Stay updated on news, articles and information for the rail industry
January 2025
Rail News: Union Pacific Railroad
Union Pacific continues to rev up safety, service to speed toward a desired finish line — becoming North America's best railroad
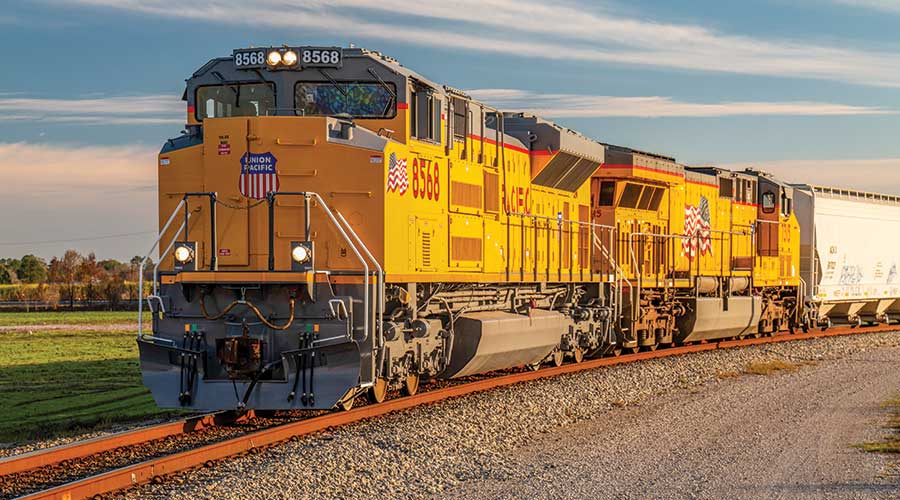
By Jeff Stagl, Managing Editor
On Dec. 6, Jim Vena was spending a chunk of his day signing dozens of Christmas cards for Union Pacific Railroad employees. The Class I’s CEO lifted up a box to show a large cluster of unsigned cards that were to be distributed to senior executives and others at UP’s headquarters in Omaha, Nebraska.
Vena seemed destined to develop writer’s cramp, but he shared a reason why he believed that was unlikely. “I’m ambidextrous,” he says. He’s not — he was just kidding.
What Vena doesn’t kid about is a strategy he’s trying to carry out at UP that’s crucial to the railroad’s present and future success. It’s something that will take many hands to accomplish, including Vena’s guiding hand.
Shortly after he became UP’s CEO in August 2023, Vena helped institute a “Safety, Service and Operational Excellence = Growth” strategy. The idea: lay out a “new vision for success” that can be understood and/or carried out by all UP constituents, such as employees, customers and shareholders, Vena says.
Through the ongoing strategy, the Class I aims to attain best-in-class safety; consistently deliver solid service performance; better engage workers and stakeholders; drive decision-making to those closest to the work; and use resources more wisely, including a new built-in resource buffer to handle unexpected events. If that overriding mission is carried out, UP will be able to grow volumes at a higher clip while continually improving safety, operations and productivity. In addition, the Class I’s ultimate goal will come closer into view: becoming North America’s best railroad by any measure, including safety and service.
Before Vena arrived, 2022 was not a good year for the railroad. Although freight revenue climbed 14% year over year, volume increased only 2% after rising 4% in 2021.
Moreover, UP’s operational performance was lagging. On a comparative basis with 2021, freight-car velocity as measured by daily miles per car was in the low 190s (versus the upper 190s); intermodal trip plan compliance as defined as on-time containers was in the low-70% range (versus closer to 80%); locomotive productivity as calculated by gross ton-miles per horsepower day was in the low 120s (versus about 130); and workforce productivity as measured by daily miles per full-time employee was a little more than 1,000 (versus about 1,050). As a result, many customers were displeased with the so-so service.
Things needed to change so UP could operate as a more well-oiled machine and recapture its allure to retain more customers while attracting new ones. Getting employees to work more in lockstep, promoting solid decision-making and instituting more checks and balances have helped so far, says Vena.
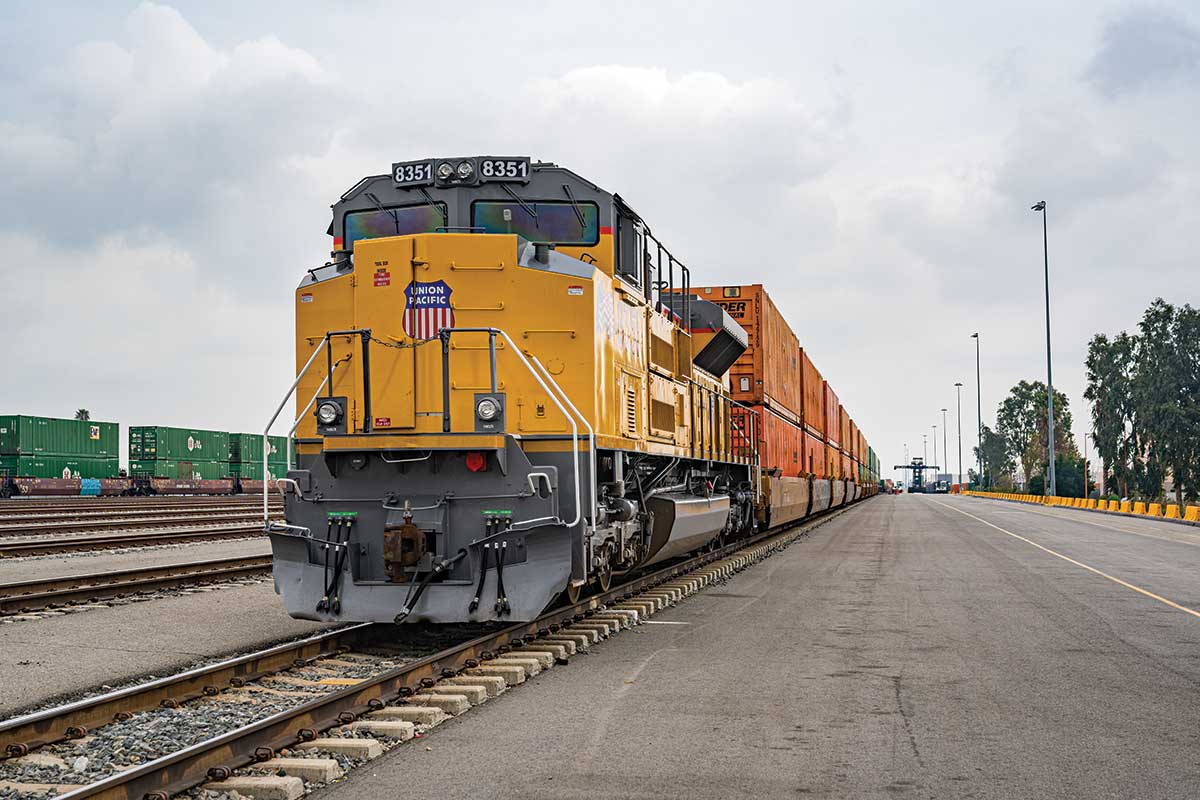
“We need to be clear in communications, to be responsive and make good decisions, and we need to be honest about what we can do,” he says. “It’s important to use facts when making decisions and not what you think can be done. Customers can see [the difference].”
The difference more customers are noticing these days? UP’s service is more consistent and reliable across the network. In last year’s third quarter, the railroad’s service performance index (SPI) showed intermodal trains at 90 and manifest/automotive trains at 87, a 5-point and 4-point improvement, respectively, compared with the third-quarter 2023 SPI.
Now, the railroad is driving to beat its best monthly SPI performance over the past three calendar years.
Smooth(er) operator
Service metrics from late last year also show also show operations are smoother. As of mid-November 2024, freight-car velocity had reached 216 miles per car per day versus 203 in Q1; average terminal dwell time had dropped to 22.1 hours compared with 23.5 hours in Q1; and locomotive productivity had climbed to 138 gross ton-miles per horsepower day versus 135 in Q1. With better fluidity, UP was moving about 168,000 carloads per week at points in Q4 compared with 153,000 carloads in Q1.
“We need to provide what we sold to the customer — not what Jim Vena thinks is good service, but the service we sold to the customer,” says Vena. “Service performance has been high. We measure to what we sold the customer.”
And if service isn’t measuring up, Vena wants to know about it — right from the source’s mouth.
“I give customers my cell number and tell them to call me if we are not delivering as promised,” he says. “I have gotten some of those calls.”
But a lot fewer than in the recent past. The Class I instead is earning some recognition from shippers for its service-improvement efforts.
C.H. Robinson recently named UP its Railroad Carrier of the Year for the second straight year and United Parcel Service (UPS) honored the Class I for perfect peak-season performance. The railroad met all its service commitments to UPS, which is one of UP’s largest customers.
Yet, there’s no time to rest on laurels, UP senior executives say. The railroad needs to continue proving its worth to shippers.
An unexpected A-minus
Some evidence that “operational excellence” measures are working — that can be used to win over skeptical customers — occurred in last year’s third quarter. UP unexpectedly experienced a 33% surge in international intermodal volume that mounted in August and September 2024.
Typically, such a flood of traffic when a railroad isn’t prepared to move it often spells trouble for operations. But UP employed a buffer of resources (locomotives, rail cars and workers) that helped keep trains moving efficiently and maintained fluidity.
Service and operational efficiency gains coupled with the buffer enabled the railroad to handle 6% more volume in the third quarter on a year-over-year basis.
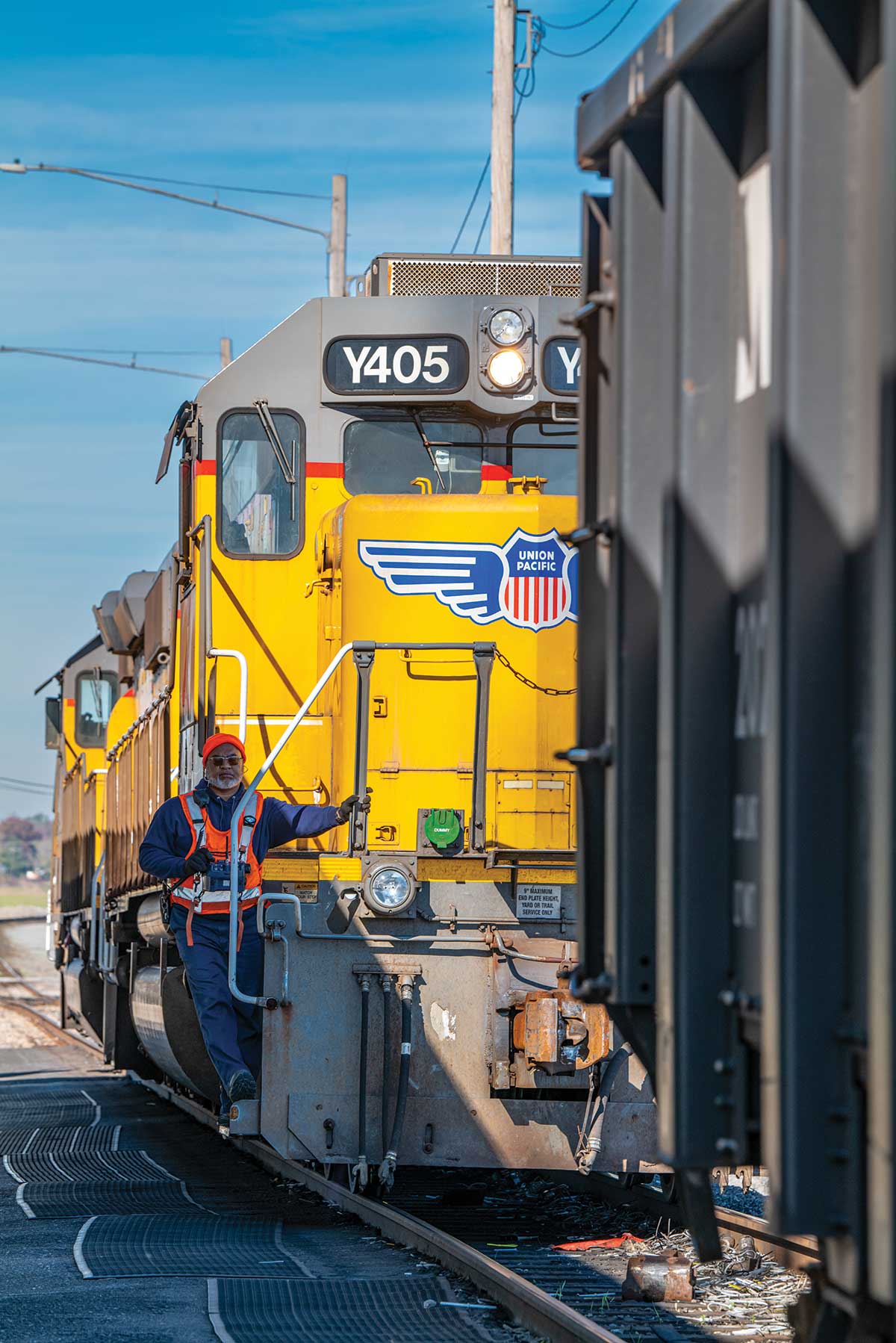
“We handled that [spike] well, and we want to build on it,” says Vena.
The buffer includes about 500 extra locomotives, several thousand extra rail cars and a couple hundred extra workers spread throughout system, says UP Executive Vice President of Operations Eric Gehringer. In addition to traffic surges, the buffer can help the railroad better deal with severe weather and other unpredictable events.
“The buffer reserves were big. There were no indicators to tell us that would happen with our international volume. No one’s volume suddenly grows 30%,” says Gehringer. “I give us an A-minus on how we handled it. We saw the flexibility we need for customers.”
Senior executives now are hearing more compliments from customers about UP’s service.
“They appreciate how it has improved. It shows we are building trust with customers,” says Gehringer.
Despite recent successes, there are things that still need to be worked on in operations, such as day-to-day actions and processes, he says. In addition, more refinement is necessary with agility, or the ability to handle volume surges.
“We can also get better at dwell times,” says Gehringer.
For example, hump yard dwell time — or the time it takes between humping the last car for a train and then getting the next cut of cars to the yard’s hump — can be pushed down, he says.
UP also is trying some rather unusual methods to improve operations. Case in point: The Class I last month announced plans for Genesee & Wyoming Inc.’s Central Oregon & Pacific Railroad Inc. to handle local service from UP’s yard in Eugene, Oregon. The move will enable UP to reduce the number of times a rail car is handled, create greater efficiencies, and provide more flexibility and agility for both railroads to meet current customer needs and anticipated traffic growth.
Typically, it takes 20 to 24 hours just to process a car at the yard, says Gehringer.
“This is all about cycle times and taking dwell out of the yard,” he says.
It’s possible the arrangement with the short line could be replicated elsewhere. UP needs to be open to any possibilities when it comes to developing top-line service, Gehringer believes.
“My team tells me all the time that I am purposely dissatisfied. I think we never stop,” he says. “We continue to look for more opportunities to improve.”
Safety remains job No. 1
The same goes for safety. Through 2024’s first nine months, the number of reportable personal injuries and reportable derailments dropped 21% and 14%, respectively, compared with the same 2023 period.
Because of the nature of railroading, safety needs to be top of mind at all times.
“We have 30,000 employees and every day, about 15,000 of them are working out in the field doing something to help our operations. I never forget that,” says Vena.
On average, a UP train can travel around the world 49 times before a derailment occurs. But unfortunately, accidents — and tragic ones at that — can happen quickly.
On Dec. 18, a UP train collided with a truck tractor-trailer at a grade crossing in Pecos, Texas. The train then derailed and struck a nearby chamber of commerce building. The UP engineer and conductor were killed in the collision and several people were injured.
The truck was stuck at the crossing for about a minute prior to impact. The National Transportation Safety Board is investigating the accident.
Ensuring safety continues to improve and be ingrained in the organization will be job No. 1 in 2025, says Gehringer.
To that end, the railroad plans to focus harder on 23 of 3,300 rules workers need to follow. For example, engineering workers — who account for about one-third of UP’s total workforce — can zero in on how they handle materials, says Gehringer.
“We handle a lot of heavy materials, so how we rig it or move it is vital. We do as much as possible with mechanical assistance,” he says.
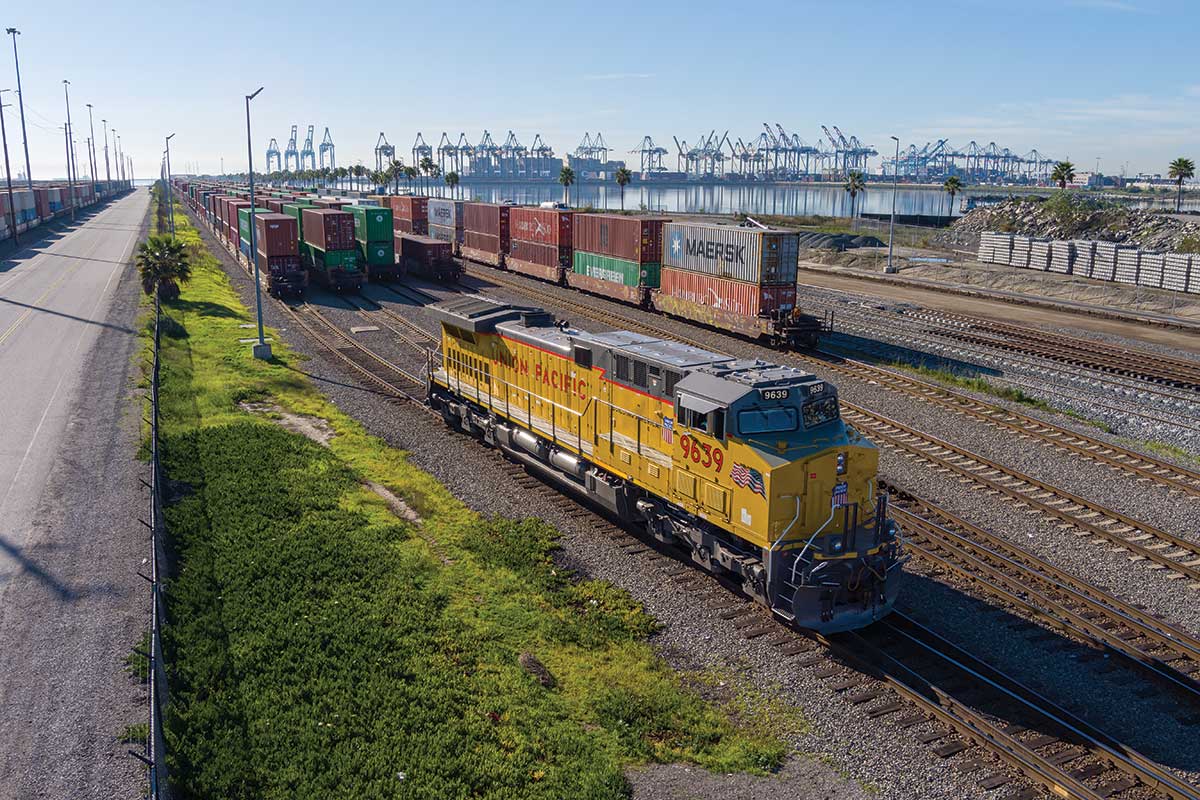
For transportation workers, the goal is to move cars as safely and efficiently as possible.
“The teams are very busy. They need to assess car movements and have situational awareness,” says Gehringer.
There’s something else all UPers need to remain aware of: helping to spur growth. In late 2024, the railroad’s volume was tracking at a 3% year-over-year gain and revenue was on pace for a healthy increase. But everyone in the company needs to help push for more, says UP Executive Vice President of Marketing and Sales Kenny Rocker.
“We are thinking about growth throughout the organization. It takes everyone to make it happen,” he says. “If you are in accounts payable, you think about how a transaction impacts growth. If you are in law, you think about growth, too.”
A stick-to-it mindset
UP moves 100 different commodities, and many of them pose growth opportunities. Even some rather unusual cargo.
For example, UP over the past couple of years has worked with SunTrain in Colorado on a plan to store electrical power in rail cars and move them around the state for distribution instead of building more transmission lines, which are expensive and take a long time to construct.
Rail cars could receive power in Pueblo and then travel to the Denver area or any place in the state that needs electricity. If all planning goes well, the power trains could start rolling in 2031.
“This shows our hustle, our stick-to-itiveness. Some growth opportunities can take a long time, not just weeks or months,” says Rocker.
UP also pursues more dimensional freight — or “high and wide” loads — that aren’t necessarily frequent, but can be lucrative.
“This can be one-time loads like heavy equipment or a tank for training for the Army. We have moved rockets in the past,” says Rocker. “We want to be as creative as we can be. Moves like this show our creativity and ingenuity.”
In terms of heavier-volume traffic, Rocker is most bullish about the potential to grow business with biofuels, such as ethanol; over-the-road traffic (OTR) diversions; petrochemicals, especially along the Gulf Coast; and traffic generated in Mexico.
“We don’t just want to trade OTR share with other railroads, but get a larger size of the pie and make the pie bigger,” says Rocker. “We have unrivaled infrastructure for petrochemicals on the Gulf Coast, which allows us to grow.”
And Mexico is a big growth factor. There’s been a structural shift in export grain moving from the Pacific Northwest and Asia to Mexico, and intermodal business has been strong in Mexico, says Rocker.
UP can take advantage of its six gateways between the United States and Mexico. In addition, UP offers the shortest route between Chicago and Mexico.
The Class I’s stronger service product is helping to attract beneficial cargo owners, says Rocker.
“We go after small- to medium-sized shippers that aren’t using rail,” he says. “We have marked 30 years of doing business in Mexico, so we are mature there.”
Some autos produced in the Gulf Coast region will head to Mexico, as well. For example, Volkswagen Group of America last year opened a vehicle processing center in Freeport, Texas, that’s served by UP. The railroad helps VW distribute imported vehicles to about 300 dealerships mostly located across the central and western U.S.
The $114 million, 120-acre facility — which features 53 rail-car spots and can annually process up to 140,000 VW, Audi, Bentley, Porsche and Lamborghini vehicles — will mainly be used to import vehicles from Europe and Mexico, where VW and Audi operate large assembly plants.
“The Volkswagen facility is a big win for us,” says Rocker. “We aggressively go after every carload, because every carload matters.”
Spend money to make money
That approach plays into capital investments UP continues to make. Over the past 10 years, the Class I has spent more than $33 billion on capital improvements in its network, including $3.4 billion in 2024. Each day, the railroad averages nearly $10 million in capital spending. A lot of the dollars are targeted at growth initiatives.
Recent investments include four new intermodal ramps, five new autonomous wide-span cranes and seven new “focus sites” or industrial parks, which provide businesses and warehouses easier access to UP’s 32,000-mile network.
Focus sites are large-scale developments suited for custom-built warehouses or industrial facilities located next to tracks. The sites make it easier to access rail while increasing a customer’s speed to market. UP currently has more than 30 focus sites, including five that were added in 2024.
A recent focus site-related industrial development win involves a new distribution center for Chick-fil-A Supply that opened late last year in UP’s 3,300-acre Prime Pointe Industrial Park near Hutchins, Texas. The first rail-served distribution center operated by Chick-fil-A Supply, it receives potato products (mainly waffle fries and hashbrowns) nearly daily from Oregon.
The facility — which opened in September — averages about six rail cars a day, each carrying the equivalent of three truckloads of products. The facility removes more than 100 long-haul trucks off roads each week, UP officials say.
The Class I also aims to meet new market demands by identifying fast-growing areas for investment and developing new intermodal ramps. Over the past four years, the railroad has built new intermodal ramps in Phoenix; Minneapolis; and near Los Angeles in the Inland Empire. A fourth ramp is under construction in Kansas City, Missouri, and is expected to open this year.
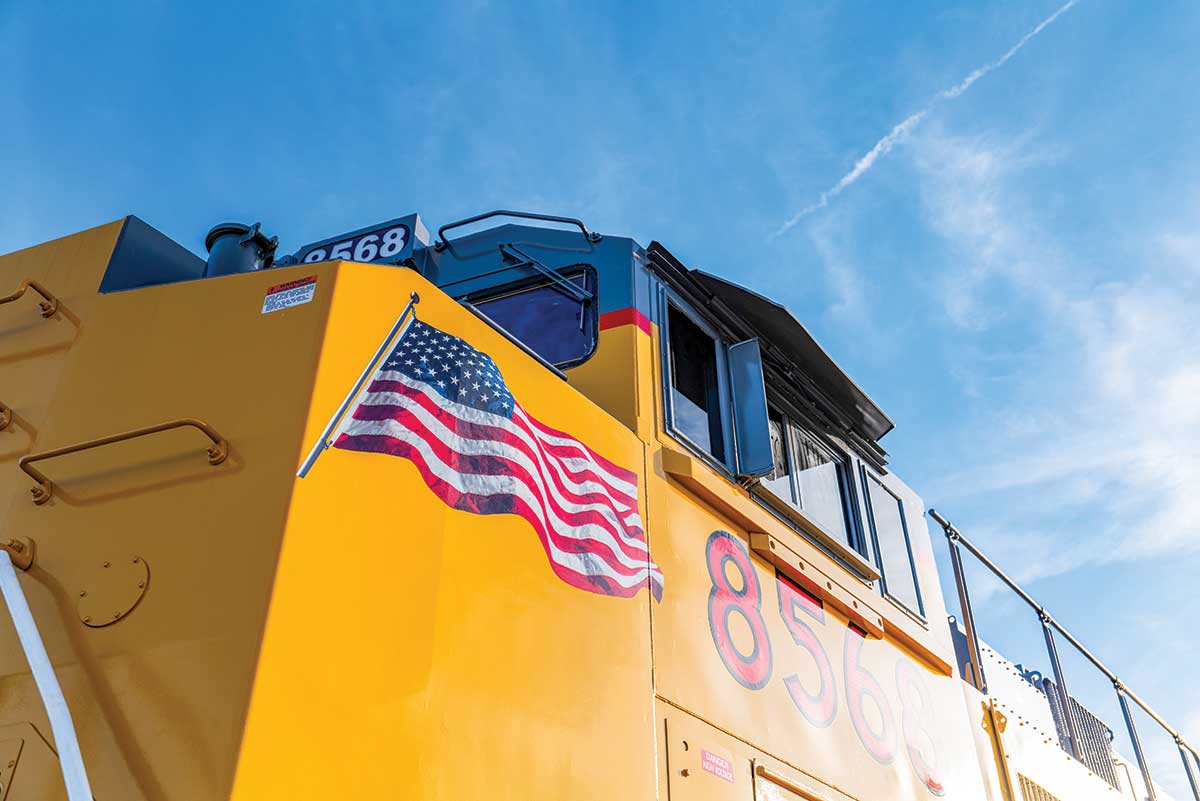
Via new ramps and enhancements completed at existing ramps, UP has added nearly 1 million units in incremental lift capacity since 2021. In all, the Class I operates 32 ramps in the nation’s most in-demand cities.
The combination of investments and operational improvements are helping to build business, says Rocker. In 2024, UP launched nearly 100 business development campaigns to generate sales leads and maintained a strong pipeline of new and incremental business opportunities totaling more than $1 billion.
“With good service good to go, we say to customers, ‘Give us one or two more carloads a day.’ That’s how we go after it,” he says. “You take those one or two carloads and add them up over 365 days and over many shippers, and that adds up.”
The technological connection
UP also is committed to making more investments in technology as part of its higher-growth and better-service pursuits. Here are some examples:
- In 2024, the railroad rolled out a new invoice management tool that offers a new and improved interface for customers to view, search, download and dispute invoices. The invoice management tool is a one-stop service for all invoice-related needs, driving better visibility and creating efficiencies for all customers;
- Precision gate technology employed at intermodal terminals provides more efficient access to and from the facilities and reduces the time it takes truck drivers to find and drop off containers;
- GPS devices have been installed on containers for conducting real-time tracking, identifying threats and mitigating potential thefts; and
- A UPGo mobile application provides truckers better in-gate and out-gate validations, ramp navigation and problem resolution processes at terminals.
“I [recently] spent nearly a day with a trucker in Chicago and they liked how UPGo is so integrated,” says Rocker.
Another prime example of better operations through technological adoption is Precision Train Builder (PTB). For the past several years, UP has employed PTB, a train physics algorithm the Class I developed with its PS Technology subsidiary, to more optimally assemble trains.
It simulates trains and their operations over hundreds of miles of track compressed into minutes and can accurately identify not only where to place rail cars within a train, but how much power to use and where to place the locomotives for the most efficient and safest operation.
Engineers continually provide feedback on PTB, which is used to tweak and refine the algorithm. There’s an additional safety benefit, as well: PTB is used to monitor train crews in real time, and issues alerts to crew members when necessary, such as to slow down.
All the moves that UP is making are resulting in speedier, safer and more consistent operations. And that’s increasingly drawing more customers’ attention and interest.
“They appreciate our responsiveness and how we make decisions quickly. We have made the organization flatter so we can make decisions faster,” says Rocker.
Plus, more workers better understand the company’s strategy and their role in executing it. UP recently conducted an employee survey that showed a 35% improvement in the number of workers who stated they have a good grasp on the vision of success, says Vena. In addition, more said they comprehend how they fit into the vision.
To recognize employees who have excelled at helping the company execute the strategy, UP is introducing the inaugural CEO Excellence Awards. The honor will acknowledge both individuals and teams.
The challenge now is to maintain the momentum the railroad has taken time to generate. With so many ducks in a row, UP is set up to win, Vena believes. And the payoff could be high by capitalizing on that prime positioning.
“When we ask someone what’s the best railroad in North America, we want to be the answer, to be that railroad,” says Vena. “I don’t mean to be a bragger. But we are starting to take that next step.”
Email questions or comments to jeff.stagl@tradepress.com.
Keywords
Browse articles on Union Pacific Railroad Safety Service and Operational Excellence = Growth Jim Vena Eric Gehringer Kenny Rocker service performance index rail safety intermodal resource buffer Genesee & Wyoming Inc. Central Oregon and Pacific Railroad SunTrain Volkswagen Group of America Chick-fil-A Precision Train Builder UPGoContact Progressive Railroading editorial staff.