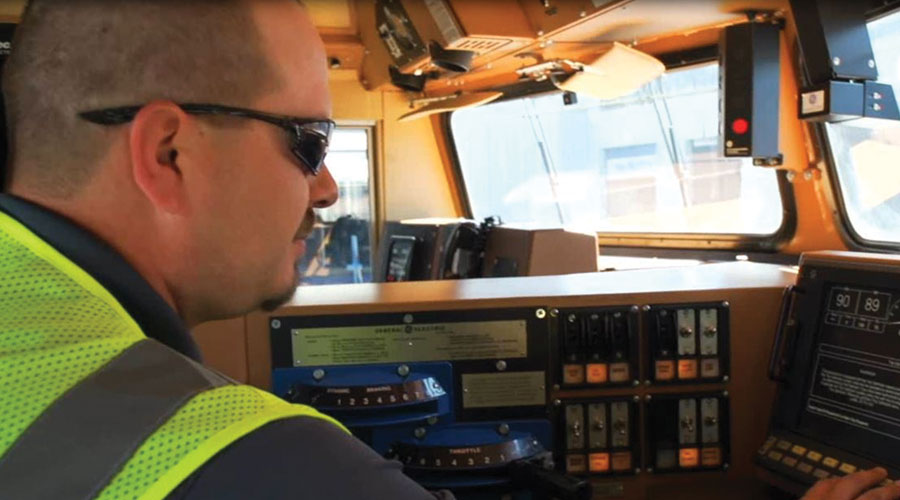
Fuel costs typically are staggering for many railroads since they continue to rely on diesel locomotives. Collectively, they spend billions of dollars each year.At least lower average diesel prices, reduced gross ton-miles or ridership and improved fuel efficiency helped drive down that major chunk of their annual expenses last year.
For example, Norfolk Southern Railway’s, CSX’s, BNSF Railway Co.’s and Union Pacific Railroad’s fuel costs fell 44% to $953 million, 40% to $541 million, 39% to $1.8 billion and 38% to $1.3 billion, respectively, compared with 2019 levels. On the passenger-rail side, Amtrak cut fuel, power and utilities costs 44.7% to $215.5 million in fiscal-year 2020, which ended Sept. 30.
Although diesel expenses haven’t been hard to take of late, market factors can change quickly and pump up costs. So railroads will continue to focus on conservation and efficiency efforts to reduce fuel consumption. They’ll also keep turning to the supply community for assistance.
Progressive Railroading recently contacted a number of fuel management equipment suppliers to share their latest offerings for railroads. Following are emailed responses from seven of them.
Wabtec
Trains are typically built with enough horsepower to achieve a minimum speed on the ruling grade of a planned route. This helps prevent stalls, but leads to excessive horsepower on almost all other parts of a route. Excess horsepower results in reduced fuel efficiency and increased greenhouse gas emissions.
A solution to this problem is Wabtec’s Trip Optimizer™ SmartHPT (Horse Power/Ton). The device’s functionality enables a railroad to set a horsepower limit that will allow SmartHPT to either isolate, idle or horsepower-limit a train to save more fuel than Trip Optimizer can alone.
SmartHPT is in use at several railroads worldwide. In the United States, the standard version of SmartHPT — which is certified by the Environmental Protection Agency (EPA) for emission reduction — has proven to reduce fuel burn by 5%, Wabtec officials said.
New versions of SmartHPT are currently being deployed with more flexibility for use of horsepower limits, improved interoperability of mixed consist trains and reduced onboard hardware requirements. Wabtec plans to monitor results from these deployments and work with the EPA for additional certifications in the future.
Railroad customers also are seeking the ability to use Trip Optimizer from stop to stop, or what Wabtec characterizes as zero-to-zero operation. This brings additional automation to a freight railroad and allows Trip Optimizer and SmartHPT to remain in auto mode longer, saving even more fuel, Wabtec officials said. The global production launch of this functionality is underway, with the full release expected in 2022.
New York Air Brake
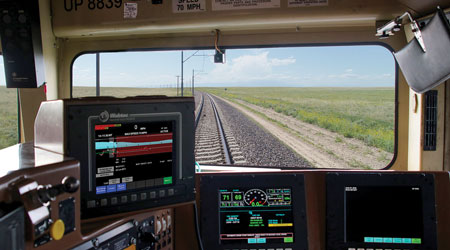
New York Air Brake (NYAB) provides the LEADER® (Locomotive Engineer Assist/Display & Event Recorder) AutoControl™ system, a proven onboard train control and energy management system that’s deployed on more than 5,000 locomotives worldwide, company officials said.
While reducing fuel costs is essential to railroads, LEADER also offers superior train handling, they said. It performs high fidelity onboard simulations to reduce dynamic and static in-train forces, providing more precise control to optimize train performance and fuel economy. LEADER has delivered fuel savings of 6% or more, NYAB officials said.
Safely running long and heavy trains is of great interest in the precision scheduled railroading world, where maximizing asset utilization is key. Customers report they are running longer and heavier trains with no derailments or break-in-twos, and credit LEADER’s ability to accurately predict run-in and run-out impacts, NYAB officials said. Actions can be taken in real time to minimize in-train forces, regardless of power distribution or consist.
LEADER is designed to precisely control distributed power — particularly asynchronous distributed power — resulting in additional opportunities to minimize in-train forces, improve safety and save fuel, NYAB officials said.
LEADER also helps railroads improve their operating ratio in other ways, including the potential to earn EPA emissions credits through locomotive manufacturers and re-manufacturers; reduce stress on draft gear caused by unchecked in-train forces; and fully leverage investments in positive train control or other train-protection technologies. Most recently, LEADER has provided key functionalities for autonomous train operation initiatives, NYAB officials said.
Progress Rail
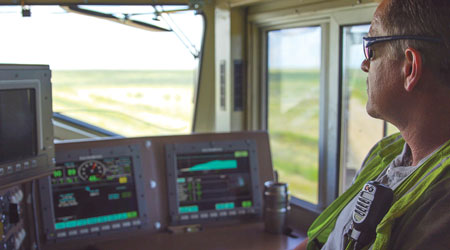
Progress Rail aims to be at the forefront of railroad automation initiatives to help customers better optimize operations and efficiency. The company’s products are designed to improve the capacity and fuel efficiency of railroads, resulting in a greener and more sustainable operation.
Progress Rail offers the Talos™ Energy Management (EM) train automation software that can automatically and efficiently control a train’s throttle and dynamic brake. Customer deployments are experiencing up to a 15% reduction in fuel consumption, lower in-train forces and more consistent train operation, Progress Rail officials said. Talos also increases safety by allowing locomotive engineers to focus more on the overall situational awareness of a train’s surroundings, they said.
In addition, Progress Rail has gained the NitroMP movement planner and pacing tool through its recent acquisition of leading decision support software company Nitryx. NitroMP uses cutting-edge machine learning and optimization tools to improve railroad network operations, Progress Rail officials said. Current customer deployments are registering a more than 10% increase in network capacity without additional assets or infrastructure investments, they added.
As automation becomes an integral part of operations, Progress Rail strives to further improve the efficiency and fluidity of railroad networks by connecting a movement plan to Talos train automation to further optimize a “meet and pass.” During a meet-and-pass situation, Movement Planner can optimize a train’s speed while Talos EM controls fuel consumption, thereby avoiding a delay caused by one train waiting for the other. That can potentially result in an additional fuel consumption decrease of about 20%, Progress Rail officials said.
Hotstart Thermal Management
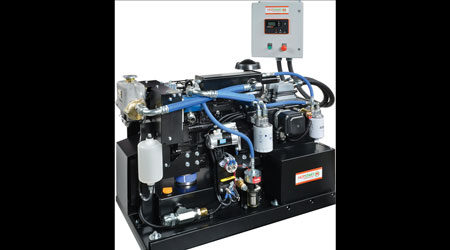
The company’s idle reduction systems play a key fuel management role for Class Is and short lines during cold weather, Hotstart Thermal Management officials said. A Hotstart system can replace the need to idle a locomotive by keeping the prime mover warm and ready to start.
Locomotive engines typically use three to six gallons of fuel per hour while idling, depending on the make and model. The Hotstart APU consumes only a half gallon of fuel an hour to help maintain the heat needed for startability in remote locations.
And for locomotives that are parked in a yard at night, electric heating systems such as Hotstart’s DLV Dual Fluid Heater or CLV Single Fluid Heater can help keep engines warm with no fuel required, company officials said. Depending on the cost of diesel and the resulting savings from fuel management, an investment in a Hotstart idle reduction system can be recouped within a few winter seasons, they added.
Power Drives Inc. (PDI)
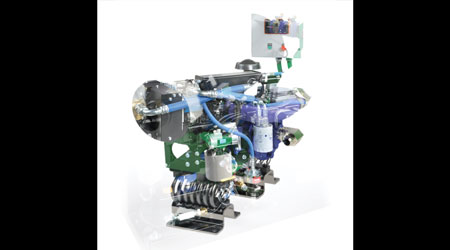
Oftentimes, calculating the return on investment in a new technology is difficult. Thankfully, when it comes to fuel-saving idle reduction technologies, the return is more clear.
If the new technology can also eliminate maintenance concerns with existing products — such as having to maintain an additional engine on a locomotive and ensuring that the battery bank is adequately charged — then it’s a “no-brainer,” PDI officials said.
The PowerHouse™ Hybrid from PDI is the newest model in the PowerHouse™ lineup and addresses those concerns by eliminating the engine as an APU and powering itself directly from the locomotive battery bank. The Hybrid can run off the locomotive batteries for up to seven days without starting the engine, and when plugged into an external 120 VAC power source, it can charge the locomotive batteries.
The PowerHouse system is designed to heat the engine oil and circulate heated coolant through the locomotive engine block and cooling system to maintain a fluid temperature above 100 degrees F — even in the coldest temperatures — via a diesel fired heating unit.
Actual customer savings have surpassed their investment in as few as three months, PDI officials said. More Class Is and short lines realize how the one-time purchase saves them money and maintenance time over the long haul, with typical fuel usage savings of over 10,000 gallons in just one season, they added.
The PowerHouse system also helps railroads comply with U.S. and global emissions standards, and operates in the harshest conditions with proven dependability, PDI officials said.
CWI Railroad System Specialists
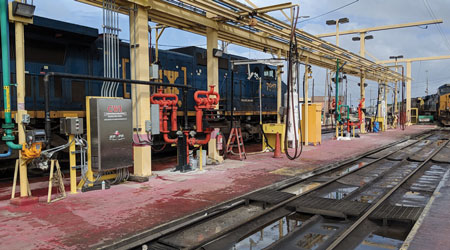
A fully licensed and insured railroad contractor with more than 37 years of rail yard experience, CWI Inc. provides custom facilities equipment to complete design-and-build Class I locomotive service centers.
CWI has engineered, built, installed and maintained RYDM (Rail Yard Data Management) throughout North America. The modular-based proprietary data collection and controls system can be used to access real-time data and reports for all fueling operations, including deliveries, tank inventories, mobile LST operations and locomotive fueling.
At its core, RYDM is run with Allen Bradley Micrologix PLCs and uses single cellular points to communicate fuel data back to CWI servers for instant online access to all site-generated data.
At a locomotive service center, CWI strategically installs tag readers at the limits of each service track to automatically scan entering locomotives and attribute fueling event data to that specific locomotive, company officials said. After a locomotive is hooked up to a fuel nozzle, a worker uses local HMI touch screens to hit start.
RYDM then takes over, controlling the pumps, valves, flow rates and other factors, while simultaneously pushing data to a customer’s RYDM website dashboard. Including fuel, RYDM can integrate into all mechanical facilities servicing systems for leak detection, truck and tank-car loading, tank monitoring, AEI locomotive tracking, nozzle pressure controls, automated fault/bypass/report emails, LST and fixed locomotive fueling, and sand system and oil system monitoring.
Railhead Corp.
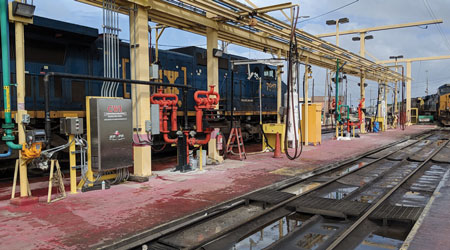
Railroads are always seeking the best ways to save fuel. Knowing how much fuel is in a tank helps, but knowing how much fuel is burned over a given run is more useful for making decisions as to when and how much diesel to add at given refilling points.
Railhead Corp. provides an ultrasonic fuel sensor designed to provide locomotive fuel level data to the remote monitoring system for display in a back office. The fuel sensor utilizes Railhead software to provide enhanced fuel level readings.
The company’s technology enables customers to monitor fuel levels and engine idle times, and create custom alerts around fuel loss, fuel utilization and trip planning, Railhead officials said.
Email questions or comments to jeff.stagl@tradepress.com.