Stay updated on news, articles and information for the rail industry
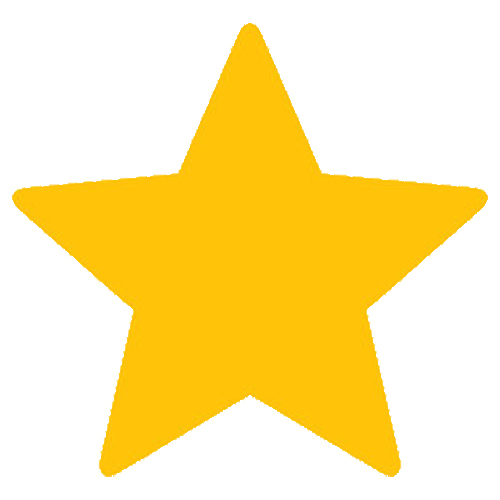
January 2008
Rail News: Union Pacific Railroad
Union Pacific Railroad: A pipeline approach
By Jeff Stagl, Managing Editor
On a cold and blustery fall day, not too many trains were blowing into Union Pacific Railroad’s Bailey Yard. Managers at the North Platte, Neb., facility were puzzled — and practically apologetic to yours truly, a first-time Bailey Yard visitor — that the world’s largest classification yard was on pace to handle less traffic than a typical day’s 150 trains and 13,000-plus rail cars. After all, it was Nov. 7, in the throes of the fall peak and strong coal demand.
What a difference a few years make. It wasn’t long ago that yard and terminal managers were apologizing to shippers for congested facilities, clogged mainlines and transit delays.
Since 2005, senior managers and department supervisors have worked together to decrease cars on line, terminal dwell time and train starts, increase train velocity and length, and expand capacity.
So far, their efforts are paying off —in the form of a more fluid Bailey Yard. Eastbound coal trains now are serviced in about 3.3 hours vs. 2004’s 3.8-hour average, and servicing time is trending downward toward a 2.75-hour goal even though train size has increased the past few years from 127 to 130 cars.
The day before my Bailey Yard tour, senior executives at UP’s Omaha, Neb., headquarters told me — quite enthusiastically and emphatically — that the Class I is shedding its “slow-moving traffic” tag and getting closer to becoming a free-flowing railroad.
One that, with a fluid network, can continue to attract more business and increase rates to generate more capital and boost earnings.
“We’re more like a pipeline,” says UP Executive Vice President of Operations Dennis Duffy. “We have a balanced workload. Our inventory is down by 6,000 cars, which doesn’t sound like much, but 100 cars equals one mile of congestion.”
Senior execs point to a few key decisions that have propelled UP down the pipeline path. Chief among them: the creation and execution of the Unified Plan, a “clean sheet” approach to the railroad’s transportation plan. They’ve also opted to implement “lean management” process-improvement initiatives; adopt emerging technologies; invest billions of dollars to build more track and facilities, hire more train and engine-service workers, and acquire more locomotives; and obtain better strategic planning tools to more accurately forecast traffic demand and patterns.
Now, forecast accuracy has improved 15 percent and, since mid-2006, car cycle times have decreased about 5 percent, from more than 10 days to 9.5 days. Execs’ aim going forward: to continue making the right reads and calling the right shots.
“We’ve built up flexibility and surge capacity,” says UP Chairman, President and Chief Executive Officer Jim Young. “But to meet our customers’ expectations, we have to have consistency.”
‘X’ marks the spot
It’ll be awhile before North America’s largest Class I is a consistent performer. For example, the “Red-X” — two lines totaling 2,560 route miles between Bill, Wyo., and St. Louis, and Green River, Wyo., and Chicago that cross to form an “x” — handles 40 percent of UP’s gross ton miles and generates 39 percent of annual revenue, yet accounts for only 8 percent of total route miles. The Red-X’s traffic density presents major operational challenges, senior execs say.
“How do you meter that railroad? We’re still learning how to get open track available and avoid disruptions to the network,” says Young. “Our No. 1 challenge is determining how to maintain the railroad with this level of density.”
The problem is, no one’s ever managed a railroad that moves as much freight traffic as UP, says Senior VP of Strategic Planning and Administration Charles Eisele. Through 2007’s first 11 months, the railroad originated 4.4 million carloads, more than 200,000 units ahead of its nearest competitor, BNSF Railway Co.
“We’re writing the rulebook as we go along,” says Eisele. “We do risk analysis. You try to maximize likelihoods and have contingencies, and the ‘what if you’re wrong?’ question is always built in.”
To guard against second-guessing, all departments need to keep working collectively, says EVP of Marketing and Sales Jack Koraleski.
“For years, we took on business and left it to operations to figure out how to handle it,” he says. “We’re working together now and are sometimes telling customers, ‘We can’t do it.’ It’s better to be up-front.”
Favorable feedback
Shippers are noticing that service improvement is front and center at UP, execs say. Although the railroad is increasing rates like other large roads, efforts to become a better-performing railroad have helped customers “see the service and price trade-off,” says Young.
UP’s monthly shipper survey bears that out. Since 1987, the railroad has polled the same 200 shippers, who each month rate service on a 1-to-5 scale to ensure the survey provides an “apples-to-apples” comparison, says Koraleski. In October, the Class I obtained an 81 percent approval rating — its best since 2003.
“The last two to three years, the top three shipper concerns have been consistency, transit time and service reliability,” says Koraleski. “For the first time, all of them have dropped out of the top three. Now, pricing is No. 1.”
Bank of America Securities’ fourth-quarter shipper survey also shows UP is making strides, yet remains a work in progress. In the poll of about 1,400 shippers released in late November, 52 percent of the respondents who use western carriers said UP’s service had improved and 32 percent believed its service had worsened.
Shippers appear to have a “love-hate” relationship with the Class I, Bank of America Securities analysts said in a survey summary: “Such volatility evidences the fits and starts of the operational situation at UP.”
Matchmaker
One thing UPers are working on to improve operations and bring shippers into the service-design equation is the Customer Inventory Management System (CIMS), which the railroad launched in 2004. The initiative helps ensure “we switch cars when we say we will switch them,” says Koraleski.
CIMS is a car demand management process designed to match car flow to and from customer facilities with track capacity at those locations to reduce switching, improve throughput and decrease terminal dwell time. Since 2006, CIMS has been rolled out to about 6,000 customers and has helped UP reduce average dwell time about 10 percent from 27.9 hours to 25 hours.
“It’s a good way to manage inventory on hand and en route,” says Duffy, adding that UP’s industrial spot/pull average has improved from below 80 percent to the mid-90s.
The railroad also is implementing the Total Car Management System to complement customer service improvements, he says. The general car order handling system is designed to minimize ordering complexity for shippers and improve empty car processing.
“It provides more visibility for us and them,” says Duffy.
When it comes to gaining a clearer picture of the network and the steps needed to keep it clear, the Unified Plan is key.
An ongoing network simplification process launched in 2005, the plan aims to eliminate mainline work events and reduce intermediate switching events. As part of the plan, traffic managers use network modeling software to more accurately forecast network impacts.
Since 2005, the Unified Plan has helped UP reduce total work events by 23 percent, cut total switch events by 9 percent, and trim through-train starts by 5 percent. In October alone, train starts dropped 9 percent even though volume rose 1 percent, says Duffy.
Process change is a primary plan goal. The Unified Plan prompted managers to relocate automotive-related humps from Bailey Yard to a Cheyenne, Wyo., yard, freeing up about 15 percent of the North Platte facility’s capacity, says Duffy.
The point of the matter
Another way to gain capacity is to operate more point-to-point trains. In late 2006, UP began offering the Pipeline Express to pipe shippers. Cargo moves in a 55-car unit train to “funnel freight to destination,” saving six to eight days in cycle time, says Koraleski.
About 90 percent of UP’s pipe business now moves on unit trains vs. 50 percent in 2005. And last year, the railroad handled 7,800 carloads of pipe vs. 1,700 carloads in 2005.
UP is scoring similar cycle time successes with lean management initiatives.
Trimming the fat
For the past three years, the railroad has pursued lean processes, which are all about “reducing the time spent around key assets,” says Vice President of Continuous Improvement Richard McClish.
For example, mechanical department managers have implemented process changes at diesel shops to reduce the time locomotives spend in the facilities. The result: UP now has the equivalent of 60 more locomotives operating in the network at any given time, says McClish.
Managers created “flow” or “swim” lanes under which locomotives are placed in shop lines based on estimated repair time — either eight to 18 hours, 18 to 36 hours or more than 36 hours — to keep work flowing. Shops now receive diagnostic reports on each locomotive 12 hours before the power arrives at a shop so managers can “better plan parts and work,” says McClish.
“We’re also training people to do a better job with diagnostics,” he says. “We’re not getting as many surprises when it comes to locomotive repairs.”
In addition, UP has implemented lean techniques to reduce run-through train servicing time at yards.
At Bailey Yard, NASCAR-like “pit crews” comprising electricians, machinists, firemen, oilers and car inspectors service trains in tandem to speed up the process. At other yards, workers have come up with process-change ideas — such as using a standard light bulb stationed at a service rack instead of retrieving a special bulb from a storage area — to hasten train servicing, says McClish.
“It’s a lot of small things that can get in the way,” he says. “We’ve gotten 25 to 30 percent reductions in train dwell time.”
In 2008, lean management will shift from compiling small ideas to analyzing the big picture. UP will implement 20 corridor projects to improve train flow.
“We’re determining what we need to do now to accommodate demand in 2010,” says McClish.
Techno-logical breakthrough
Adopting technology ranks high on that to-do list. UP continues to pursue technological change in just about every
department to boost productivity.
In late 2008, the railroad will begin phasing in a computer-aided dispatching (CAD) system upgrade to better integrate road planning with yard management systems. Managers expect to complete the transition from a CAD 2.5 to CAD III system by 2010.
“It’s critical that a terminal is available or you get trains that are like planes sitting on a tarmac waiting for take-off,” says Duffy.
UP also is implementing an automated crew calling system to reduce crew assembly time, rolling out automated gate systems at intermodal terminals to cut the time trucks spend at the facilities, and installing more wayside detection systems to identify hot wheels and other component problems to prevent equipment-related train breakdowns.
In addition, the Class I is embracing positive train control (PTC) to notch more efficiency gains. Wabtec Railway Electronics is developing a communications-based PTC system for UP, which is conducting a pilot on lines totaling 333 track miles between North Platte and South Morrill, Neb., and Spokane, Wash., and Eastport, Idaho.
“No one talks much about the fuel savings from PTC,” says Duffy. “We can save 10 to 12 percent on fuel.”
Surging ahead
Although “fuel” is the first word senior execs think of to explain cost increases — diesel expenses are the primary reason fourth-quarter earnings will fall into a lower-than-expected range — “surge” is top of mind when describing obstacles to network fluidity.
UP has gained surge capacity the past few years by expanding its workforce and acquiring locomotives. Since 2002, the Class I has hired 15,000 train, engine-service and yard (TE&Y) workers, boosting the TE&Y workforce 13 percent to more than 22,000.
Last year, the railroad trained 1,900 conductors and 850 engineers, and kept about 450 furloughed TE&Y employees on standby for any potential traffic surge.
Meanwhile, UP has acquired more than 2,000 new locomotives since 2002 — including 300 road units in 2007 — increasing the fleet about 25 percent to more than 8,500 units. The railroad retains about 200 locomotives in storage as “surge protection” units.
In addition to obtaining power as a traffic insurance policy of sorts, UP is acquiring locomotives as part of a “green” push. Last year, the railroad acquired 144 environmentally friendly switchers to reduce air pollutant emissions in yards.
UP is trying to answer a growing rail industry call for environmental stewardship, says Young.
“Customers are not just talking about service and price. They’re seeing the value of rail from an environmental point of view,” he says.
To that end, UP plans to spend $300 million to transform its 20-year-old Los Angeles Intermodal Container Transfer Facility (ICTF) into the “greenest terminal in the world,” says Young.
To be completed in 2009, the project calls for replacing diesel switchers with low-emission “GenSet” switchers, converting diesel-powered equipment — including gantry cranes — to electric-powered machinery, installing a hooded lighting system to direct light away from adjacent neighborhoods and implementing an automatic gate system with optical character recognition to reduce truck idling.
UP also is trying to heed the industry’s — and its own — call for additional capacity. Exhibit A: double tracking the key L.A.-to-El Paso, Texas, Sunset Route. Last year, the railroad spent $260 million to expand the 760-mile route’s capacity by adding 39 miles of second mainline. By 2011, the entire corridor should be double-tracked pending the resolution of permitting and regulatory issues in Arizona.
In addition, UP last year built a third main track traversing Bailey Yard, added an intermodal ramp at its Salt Lake City terminal, and double tracked the Gasconade Bridge between Kansas City, Mo., and St. Louis.
UP also spent more than $20 million to expand ethanol traffic capacity. For example, the railroad constructed an unloading facility in Dallas that can unload an 80-car train in 24 hours and upgraded a Selby, Calif., unloading terminal to handle 30 vs. 10 cars.
This year, UP plans to open a new San Antonio intermodal terminal. To be completed in November, the $90 million facility initially will handle 100,000 trailers annually, then eventually be expanded to accommodate 250,000 trailers and containers.
Pipeline principles
While constructing more of its own facilities, UP is trying to boost industrial development along its lines — but not attract new plants that’ll hinder the Class I’s fluidity quest, says Koraleski.
UP has tightened guidelines for shippers to open a facility on its lines, such as by requiring a 9,000-foot siding and ensuring a plant is built along tangent track and not a mainline, he says.
“Prior to 2003, stricter guidelines weren’t at the top of our hit list,” says Koraleski. “But our fluidity is so good now, we don’t want to fill up track and yards.”
As long as senior execs stick to their make a good read/call a good shot credo and workers keep heeding the pipeline principles, UP’s fluidity level figures to continue moving closer to the free-flowing stage. In the meantime, execs are encouraged that the network is at least pipeline-like.
“Our service metrics are very good and there’s a lack of slow orders all over the network,” says Young. “But we need to keep taking out work events. We need to keep finding ways to be consistent.”
Keywords
Browse articles on Union Pacific Bailey Yard terminal dwell rail capacity train velocityContact Progressive Railroading editorial staff.